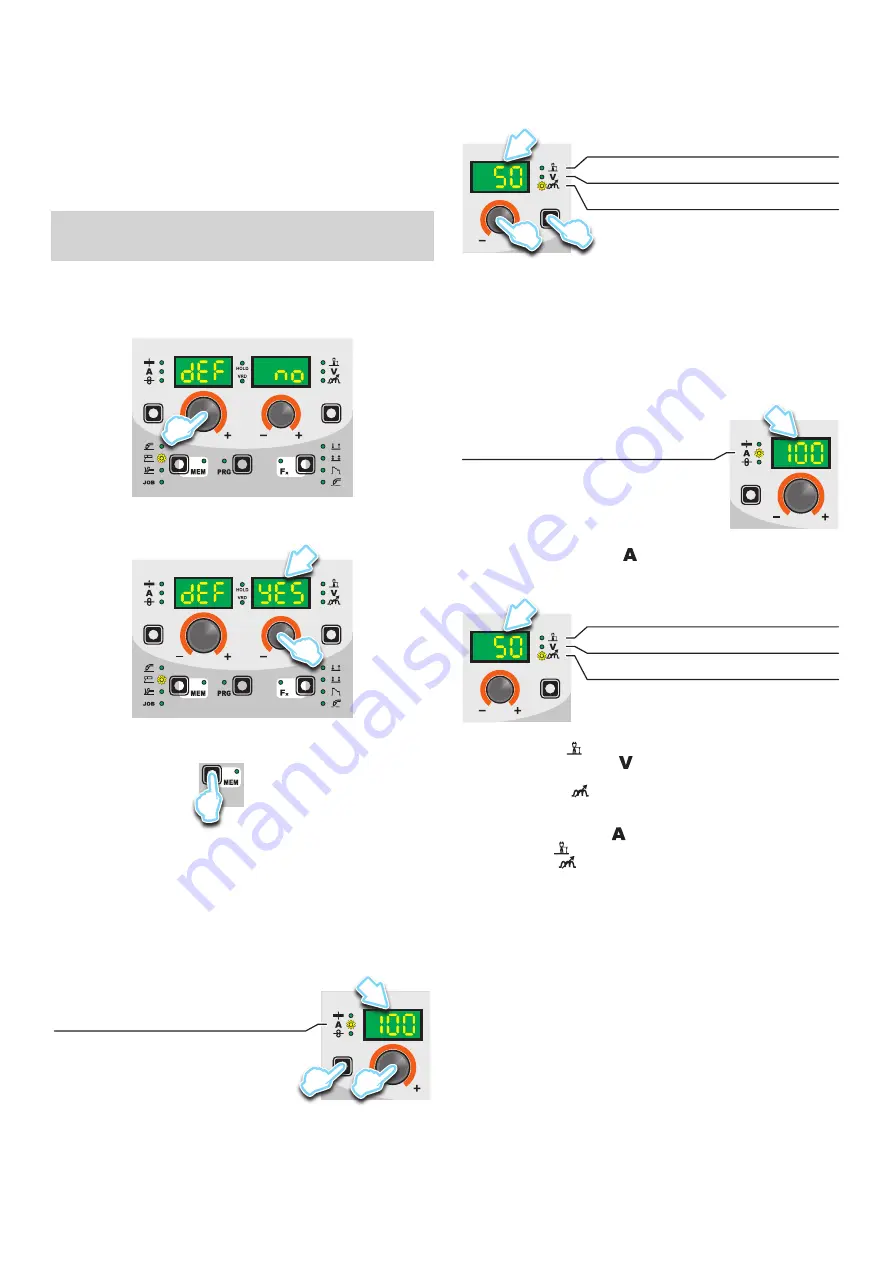
30
The SPECIAL FUNCTIONS “Fx” that are only available in the MMA
welding process are shown below. For all the other explanations
regarding this menu make reference to the relative paragraph.
•
HOT START (Hot) -
At the start of the welding process it increas-
es the current, adjustable in percentage, reducing in such a way
the risk of low function at the start of the connection.
•
ARC FORCE (ArC) -
During the welding process, it increases
the current in percentage, reducing in such a way the risk of fus-
ing the electrode to the piece.
■
PROGRAM DEFAULT (dEF)
WARNING: If carried out, this operation resets the program
in use to the factory default settings.
To carry out the reset of the settings / parameters, proceed in the
following manner:
•
Rotate the ENCODER - A (E1) knob until both the displays read
dEF no
(see figure).
E1
•
Rotate the ENCODER - V knob (E2) until the PARAMETERS
DISPLAY - V screen (D2) reads
YES
.
D2
E2
•
Hold the SAVE “MEM” key (T2) down for at least
2
consecu-
tive seconds.
T2
T ≥ 2 s
•
The program in use has now been completed successfully. To
confirmation the above, the control panel of the welder performs
a short operation of MACHINE CHECK (all of the LED stay lit
simultaneously so as to verify their actual operation), the gen-
erator itself starts, having memorised the new settings and is
again ready to weld.
4 - PRE-SETTING
Before welding it is possible to set the following parameters:
D1
T1
E1
WELDING CURRENT
Example: WELDING CURRENT
Press the PARAMETER SELECTION - A key (T1) until the LED
that corresponds to the WELDING CURRENT switches on. Turn
the ENCODER - A knob (E1) to change the value shown on the
PARAMETER DISPLAY - A screen (D1).
D2
T4
E2
ARC FORCE
WELDING VOLTAGE
HOT START
Example: ARC FORCE
Press the PARAMETER SELECTION - V key (T4) until the LED
that corresponds to the ARC FORCE switches on. Turn the EN-
CODER - V knob (E2) to change the value shown on the PARAM-
ETER DISPLAY - V screen (D2).
5 - WELDING
During the welding the display shows:
•
PARAMETER DISPLAY screen - A (D1)
D1
WELDING CURRENT
- WELDING CURRENT (
):the measured value of the current
of what is being welded.
•
PARAMETER DISPLAY screen - V (D2)
D2
ARC FORCE
WELDING VOLTAGE
HOT START
- HOT START (
): the value previously set.
- WELDING VOLTAGE (
): the measured value of the voltage
of what is being welded.
- ARC FORCE (
): the value previously set.
During the welding the operator can change the following param-
eters:
•
WELDING CURRENT (
).
•
HOT START (
).
•
ARC FORCE (
).
•
SPECIAL FUNCTIONS “Fx” - FIRST LEVEL MENU.
6 - HOLD
This function automatically starts itself at the conclusion of eve-
ry welding operation welding and it is indicated to the operator by
means of a flashing light of the HOLD FUNCTION LED for a spe-
cific amount of time. Once the welding has been terminated, for
about
15
seconds, both the DISPLAYS should show the same val-
ues of the parameters during the welding.
In this phase the displays show:
•
PARAMETER DISPLAY screen - A (D1)