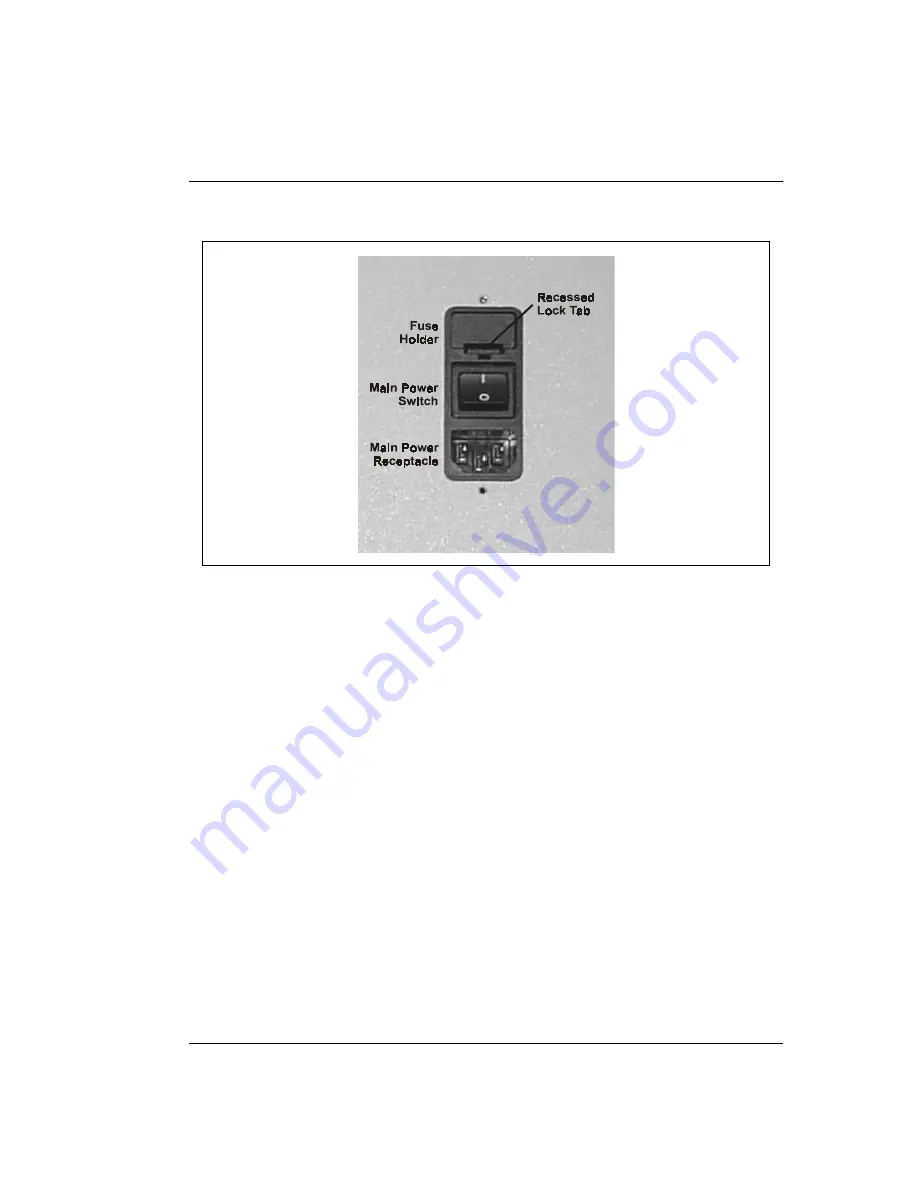
5 • Service
Doc. 031842-01 5/02
5-35
3. Replace the two fuses in the holder with new IEC127 fast-blow fuses rated
8 amps (P/N 954766).
NOTE Dionex recommends always replacing both fuses.
4. Reinsert the fuse holder into its compartment. Apply enough pressure evenly
against the holder to engage the tab on the recessed lock; when the tab is
engaged, the holder is flush against the panel.
5. Reconnect the main power cord. Turn on the ASE 100 main power switch.
Figure 5-18. Main Power Fuse Holder
Summary of Contents for ASE 100
Page 8: ...ASE 100 Accelerated Solvent Extractor vi Doc 031842 01 5 02...
Page 24: ...ASE 100 Operator s Manual 2 10 Doc 031842 01 5 02 Figure 2 4 ASE 100 Rear Panel...
Page 32: ...ASE 100 Operator s Manual 2 18 Doc 031842 01 5 02...
Page 42: ...ASE 100 Operator s Manual 3 10 Doc 031842 01 5 02 Figure 3 2 Inspecting Cell O Rings...
Page 60: ...ASE 100 Operator s Manual 3 28 Doc 031842 01 5 02...
Page 69: ...4 Troubleshooting Doc 031842 01 5 02 4 9 Figure 4 1 ASE 100 Plumbing Diagram...
Page 106: ...ASE 100 Operator s Manual 5 36 Doc 031842 01 5 02...
Page 110: ...ASE 100 Operator s Manual A 4 Doc 031842 01 5 02...
Page 113: ...B Installation Doc 031842 01 5 02 B 3 Figure B 1 ASE 100 Rear Panel...
Page 150: ...ASE 100 Accelerated Solvent Extractor Index 8 Doc 031842 01 5 02...