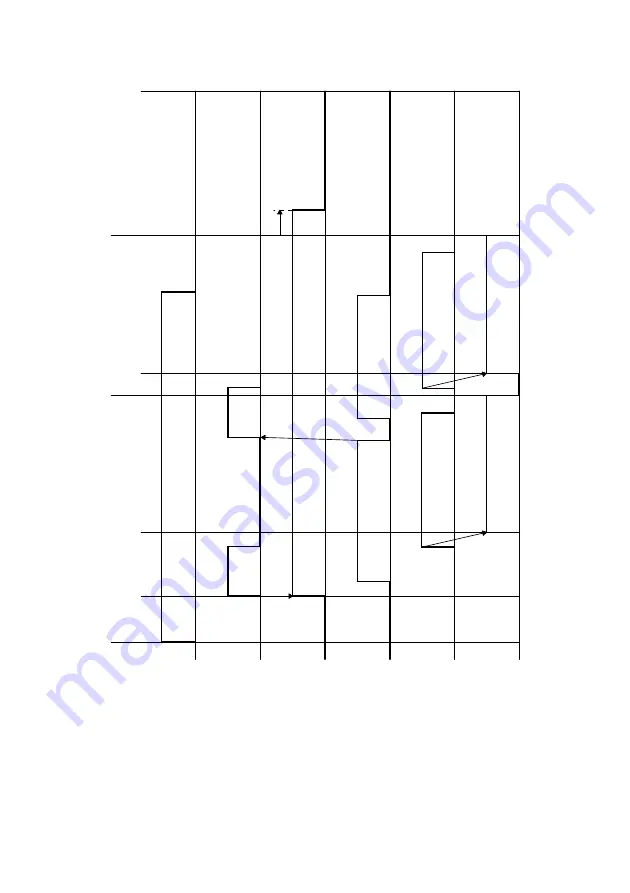
T-8
3.
TIMING CHART
Or
iginal load
ed
St
a
rt
k
e
y
presse
d
Begin scanning
of first page
Begin sca
nning
of
second pag
e
Finish scanning
of first page
F
inish
scanning of
seco
nd page
F
eeding tw
o A4 L
pages
H
L
OF
F
ON
Stop
L
H
OF
F
ON
Or
ig
inal Detection
Sensor
PC1
P
a
per T
a
k
e
-Up
Clutch
CL1
ADF Ma
in Moto
r
M5
Leading Edge
Detection Sensor
PC3
Or
ig
inal scann
ing
F
orw
ard
ro
tatio
n
Summary of Contents for D 16G
Page 1: ...DEVELOP SERVICE MANUAL OPTIONS D 16G 4986 7991 00 ...
Page 2: ......
Page 4: ......
Page 10: ......
Page 11: ...GENERAL ...
Page 12: ......
Page 20: ......
Page 21: ...MECHANICAL ELECTRICAL ...
Page 22: ......
Page 54: ......
Page 55: ...MAINTENANCE ...
Page 56: ......
Page 66: ......
Page 67: ...DIS REASSEMBLY ADJUSTMENT ...
Page 68: ......
Page 116: ......
Page 117: ...CONTROL PANEL SERVICE MODE DESCRIPTIONS ...
Page 118: ......
Page 122: ...S 4 2 3 PWB IF Interface Board 4980S004AA USB port IEEE1284 parallel port ...
Page 142: ......
Page 143: ...TROUBLESHOOTING ...
Page 144: ......
Page 184: ...DEVELOP Copyright 2003 Develop Printed in Germany ...
Page 185: ...AF 11 Service Manual ...
Page 188: ...GENERAL ...
Page 190: ...MECHANICAL ELECTRICAL ...
Page 199: ...DIS REASSEMBLY ADJUSTMENT ...
Page 215: ...TROUBLESHOOTING ...
Page 224: ...PF 125 Service Manual ...
Page 226: ...GENERAL ...
Page 228: ...MECHANICAL ELECTRICAL ...
Page 233: ...DIS REASSEMBLY ADJUSTMENT ...