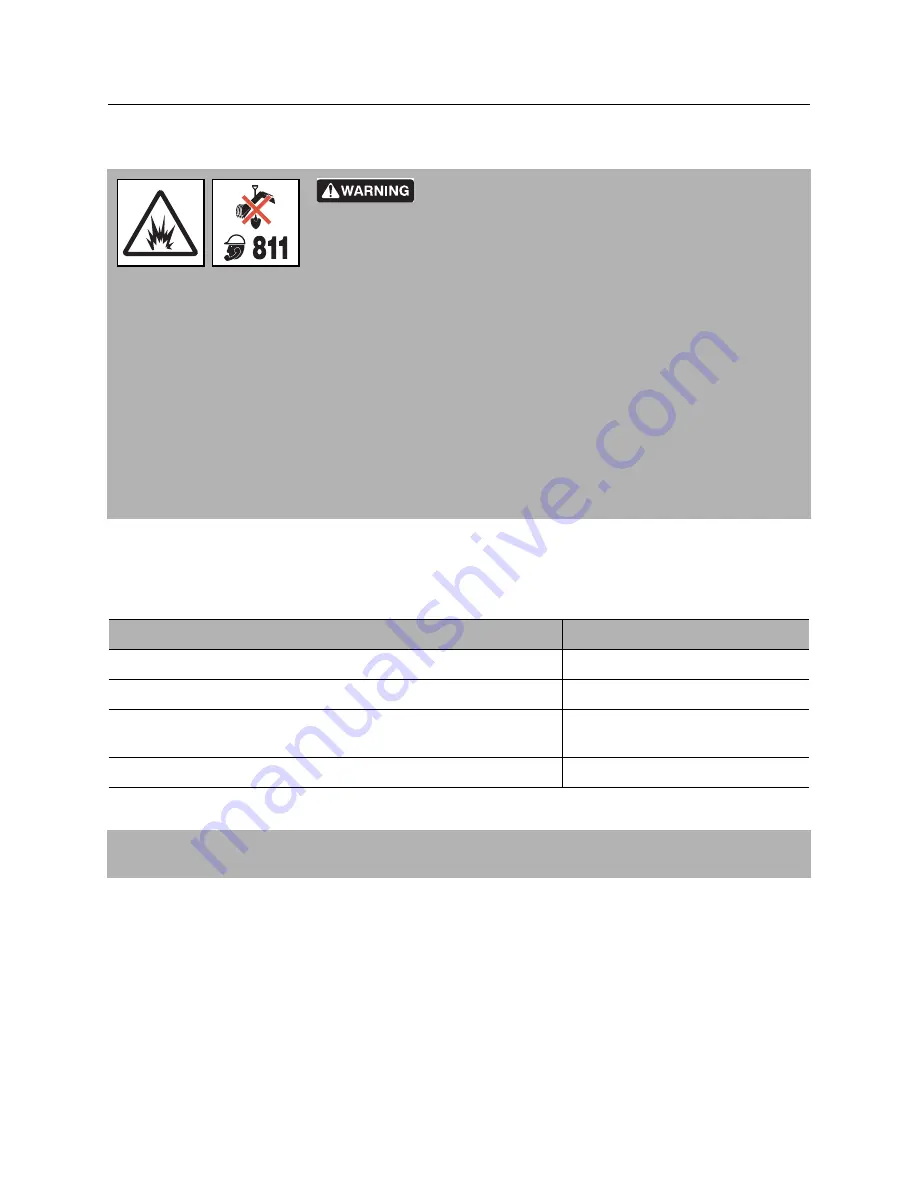
Prepare - 34
SK752 Operator’s Manual
Classify Jobsite
Classify Jobsite
Select a Classification
Jobsites are classified according to underground hazards present.
Jobsite hazards could cause death or serious injury. Use
correct equipment and work methods. Use and maintain proper safety
equipment.
To help avoid injury:
•
Wear personal protective equipment including hard hat, safety eye wear, and hearing protection.
•
Do not wear jewelry or loose clothing.
•
Comply with all utility notification regulations before digging or drilling.
•
Mark proposed path with white paint and have underground utilities located before working.
•
Verify location of previously marked underground hazards.
•
Mark jobsite clearly and keep spectators away.
Remember, jobsite is classified by hazards in place -- not by line being installed.
If working . . .
then classify jobsite as . . .
within 10’ (3 m) of a buried electric line
electric
within 10’ (3 m) of a natural gas line
natural gas
in sand or granite which is capable of producing crystalline silica
(quartz) dust
crystalline silica (quartz) dust
within 10’ (3 m) of any other hazard
other
NOTICE:
If you have any doubt about jobsite classification, or if jobsite might contain unmarked
hazards, take steps outlined previously to identify hazards and classify jobsite before working.
Summary of Contents for SK752
Page 1: ...SK752 Operator s Manual 053 2859 Issue 2 0 Original Instruction...
Page 11: ...Contents 10 SK752 Operator s Manual...
Page 21: ...Safety 20 SK752 Operator s Manual Machine Safety Alerts...
Page 31: ...Controls 30 SK752 Operator s Manual Attachment Plate...
Page 41: ...Prepare 40 SK752 Operator s Manual Connect Attachment...
Page 47: ...Drive 46 SK752 Operator s Manual Shut Down...
Page 55: ...Transport 54 SK752 Operator s Manual Retrieve...
Page 86: ......
Page 87: ......
Page 88: ...SK752 Operator s Manual Service Record 87 Service Record Service Performed Date Hours...
Page 89: ...Service Record 88 SK752 Operator s Manual Service Performed Date Hours...