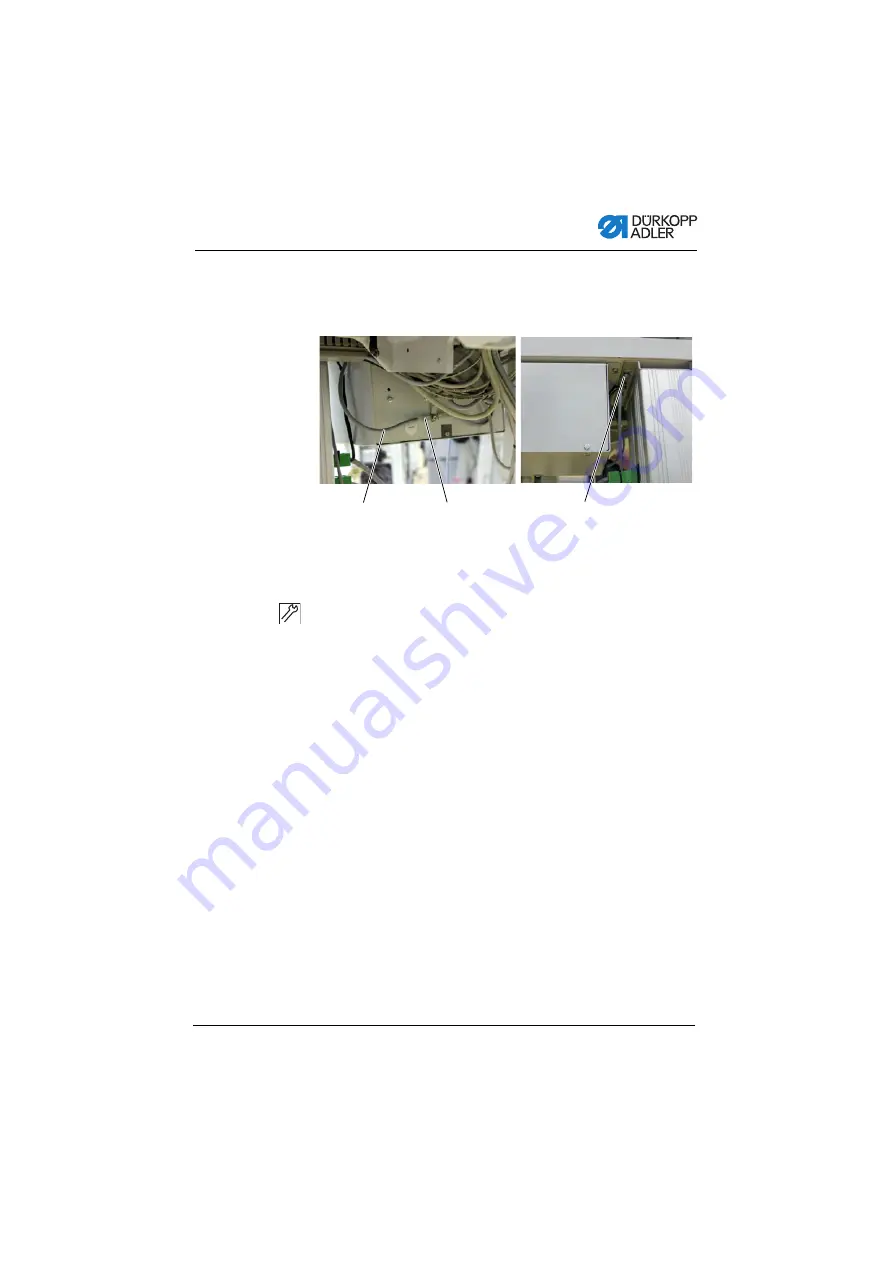
Setup
Operating Instructions 650-16 - 02.0 - 08/2016
125
8.9.7
Connecting the equipotential bonding for the
additional control
Fig. 82: Connecting the equipotential bonding for the additional control
To connect the equipotential bonding for the additional control:
1.
Plug the protective earth conductor (1) into the flat plug (2)
on the additional control cabinet.
2.
Lay the cable (2) (300 mm long) to the control cabinet (3) and
screw it on.
(1) - Protective earth conductor
(2) - Flat plug
(3) - Attachment to control cabinet
①
②
③
Summary of Contents for 650-16
Page 1: ...650 16 Operating Instructions...
Page 6: ...Table of Contents 4 Operating Instructions 650 16 02 0 08 2016...
Page 16: ...Safety 14 Operating Instructions 650 16 02 0 08 2016...
Page 20: ...Machine description 18 Operating Instructions 650 16 02 0 08 2016...
Page 38: ...Operation 36 Operating Instructions 650 16 02 0 08 2016...
Page 104: ...Control with the OP7000 control panel 102 Operating Instructions 650 16 02 0 08 2016...
Page 136: ...Decommissioning 134 Operating Instructions 650 16 02 0 08 2016...
Page 138: ...Disposal 136 Operating Instructions 650 16 02 0 08 2016...
Page 146: ...Appendix 144 Operating Instructions 650 16 02 0 08 2016...
Page 147: ...Appendix Operating Instructions 650 16 02 0 08 2016 145...
Page 148: ...Appendix 146 Operating Instructions 650 16 02 0 08 2016...
Page 149: ......