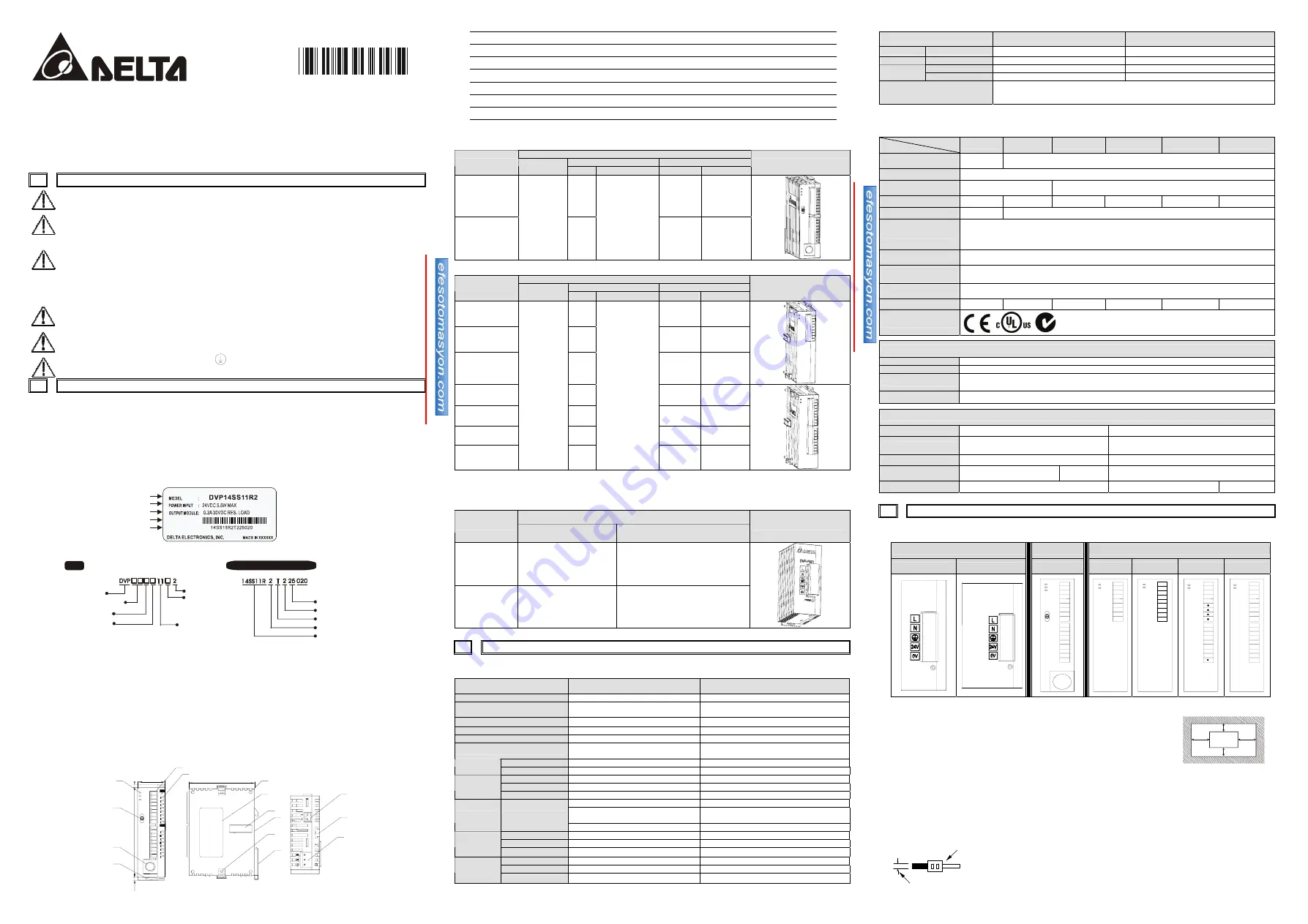
http://www.delta.com.tw/industrialautomation/
5011608703-ZSE4
2006-05-05
DVP-SS
Programmable Logic
Controller
Instruction Sheet
1
WARNING
Please carefully read this manual thoroughly prior to use the DVP PLC.
The AC input power must be disconnected before any maintenance.
This is an OPEN-TYPE built-in PLC, and the PLC is certified to meet the safety requirements of IEC 61131-2
(UL 508) when installed in the enclosure to avoid high temperature, high humidity, exceessive vibration,
corrosive gases, liquids, airbome dust or metallic particles. Also, it is equipped with protective methods such
as some special tool or key to open the enclosure, to avoid the possible hazard to users or any damage to
the PLC.
Do not connect the AC power to any of the input/output terminals, as it might cause damage to the PLC.
Make sure that all the wiring is well conducted prior to power on. Do NOT touch terminals when power on.
