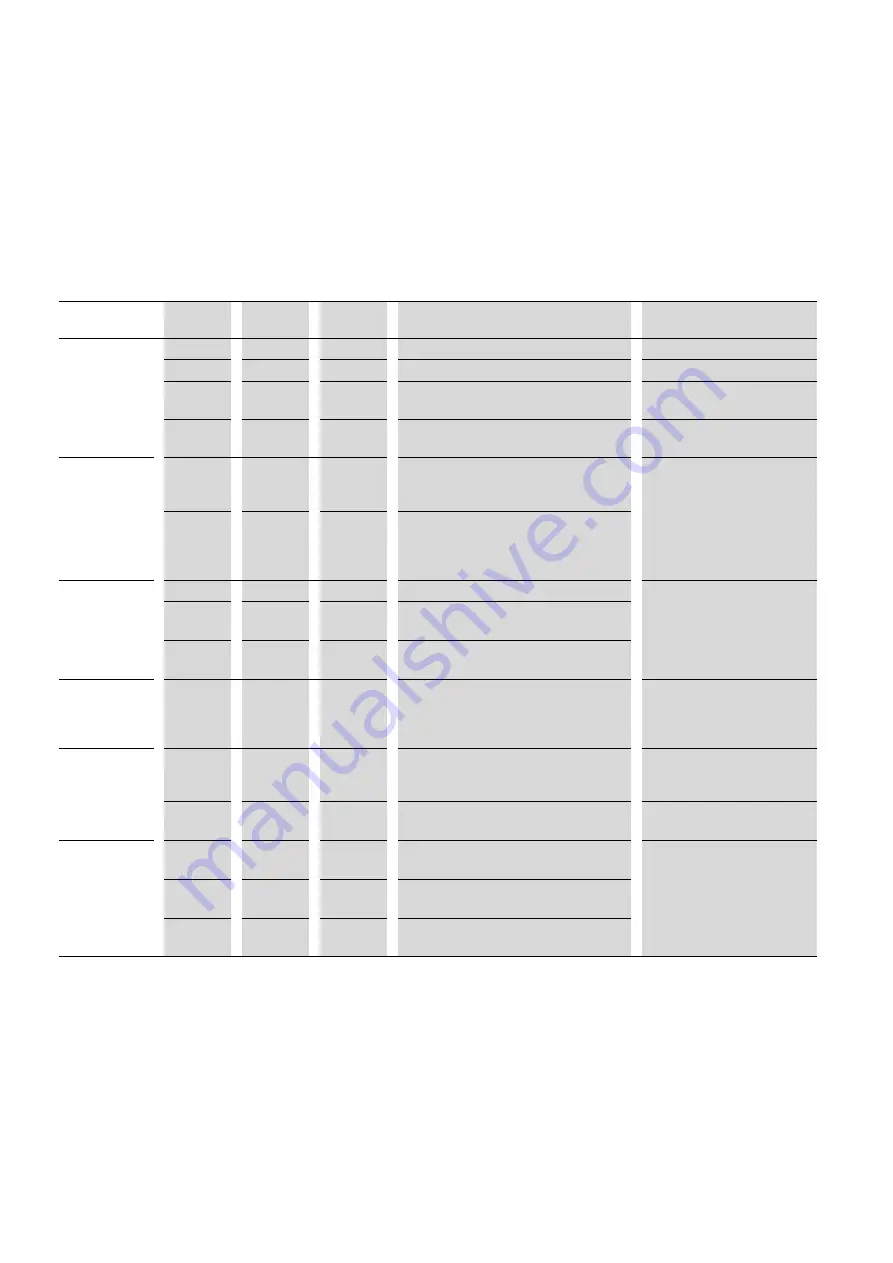
9 Diagnistics
20
ESR5-NV3-30
12/19 MN049010EN
www.eaton.com
9 Diagnistics
○
– LED o
ff
●
– LED
fl
ashes
Table 1: Diagnostic description
Power
K1/K2
K3(t)/K4(t)
Fault
Remedy
Connection/
voltage error
○
○
○
Supply voltage not present.
Apply supply voltage.
★
○
○
Supply voltage too low.
Adjust supply voltage.
★
1 s
○
○
Supply voltage too high.
Adjust supply voltage.
★
○
○
The enable circuits are connected incorrectly
or not connected at all.
Check the connection of the
enable circuits.
Cross-circuit
★
1 s
○
○
Between both enable circuits S11-S12 and
S21-S22.
E.g., for emergency stop or safety door.
Remove cross-circuit.
★
○
○
Between enable circuit S12-S22 for applica-
tions with light grid and safe PLC.
Fault is detected and indicated by the light grid/
PLC.
Short circuit
○
○
○
Between contact points A1 and A2.
Remove short circuit.
★
1 s
○
○
Between S11 and S12.
Error detection on next demand.
★
1 s
○
○
Between S21 and S22.
Fault detection on next demand.
Fault in reset
circuit
★
1 s
○
○
Faulty reset button.
Short circuit between A1 and S34.
No fault detection on initial start, only once all
enable contacts have been opened.
Remove short circuit.
Configuration
error
★
1 s
★
1 s
○
If a cross-circuit or overvoltage/undervoltage
occurs during the configuration phase, the
safety module indicates a configuration error.
Check the wiring and the operat-
ing voltage supply.
Perform a voltage reset.
★
1 s
★
1 s
★
1 s
Rotary switch (delay time) was modi- fied.
Perform configuration again.
Fault with
internal cause
★
0,2 s
○
○
Safety relay faulty.
Replace safety relays. Perform a
voltage reset.
★
0,2 s
○
○
Enable contact(s) of K1 and K2 faulty.
★
0,2 s
○
○
Enable contact(s) of K3 and K4 faulty.
Summary of Contents for ESR5-NV3-30
Page 1: ...Manual ESR5 NV3 30 Safety relay 12 19 MN049010EN...
Page 4: ......