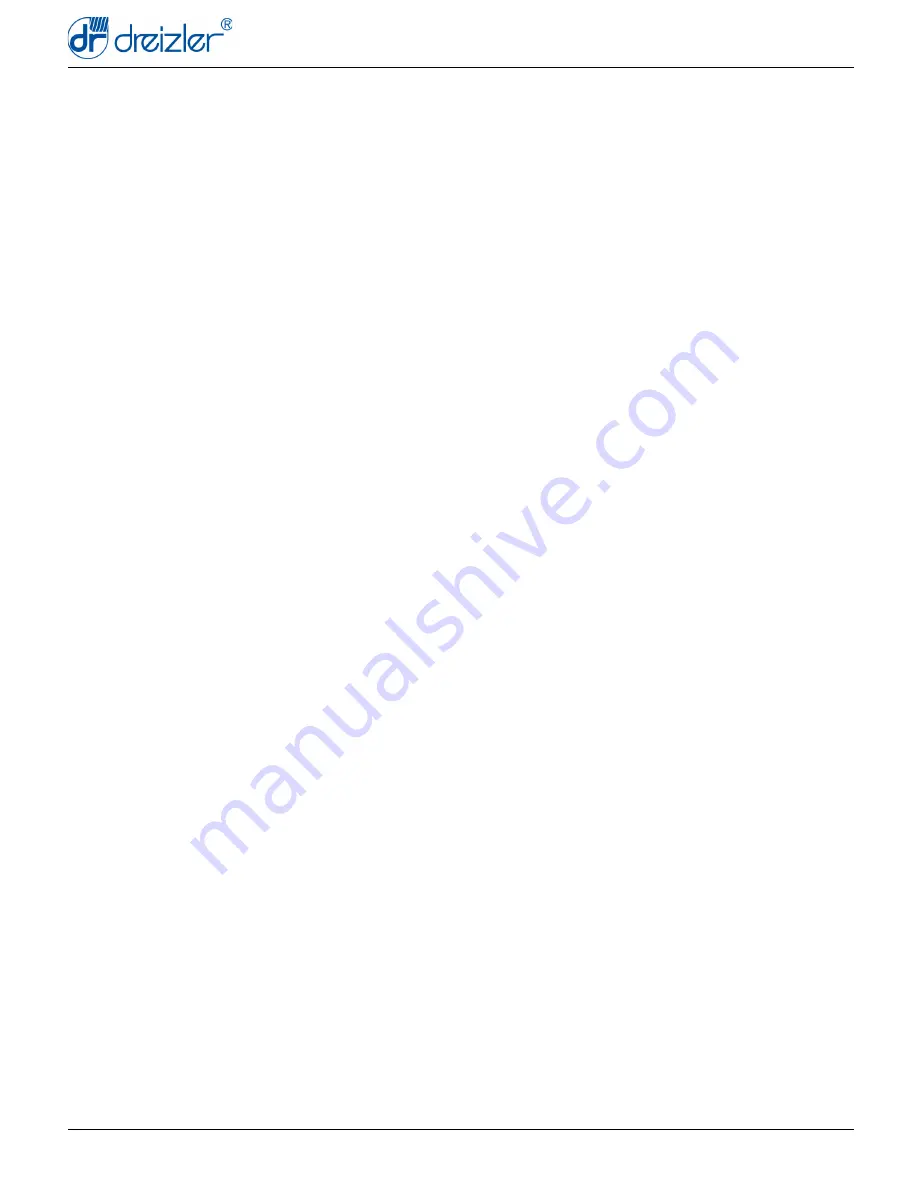
Annual inspection and maintenance
dreizler A 3001 E - 18.12.2015 | A 2006 - 1.15 | EN - 10.12.2015
181
•
TRGI "Technical Rules for Gas Installations"
Relevant EU standards include:
•
EN 676 "Automatic burners with blowers for gaseous materials" and included standards
•
EN 267 "Oil burners with blowers" and included standards
Other relevant EU standards include:
•
DIN EN 303 "Boiler with blower burner"
•
DIN EN 12952 "Water tube boilers"
•
DIN EN 12953 "Shell boilers"
•
DIN EN 13306 "Maintenance terminology"
56.8 Spare parts
Manufacturer spare parts lists include 'spare parts' that must be replaced within the warranty period of a
product, even with intended use compliance. In accordance with accepted business practices, any costs
arising from these replacements do not fall under the warranty provision duties/assurances of the manu-
facturer.
In order to avoid misunderstandings, a subdivision of the offered parts in the list into three categories is
provided:
56.8.1 Spare parts
Definition:
Spare parts are meant for product repair purposes. Parts are replaced that have not reached their expected
lifespan, even though the device was operated within the parameters of intended use. Additionally, parts
are replaced that have been damaged due to operation outside the parameters of intended use or due to
improper operation.
56.8.2 Wear parts
Definition:
Wear parts are parts, which - when used within the parameters of intended use - must be replaced repeat-
edly during the lifespan of the product (e.g. during maintenance).
56.8.3 Auxiliary material
Definition:
Auxiliary material is required during the repair and maintenance of devices. Typical auxiliary materials in-
clude seals of all types or fuses.
Wear parts and auxiliary material are marked accordingly in manufacturer spare parts lists and have an
added note, explaining that a warranty claim will only be accepted, where wear parts must be replaced be-
fore their usual lifespan ends due to reasons that are the responsibility of the manufacturer. Auxiliary ma-
terial is not subject to warranty claims, with the exception of required use in connection with the
replacement of parts within the scope of an existing warranty agreement.