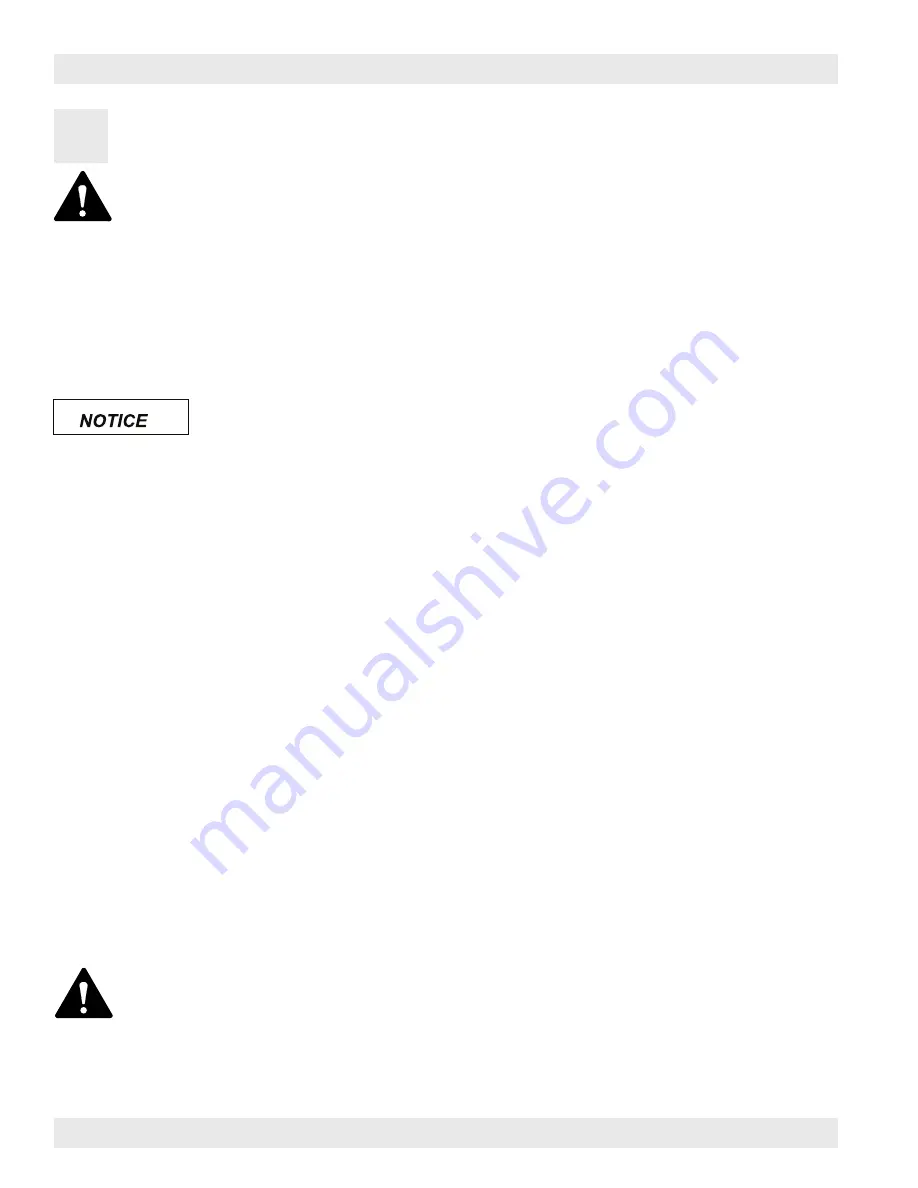
5
Donaldson Company, Inc.
4
Product Service
Operational Checklist
1. Monitor the physical condition of the collector and repair or replace any damaged components.
Routine inspections will minimize downtime and maintain optimum system performance. This is particularly important on
continuous-duty applications.
2. Periodically check the compressed air components and replace compressed air filters.
Drain moisture following the manufacturer’s instructions. With the compressed air supply ON, check the cleaning valves,
solenoid valves, and tubing for leaks. Replace as necessary.
3. Monitor pressure drop across filters.
Abnormal changes in pressure drop may indicate a change in operating conditions and possibly a fault to be corrected. For
example, prolonged lack of compressed air will cause an excess build-up of dust on the filters resulting in increased pressure
drop. Cleaning off-line with no airflow usually restores the filters to normal pressure drop.
4. Monitor exhaust.
5. Monitor dust disposal. Empty the dust drawers at the end of each shift, or more frequently if necessary. Dust drawers should
be emptied when they are more than 2/3 full.
6. Check fan wheel set screws. Set screws should be checked and retightened to 10.5 foot pounds for 3/8-in stainless steel
set screws and 25 foot pounds for 1/2-in stainless steel set screws after eight hours of operation and again after 80 hours of
operation.
Set screws on fan wheels must be properly tightened to avoid severe personal injury and/or property damage.
During any service activities there is some potential for exposure to the dust in the collector. Most dusts present
safety and health hazards that require precautions. Wear eye, respiratory, head and other protection equipment
suitable for the type of dust when performing any service activities.
Use appropriate access equipment and procedures. Note the standard collector is not equipped with access
platforms unless noted on the specification drawings.
LOCK-OUT all energy sources prior to performing any service or maintenance on the equipment.
Electrical service or maintenance work must be performed by a qualified electrician and comply with all applicable
national and local codes.
Turn compressed air supply OFF, bleed and lock out lines before performing service or maintenance work.
Do not set compressed-air pressure above 70-psig as component damage can occur.
All compressed air components must be sized to meet the system requirements of 50-70-psig supply
pressure.
The compressed-air supply must be oil and moisture free. Contamination in the compressed air used to clean filters
will result in poor cleaning, cleaning valve failure, or poor collector performance.
Purge compressed air lines to remove debris before connecting to the collector’s compressed air manifold.