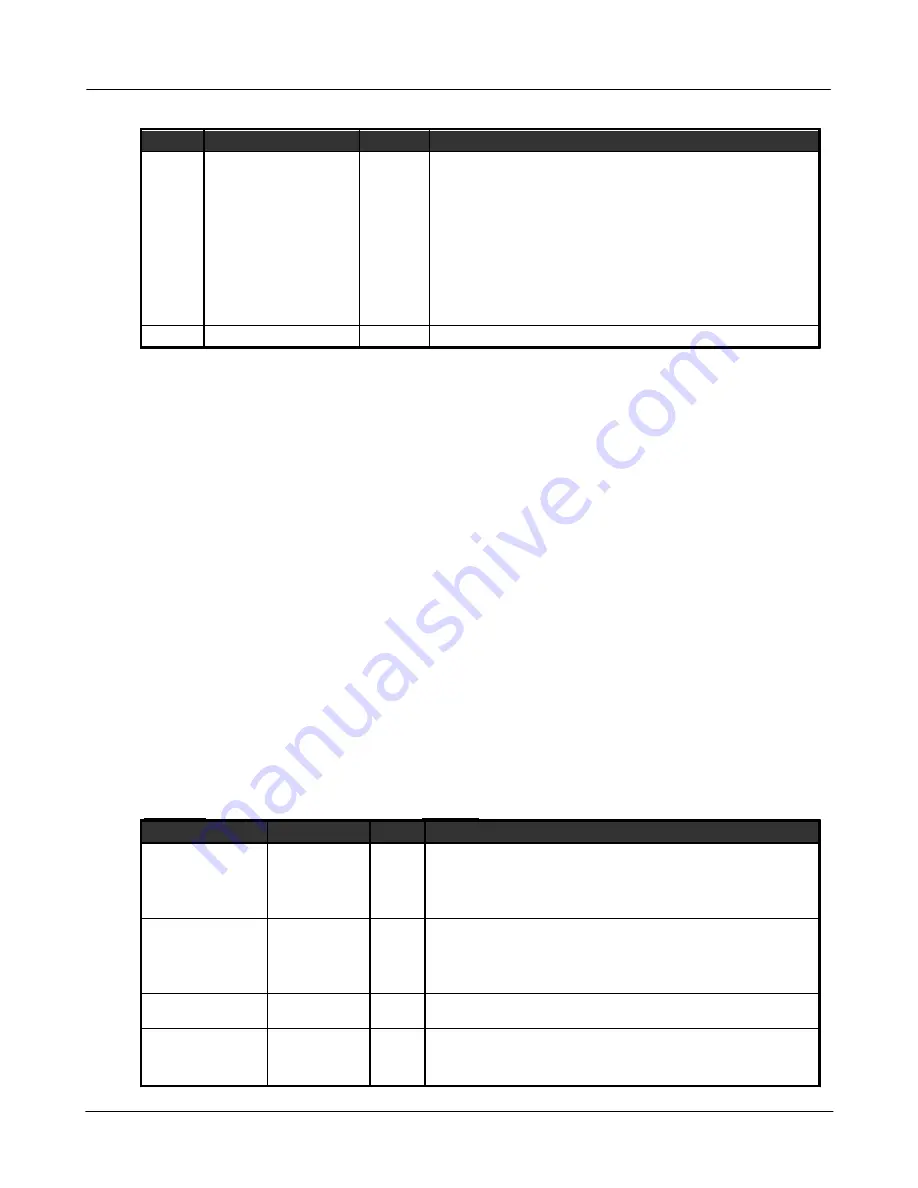
Settings
63
© 2019 DynaGen Technologies Inc
TOUGH Series Manual
Name
Range
Default
Description
Timeout
0 ~ 120 minutes in 1
minute increments
10 min
How long after the password is entered before the user is required to
enter it again.
The timeout is implemented as a simple countdown timer. The
following apply:
·
If the bypass time is changed this new bypass time will not be
loaded until the countdown timer has expired and the user enters the
password.
·
The countdown timer is stored in non-volatile memory and is
"paused" when the controller is powered off. The counter will
resume when the controller is powered on again.
·
Any button press in the menu will reset the timer.
Passcode 0000 ~ 9999
0000
The four numeric digits that make up the password.
4.8.2
Settings Name
If storing settings from the RapidCore Configuration Software a custom name can be entered to allow users to determine the
settings that are stored in the controller. This custom name, called "Configuration Name" (ID in the controller) is found under
Options in the settings tab of the Configuration Software. There is no controller menu to set this ID. It can be up to 12
characters long.
The Configuration Name can be viewed in the Device Info > About TG410/TG350 menu. It is labeled ID.
4.8.3
Process Control
The Process Control feature has two different control methods: Main-In and Main-Out. The Main-In maintains a
reservoir/pressure level by controlling the flow of fluid/gas into the reservoir/tank. The Main-Out maintains a reservoir/pressure
level by controlling the flow of fluid/gas from the reservoir/tank. It does this by regulation the speed of the engine over the J1939
CAN bus.
The process control feature takes over on an engine start once the engine has ramped up to the goal speed (after going
through the idle and intermediate ramping).
The controller reads the sensor value from selected Auxiliary Sensor input (1~4) or Transducer Input (Aux 5), compares the
input value with the set-point, and then, based on an algorithm, increments or decrements the speed (RPM) by a certain
amount (controlled by the Gain and delay settings) to maintain the desired set-point outside of the dead-band area. Control
pauses inside the dead-band area. If the sensor input goes beyond a minimum or maximum value, the algorithm will pause and
the RPM will be maintained at a minimum or maximum value.
The algorithm is a fuzzy logic type control with a dead band and a minimum / maximum saturation. The user sets the
aggressiveness of the control with the
Gain
setting and the response time of the control with the
Delay
setting.
(Front Panel: Other Config > Process Control menu, RapidCore: Pumping Applications > Closed Loop Control)
Name
Range
Default
Description
Closed Loop >
System (Control
Type)
Disabled
Main-In (Maintain
In)
Main-Out
(Maintain Out)
Disabled
Main-In controls the level when pumping fluid into a reservoir. Main-Out
controls the level while pumping fluid out of the reservoir.
Closed Loop >
Sensor In (Sensor
Input)
AUX-1
AUX-2
AUX-3
AUX-4
AUX-5
Aux-5
The Auxiliary Sensor Input function that is providing feedback on the
reservoir level. Aux-5 refers to the Transducer under the Application
menu.
Closed Loop > Delay
1 ~ 30 s in 0.1 s
increments
8.0 s
The sampling time of the control algorithm. This value must be tuned for
each installation.
Closed Loop > Gain
1 ~ 30 in 0.1
increments
19.0
The amount to increment or decrement the RPM when the sensed value
is outside of the dead-band. This number does not represent an actual
RPM. A larger gain will generate a larger RPM change than a smaller
Summary of Contents for Tough Series
Page 4: ...3 2019 DynaGen Technologies Inc TOUGH Series Manual User Guide ...
Page 11: ...Installation 10 2019 DynaGen Technologies Inc TOUGH Series Manual 2 3 Wiring Harnesses ...
Page 12: ...Installation 11 2019 DynaGen Technologies Inc TOUGH Series Manual 2 4 Typical Wiring Diagram ...
Page 17: ...Installation 16 2019 DynaGen Technologies Inc TOUGH Series Manual ...
Page 19: ...Installation 18 2019 DynaGen Technologies Inc TOUGH Series Manual ...