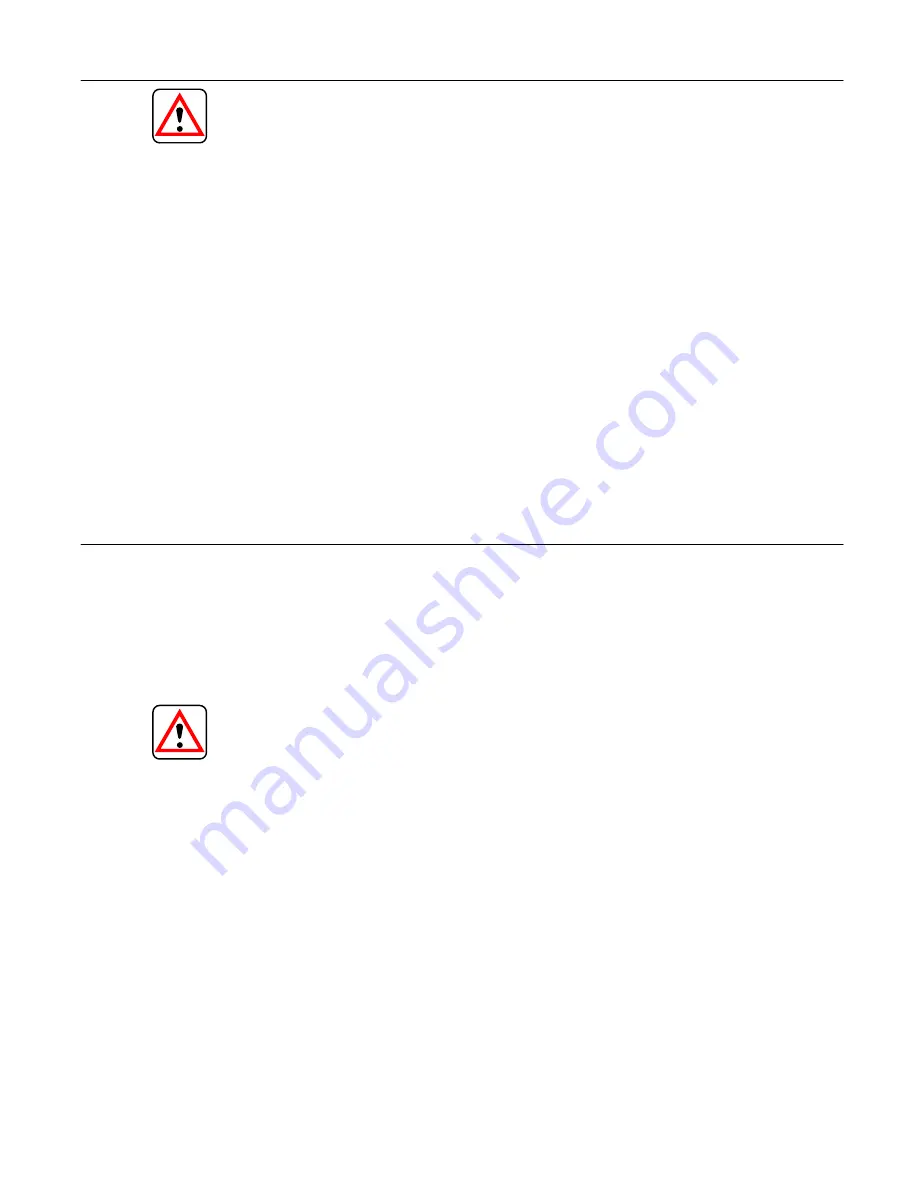
7
CAUTION
Over-lubrication can damage the shaft seal.
C. Routine Inspection and
Maintenance
1. Make certain all hydraulic connections are tight to
prevent fluid leakage or entry of air into the system.Complete
overhaul may be accomplished by means of cartridge and
gasket kits.
2. Check fluid level in the reservoir to assure an
adequate supply to the pump intake. When adding fluid,
always pour it through a 200 mesh or finer screen.
3. Inspect the filter element and replace if dirty.
4. Inspect the fluid for contamination. If contaminated,
drain the system and thoroughly clean the reservoir. Change
the filters and flush the complete system with new fluid.
Again drain the system and refill with new fluid.
5. Check the reservoir air breather and replace if dirty.
D. Product Life
The longevity of these products is dependent upon environ-
ment, duty cycle, operating parameters and system clean-
liness. Since these parameters vary from application to
application, the ultimate user must determine and establish
the periodic maintenance required to maximize life and
detect potential component failure.
Section IV – Overhaul
A. General
Complete overhaul may be accomplished by means of car-
tridge and gasket kits.
B. Disassembly
Disassembly may be accomplished in the order shown in the
illustration (Figures 3 or 4).
WARNING
Before breaking a circuit connection, make certain
that power is off and system pressure has been
released. Lower all vertical cylinders, discharge
accumulators, and block any load whose movement
could generate pressure.
Prepare a clean, lint-free surface on which to lay internal
parts of the pump. Thoroughly clean areas adjacent to the
components being removed to minimize possibility of dirt
entering the system. Cap or cover all exposed ports and
openings into the system.
Inspect and replace as follows:
1. Vanes, for wear and sticking in rotor slots. Vanes
must move in slots from their own weight when dry. Replace
if defective. Stone new vanes lightly on an India stone to
remove sharp edges.
2. Ring, for scored or cross-grooved cam face. Replace
if grooved or scored.
3. Faces of rotor and bushings for wear and scoring.
Remove light scores by lapping; replace if heavily scored.
Stone new parts lightly to remove burrs.
4. Bearings for cracked or pitted races or pitted balls.
Replace if defective.
5. Shaft for wear at seal lip journal. Replace if scored.
6. Replace shaft seal, O-ring and head packing at each
teardown.
C. Reassembly
Assemble parts in reverse order of disassembly, noting the
following:
1. Assembly seals with spring toward inside of the
pump.
2. Coat all parts with compatible fluid and lightly
lubricate the lip of the shaft seal to prevent damage during
installation.
3. Install bearing and snap ring on shaft end and place
in the body.
4. Spring in the shaft seal must be toward the shaft
bearing.
5. Install cartridge parts so arrows on the parts are
pointed for intended rotation as viewed from the shaft end.
6. Assemble the pin so its small diameter end fits into
the body for right hand rotation (large end in body for left
hand rotation). See installation page 5.