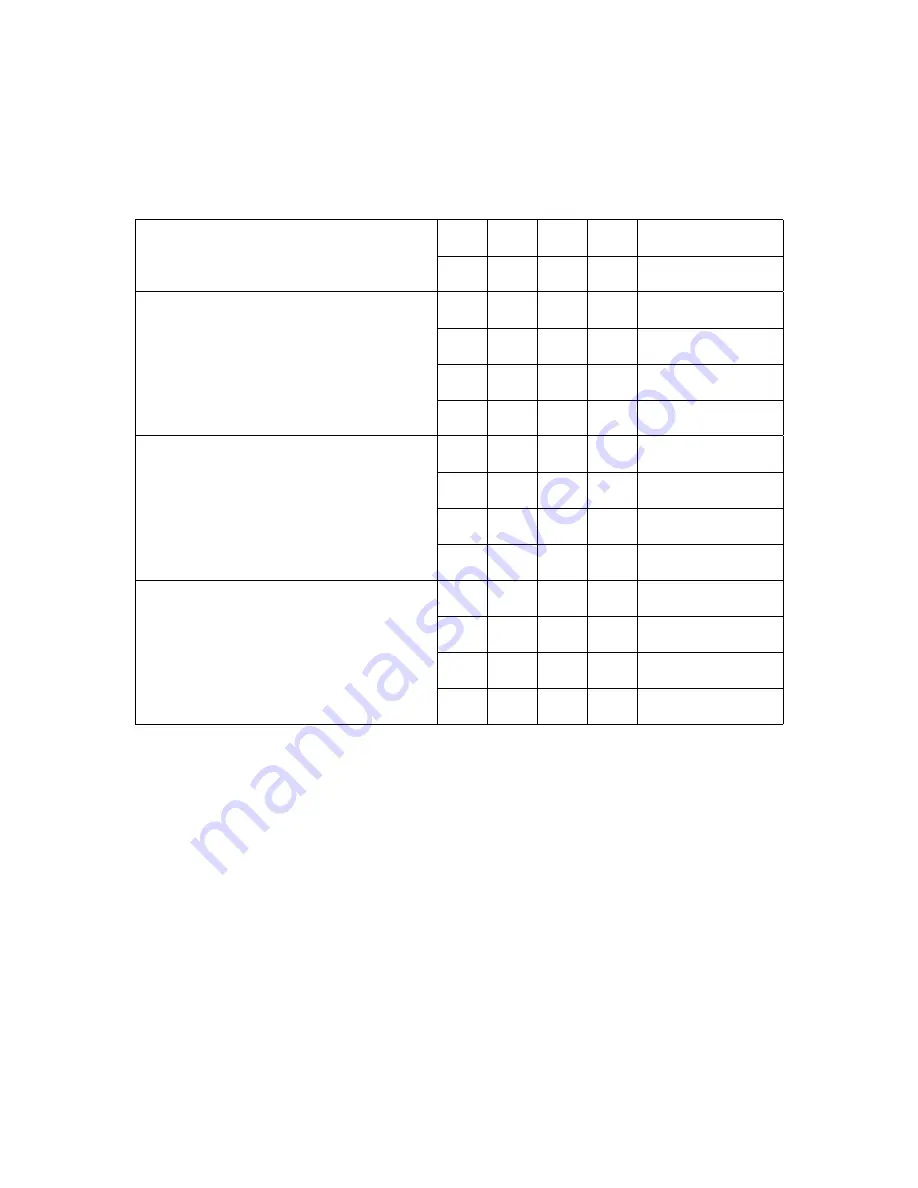
13
INFORMATIONS AND SPECIFICATIONS
Table 9 – Air Flow Adjustement - S1
FACTORY DEFAULT
S1-1
S1-2
S1-3
S1-4
DESCRIPTION
OFF
OFF
OFF
OFF
NO ADJUSTMENT
LOW HEAT ADJUSTMENT ONLY (40%)
OFF
ON
OFF
OFF
-7.5%
OFF
ON
OFF
ON
-15%
OFF
ON
ON
OFF
+7.5%
OFF
ON
ON
ON
+15%
HIGH HEAT ADJUSTMENT ONLY (100%)
ON
OFF
OFF
OFF
-7.5%
ON
OFF
OFF
ON
-15%
ON
OFF
ON
OFF
+7.5%
ON
OFF
ON
ON
+15%
ADJUSTMENT TO ALL RISE RATE
ON
ON
OFF
OFF
-7.5%
ON
ON
OFF
ON
-15%
ON
ON
ON
OFF
+7.5%
ON
ON
ON
ON
+15%
48
Summary of Contents for Chinook C105-M-V
Page 24: ...Figure 10 Typical gas pipe arrangement 23...
Page 27: ...Figure 11 Wiring Diagram 26...
Page 39: ...Figure 14 Wiring Diagram Modulating t stat 38...
Page 53: ...Table 17 CFM 52...
Page 54: ...Figure 15 Dimensional Drawing 53...
Page 55: ...14 PART LIST 54...
Page 56: ...Figure 16 Exploded view 1 55...
Page 57: ...Figure 17 Exploded view 2 56...
Page 59: ...Table 19 Parts list continued 58...
Page 60: ...Table 20 Parts list MS 59...