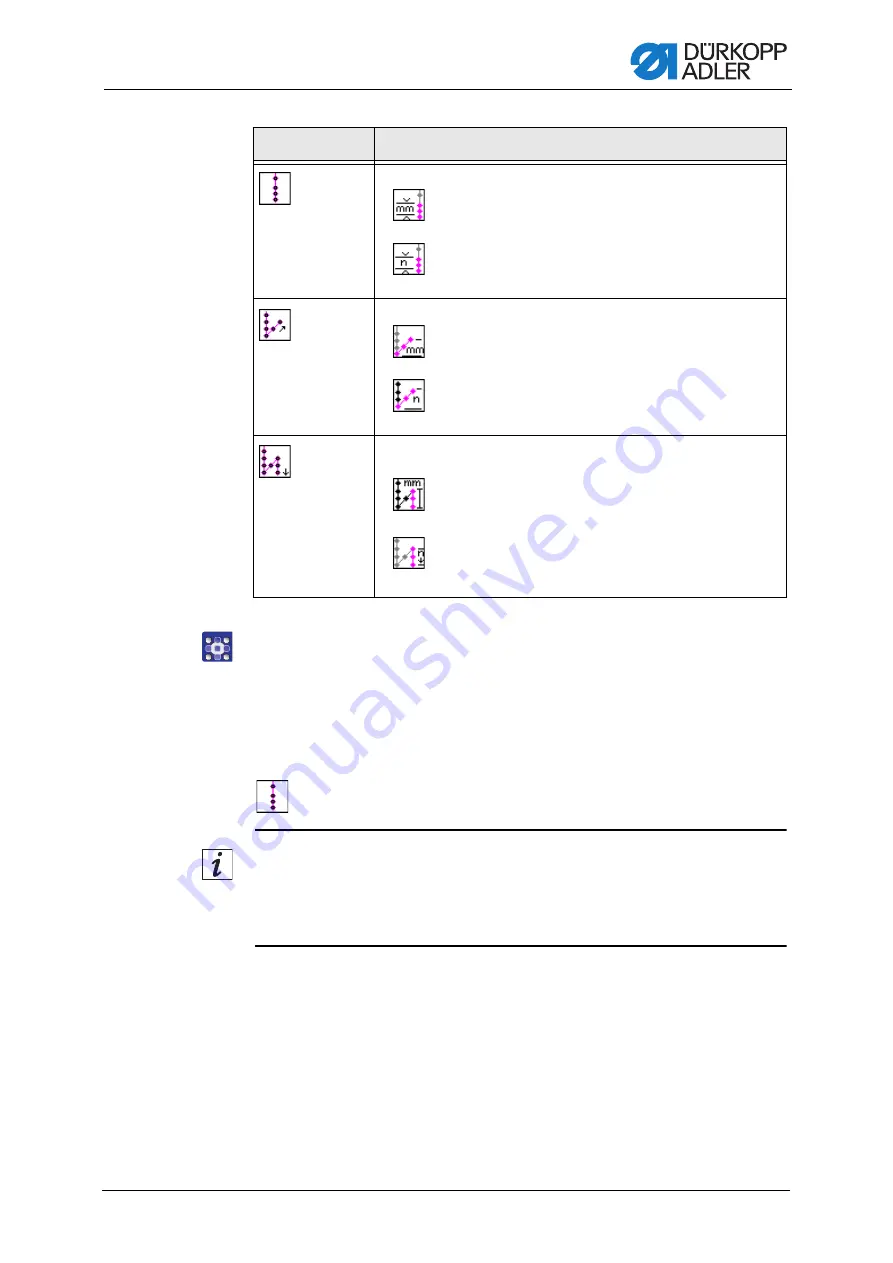
Programming
Service Instructions 745-35-10 D - 00.0 - 10/2017
183
To set the securement of the right seam end:
1.
Press the desired button.
2.
Enter the desired value using the numeric keypad.
3.
Confirm with
OK
.
Set securement seam end right needle
Information
The settings in subitem
Securement seam end right needle
are
adopted automatically from the settings for the
Securement seam end
left needle
Symbols
Meaning
Select stitch condensing
•
Set stitch length for stitch condensing at seam end
(0.5 - 3.5 mm)
•
Set number of stitches for stitch condensing at seam end
(0 - 10)
Select single tack
•
Set stitch length for single tack at seam end
(0.5 - 3.5 mm)
•
Set number of stitches for single tack at seam end
(0 - 10)
Select double tack
• for straight pocket only
•
Set stitch length for double tack at seam end
(0.5 - 3.5 mm)
•
Set number of stitches for double tack at seam end
(0 - 10)
Summary of Contents for 745-35-10 D
Page 1: ...745 35 10 D Service Instructions...
Page 6: ...Table of Contents 4 Service Instructions 745 35 10 D 00 0 10 2017...
Page 10: ...About these instructions 8 Service Instructions 745 35 10 D 00 0 10 2017...
Page 74: ...Machine head 72 Service Instructions 745 35 10 D 00 0 10 2017...
Page 84: ...Transport carriage 82 Service Instructions 745 35 10 D 00 0 10 2017...
Page 116: ...Light barriers 114 Service Instructions 745 35 10 D 00 0 10 2017...
Page 122: ...Aligning the machine head 120 Service Instructions 745 35 10 D 00 0 10 2017...
Page 128: ...Folder 126 Service Instructions 745 35 10 D 00 0 10 2017...
Page 146: ...Throw over stacker 144 Service Instructions 745 35 10 D 00 0 10 2017...
Page 282: ...Programming 280 Service Instructions 745 35 10 D 00 0 10 2017...
Page 292: ...Maintenance 290 Service Instructions 745 35 10 D 00 0 10 2017...
Page 294: ...Decommissioning 292 Service Instructions 745 35 10 D 00 0 10 2017...
Page 296: ...Disposal 294 Service Instructions 745 35 10 D 00 0 10 2017...
Page 308: ...Troubleshooting 306 Service Instructions 745 35 10 D 00 0 10 2017...
Page 337: ......