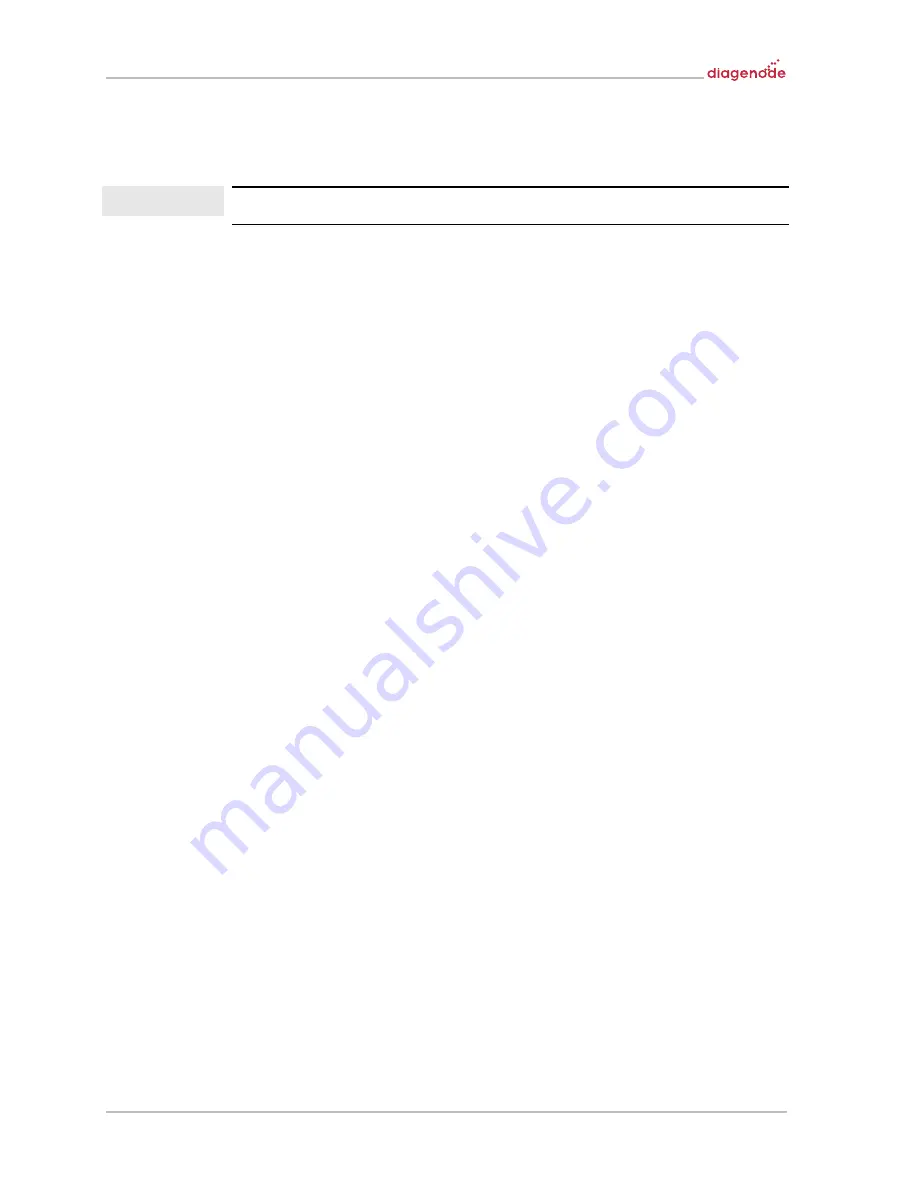
Function description
Chapter 3
OPERATION MANUAL
V1.1.0en/13.12.12
Errors and omissions excepted.
Water Cooler
31
3.3
Testing planning
Also observe page 12 in section
«.
The focus is on your application. Remember that system performance depends on the temperature
and viscosity of the thermal fluid and the flow speed:
Make sure that the electrical connection is adequately dimensioned.
The installation location of the temperature control unit should be selected so as to ensure
adequate fresh air, even with water-cooled chillers.
The selected hose connections must withstand the thermal fluid/working temperatures.
You must choose a thermal fluid that not only permits the minimum and maximum working
temperatures, but that is also suitable for the combustion point and/or viscosity. Furthermore,
the thermal fluid must be compatible with all materials in your system.
The hose lengths (as short as possible), the hose diameters (clearance of the pump connections is
the reference value), and the viscosity of the thermal fluid (this is temperature-dependent)
determine the pressure drop and influence the tempering result. Inadequate clearances for
connections, corrugated hoses and values can cause considerable flow resistances. As a result, it
takes longer to control the temperature in your application.
Unsuitable thermal fluids can negatively impact temperature control, causing negative
temperature control results and damage. Always use only the thermal fluids recommended by the
manufacturer and only within the usable temperature and pressure range. With a temperature
control near to the boiling point of the thermal fluid, the application should be at around the
same height level or above the temperature control unit. During filling, the thermal fluid must be
around room temperature level. Fill slowly, carefully and evenly. At the same time, make sure
that no thermal fluid overflows (backup). Personal protective equipment, including safety
goggles, temperature and chemical-resistant protective gloves, must be worn.
After filling and setting all the requisite parameters, the temperature control circuit must be
vented. This is required to ensure trouble-free operation of the temperature control unit and
hence your application.
With pressure-sensitive applications such as glass reactors, the maximum flow pressure of the
temperature control unit for cross-section reduction or sealing must be observed (see data sheet
from page 55 in section
and the data sheet for your glass apparatus). Take the necessary
precautions (e.g. pressure limiter for temperature control units with pressure regulation and/or
use of an external bypass for temperature control units without pressure limiter).
Avoid bending the hoses.
Check hoses for potential material fatigue at regular intervals (e.g. cracks).
For water-cooled temperature control units, please see page 55 in section
for the maxi-
mum cooling water temperature and the differential pressure required to ensure trouble-free op-
eration.
INFORMATION
.
Summary of Contents for BioAcc-cool
Page 1: ...Cat No BioAcc cool Water Cooler Version 1 1 ...
Page 6: ...OPERATION MANUAL Water Cooler Errors and omissions excepted V1 1 0en 13 12 12 6 ...
Page 10: ...OPERATION MANUAL Water Cooler Errors and omissions excepted V1 1 0en 13 12 12 10 ...
Page 58: ......
Page 59: ...PAGE 55 www diagenode com ...
Page 60: ...orders diagenode com orders na diagenode com www diagenode com ...