Do not touch the internal circuit for at least 1 minute after the power supply is OFF.
Make sure that the PLC is properly grounded
, to avoid any electromagnetic noise.
2
INTRODUCTION
2.1 Model Explanation and Peripherals
Thank you for choosing DELTA’s DVP PLC Series. The DVP-SS series provides a 14-point Main Processing Unit
and allows to expand units with 8~16 points. The maximum input/output points could be extended up to 128 points.
Since the power supply unit is independent of the main unit, and with the volume of the device being smaller, the
installation of DVP PLC is thus easier.
Nameplate Explanation
V4.9
PLC Model
Input Power Supply Specification
Output Module Specification
Bar Code and Serial Number
Software Version
CE
Model Explanation
Model
Serial Number Explanation
Product Series
Input+Output point
Model type
S: Standard Function MPU
M: Input Point Expansion Unit
N: Output Point Expansion Unit
P: I/O Point Expansion Unit
R
: Relay
T: Transistor
N: No Output Module
Production Week
Production Place (Taoyuan)
Production Year (2002)
Version
Production Model
S TYPE
DC Power Input
Version
Periphery Equipment
◎
DVPHPP Handheld Programming Panel
◎
WPLSoft (WINDOWS) Ladder Diagram Editor
◎
DVPACAB115 Cable (HPP PLC, 1.5m)
◎
DVPACAB215 Cable (PC PLC, 1.5m)
◎
DVPACAB230 Cable
(
PC PLC/3
公尺)
, DVPACAB2A30 Cable
(
PC PLC/3
公尺)
◎
DVPACAB315 Cable (HPP PC, 1.5m)
2.2 Product Profile and Outline
90.00
4.00
3.00
25.20
60.00
1
2
3
4
5
6
7
8
9
3
10
11
12
13
STOP
RUN
ERROR
RUN
POWER
X6
X7
C0
Y5
Y4
Y3
Y2
Y1
Y0
C2
C1
X5
X4
X3
X2
X1
X0
s
s
14
1. Status indicator (Power, RUN and ERROR)
8. Extension port
2. I/O port for program communication (RS-232)
9. Extension unit clip
3. DIN rail clip
10. DIN rail (35mm)
4. I/O terminals
11. RS-485 Communication port
5. I/O point indicator
12. Mounting rail of the extension unit
6. Mounting hole of the extension unit
13. DC Power input
7. Nameplate
14. RUN/STOP switch
2.3 Model Numbers
◎
Standard Function MPU
Input/Output
Input Unit
Output Unit
Model
Power
Point
Type
Point
Type
Profile Reference
DVP14SS11R2 8
6
Relay
DVP14SS11T2
24VDC
8
DC Type
Sink or Source
6 Transistor
◎
Digital I/O Extension Unit
Input/Output
Input Unit
Output Unit
Model
Power
Point
Type
Point
Type
Profile Reference
DVP08SM11N 8
0
None
DVP08SN11R 0
8
Relay
DVP08SN11T 0
8
Transistor
DVP08SP11R 4
4
Relay
DVP08SP11T 4
4
Transistor
DVP16SP11R 8
8
Relay
DVP16SP11T
24VDC
8
DC Type
Sink or Source
8 Transistor
◎
Analog/temperature module extension unit
Please refer to user manuals that go with PLC.
◎
Power Supply Module
Input/Output
Model
Input Power
Output Power
Profile Reference
DVPPS01
100~240VAC
( 50/60Hz )
Output voltage: 24VDC
Output current (max.): 1A
DVPPS02
100~240VAC
( 50/60Hz )
Output voltage: 24VDC
Output current (max.): 2A
3
STANDARD SPECIFICATIONS
3.1 Function Specifications
Item
Specification
Remark
Control Method
Stored program, cyclic scan system
I/O Processing Method
Batch I/O (refresh)
Immediate refresh command available only
with I/O of the MPU
Execution Speed
Basic command (several
μ
s)
Application command (10~hundreds
μ
s)
Program Language
Instru Ladder D SFC
Step instructions included
Program Capacity
3792 Steps
Built-in EEPROM
Instructions
Basic commands: 32 (including the STL
commands)
Application commands: 107
Primary step point
10 Points
S0~S9
Step Relay
(Latched)
General step point
118 Points
S10~S127
General
512+232 Points
M000~M511 + M768~M999
Latched
256 Points
M512~M767
Auxiliary
Relay
Special
280 Points
M1000~M1279
64 Points
T0~T63 (100 ms time base)
63 Points
T64~T126 (10 ms time base, when M1028 is
On)
Timer
Digital
1 Point
T127 (1 ms time base)
General
112 Points
C0~C111
Latched
16 Points
C112~C127
Counter
High-Speed
13 Points 1-Phase 20KHz, 2-Phase 5KHz
C235~C254 (all of which are latched type)
General
408 Points
D0 ~ D407
Latched
192 Points
D408~D599
Data
Register
Special
144 Points
D1000~D1143
Item
Specification
Remark
Pointer
P
64 Points
P0~P63
Index Relay E/F
2
E (=D1028), F (=D1029)
Decimal K
16 bit: -32768~+32767
32 bit: -21472147483647
Constant
Hexadecimal H
16 bit: 0000~FFFF
32 bit: 00000000~FFFFFFFF
Serial Communication Port
Program write/read communication port: RS-232C. General function communication port:
RS-485 (controlled by the RS command). The DELTA’s inverter-specific drive commands are
included as well.
