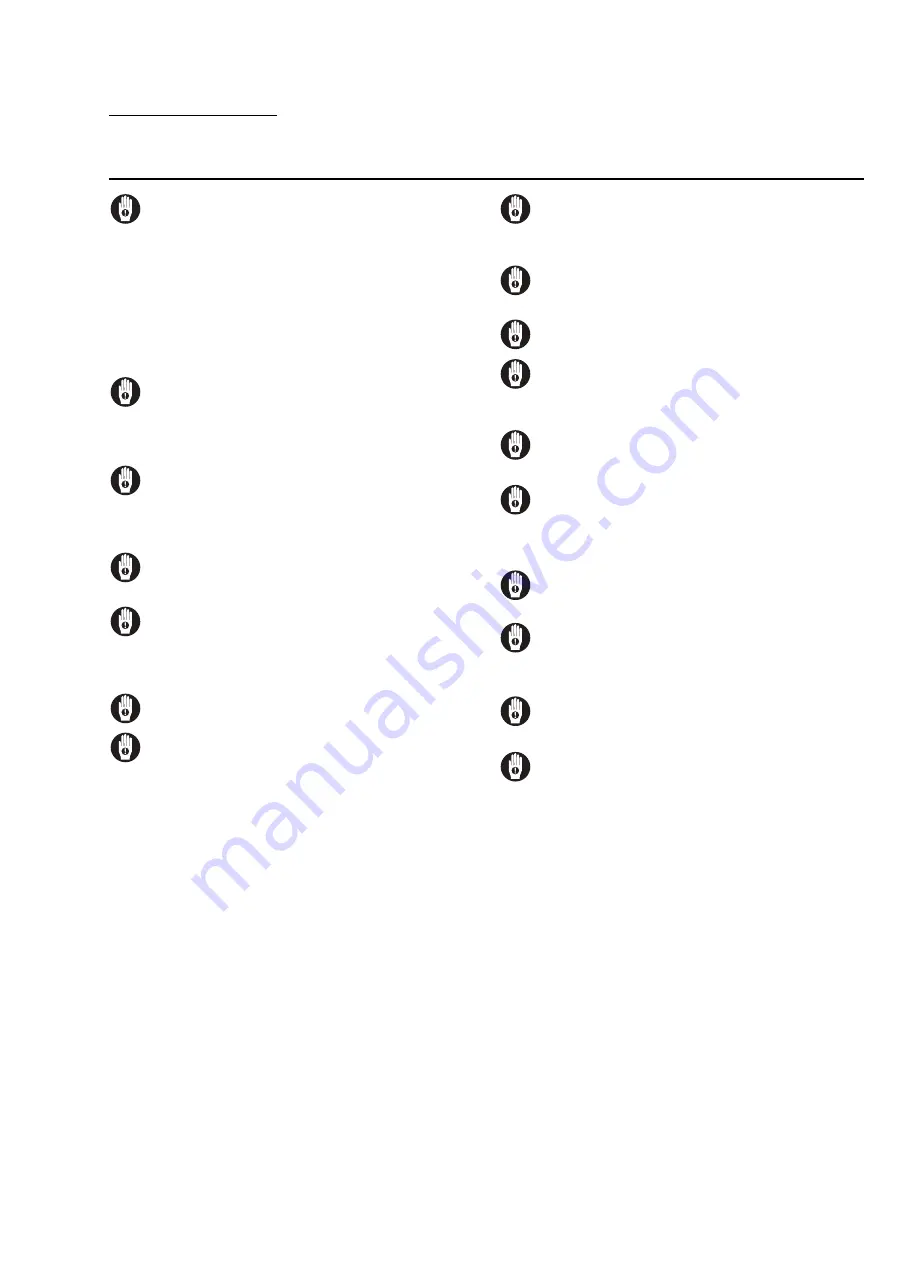
1
WILDEN PUMP & ENGINEERING, LLC
WIL-10260-E-02
SECTION 1
MODEL T4 METAL
CAUTIONS – READ FIRST!
TEMPERATURE LIMITS:
Polypropylene
0°C to 79°C
32°F to 175°F
PVDF
–12°C to 107°C
10°F to 225°F
Neoprene
–17.8°C to 93.3°C
0°F to 200°F
Buna-N
–12.2°C to 82.2°C
10°F to 180°F
EPDM
–51.1°C to 137.8°C
–60°F to 280°F
Viton
®
–40°C to 176.7°C
–40°F to 350°F
Wil-Flex™
–40°C to 107.2°C
–40°F to 225°F
Polyurethane 12.2°C to 65.6°C
10°F to 150°F
Saniflex™
–28.9°C to 104.4°C
–20°F to 220°F
PTFE
4.4°C to 104.4°C
40°F to 220°F
CAUTION:
When choosing pump materials, be sure
to check the temperature limits for all wetted compo-
nents. Example: Viton
®
has a maximum limit of 176.7°C
(350°F) but polypropylene has a maximum limit of only
79°C (175°F).
CAUTION:
Maximum temperature limits are based
upon mechanical stress only. Certain chemicals will
significantly reduce maximum safe operating tempera-
tures. Consult engineering guide for chemical compat-
ibility and temperature limits.
CAUTION:
Always wear safety glasses when operat-
ing pump. If diaphragm rupture occurs, material being
pumped may be forced out air exhaust.
WARNING:
Prevention of static sparking — If static
sparking occurs, fire or explosion could result. Pump,
valves, and containers must be properly grounded when
handling flammable fluids and whenever discharge of
static electricity is a hazard.
CAUTION:
Do not exceed 8.6 bar (125 psig) air supply
pressure.
CAUTION:
Before any maintenance or repair is
attempted, the compressed air line to the pump should
be disconnected and all air pressure allowed to bleed
from pump. Disconnect all intake, discharge and air
lines. Drain the pump by turning it upside down and
allowing any fluid to flow into a suitable container.
CAUTION:
Blow out air line for 10 to 20 seconds
before attaching to pump to make sure all pipe line
debris is clear. Use an in-line air filter. A 5µ (micron) air
filter is recommended.
NOTE:
When installing PTFE diaphragms, it is impor-
tant to tighten outer pistons simultaneously (turning in
opposite directions) to ensure tight fit.
NOTE:
Tighten clamp bands and retainers prior to instal-
lation. Fittings may loosen during transportation.
NOTE:
Before starting disassembly, mark a line from
each liquid chamber to its corresponding air chamber.
This line will assist in proper alignment during reas-
sembly.
CAUTION:
Verify the chemical compatibility of the
process and cleaning fluid to the pump’s component
materials in the Chemical Resistance Guide (see E4).
CAUTION:
When removing the end cap using
compressed air, the air valve end cap may come out
with considerable force. Hand protection such as a
padded glove or rag should be used to capture the
end cap.
CAUTION:
Only explosion proof (NEMA 7) solenoid
valves should be used in areas where explosion proof
equipment is required.
NOTE:
All non lube-free air-operated pumps must be
lubricated. Wilden suggests an arctic 5 weight oil (ISO
grade 15). Do not over-lubricate pump. Over-lubrica-
tion will reduce pump performance.
NOTE:
On cast iron pumps equipped with PTFE
diaphragms, balls and sealing rings, PTFE gasket kits
should be utilized.
NOTE:
UL-listed pumps must not exceed 3.4 bar (50
psig) air supply pressure.