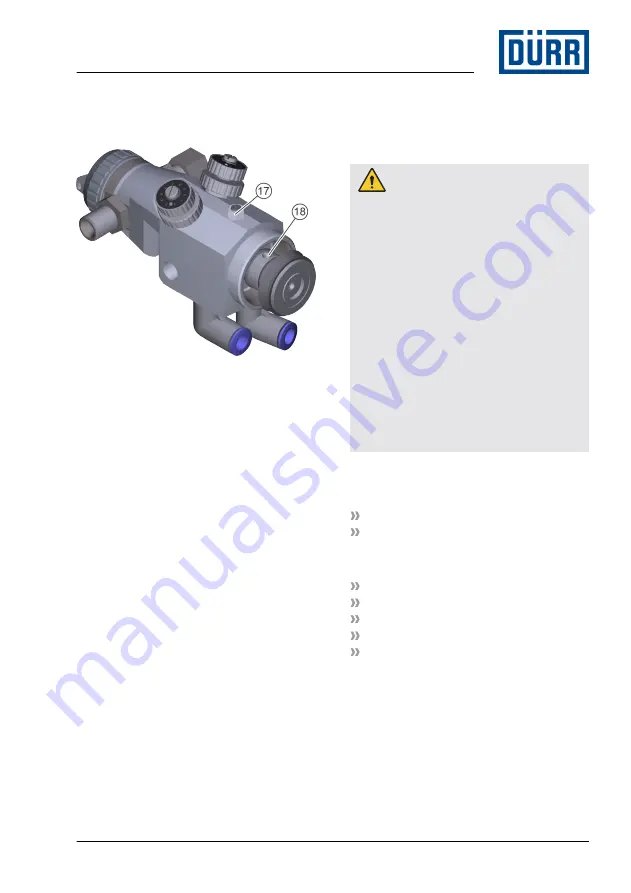
22. Lubricate piston sleeve and piston glide
surface in the housing lightly with sili-
cone-free oil.
Fig. 26: Insert piston axis
23. Ensure that the tapering bore of the
piston axis (18) is perpendicular to the
tapped hole (17) in the housing.
24. Push in complete piston axis from
behind into the housing.
25. Thread in the screw (2).
26. Screw on hex nut (1) and tighten it.
27. Lubricate needle shank lightly with sili-
cone-free oil. Push in needle (4) care-
fully into the housing from the back.
28. Insert needle spring (5) and plunger
spring (6).
29. Fit end cap (7).
30. Fit cap nut (8). Tighten by hand.
10
Disassembly and Disposal
10.1 Safety recommendations
WARNING!
Material escaping under pressure
Material leaking under high pressure can
penetrate the body. Even if the injury looks
like a harmless cut wound, the penetrating
material leads to amputation, serious inju-
ries can cause death.
– Do not try to seal leakages using body
parts, gloves or towels.
– If there are injuries, seek medical
attention immediately.
Before working on the product:
– Disconnect the system, in which the
product is installed, from compressed
air and material supply.
– Secure the system against being
switched on again.
– Depressurize the lines.
10.2 Disassembly
Personnel:
Operator
+ additional qualification explosion pro-
tection
Protective equipment:
Use ear protection
Eye protection
Respiratory protection device
Protective workwear
Protective gloves
1. Rinsing
2. Disconnect the compressed air supply
and material feed. Secure against recon-
nection.
Disassembly and Disposal
02/2020
EcoGun AA AUTO - MSG00008EN
27/48