*
Additional remark: Refer to the PLC Technique Application Manual for relevant special relays and data registers.
3.2 General Specifications
Model
Item
DVPPS01
DVP14SS
11R2/T2
DVP08SM11N
DVP08SN11R/T
DVP08SP11R/T
DVP16SP11R/T
Power Supply Voltage
100~240VA
C (50/60Hz)
24VDC (-15%~20%) (the counter-connection protection towards the DC input power
polarity is included)
Motion Specifications
Within 5ms of the momentary power loss, the device will keep on operating
Capacity of the Power
Supply Fuse
2A / 250VAC
---
Power Consumption
--- 3.5W 1W 1.5W 1.5W
2W
Insulation Resistance
---
Above 5 M
Ω
(500VDC between the ground and all the I/O points)
Noise Immunity
ESD(IEC 61131-2, IEC 61000-4-2): 8KV Air Discharge
EFT(IEC 61131-2, IEC 61000-4-4): Power Line: 2KV, Digital I/O: 1KV, Analog & Communication I/O: 1KV
Damped-Oscillatory Wave: Power Line: 1KV, Digital I/O: 1KV
RS(IEC 61131-2, IEC 61000-4-3): 26MHz~1GHz, 10V/m
Grounding
The diameter of the grounding wire cannot be smaller than that of terminals L and N (if numerous PLCs
are used at the same time, make sure that each PLC is grounded respectively to the ground poles)
Ambient
Temperature/Humidity
For operation: 0
℃
~55
℃
(temperature), 50~95% (humidity), the 2
nd
degree pollution.
Storage: -40
℃
~70
℃
(temperature), 5~95% (humidity)
Vibration/Shock
Immunity
International Standard Regulations: IEC1131-2, IEC 68-2-6 (TEST Fc) / IEC1131-2 & IEC 68-2-27 (TEST
Ea)
Weight (approximation)
210(g) 214(g)/208(g) 128(g)
154(g)/146(g) 141(g)/136(g) 162(g)/154(g)
Approvals
Input Point Electric Specifications
Input Type
DC (SINK or SOURCE)
Input Current
24VDC 5mA
Motion Level
Off
→
On, above 16VDC
On
→
Off, below 14.4VDC
Responding Time
About 10ms (An adjustment range of 0~20ms could be selected through D1020 and D1021)
Output Point Electric Specifications
Output Type
Relay-R Transistor-T
Current Specifications
1.5A/1 point (5A/COM)
55
℃
0.1A/1point, 50
℃
0.15A/1point
45
℃
0.2A/1 point, 40
℃
0.3A/1 point (2A/COM
)
Voltage Specifications
Below 250VAC, 30VDC
30VDC
Maximum Loading
75 VA (Inductive)
90 W
(Resistive)
9W
Responding Time
About 10 ms
Off
→
On 15us
On
→
Off 25us
4
INSTALLATION & WIRING
4.1 Terminal Wiring of the Standard Function MPU and the Digital I/O Extension Unit
Power Module
MPU
Digital I/O Extension Unit
DVPPS01
DVPPS02
DVP14SS
DVP08SM
DVP08SN
DVP08SP
DVP16SP
DVP-PS01
POWER
DVP-PS02
POWER
S / S
X 0
X 1
X 2
X 3
X 4
X 5
X 6
X 7
C 0
Y 0
C 1
C 2
Y 1
Y 2
Y 3
Y 4
Y 5
STOP
RUN
S / S
X 0
X 1
X 2
X 3
X 4
X 5
X 6
X 7
C 0
Y 0
Y 1
Y 3
Y 2
Y 4
Y 5
Y 6
Y 7
S / S
X 0
X 1
X 2
X 3
C 0
Y 0
C 1
C 2
Y 1
Y 2
C 3
Y 3
S / S
X 0
X 1
X 2
X 3
X 4
X 5
X 6
X 7
C 0
Y 0
Y 1
Y 3
Y 2
Y 4
Y 5
Y 6
Y 7
4.2 Mounting Arrangements and Wiring Notes
When installing the DVP series PLC, make sure that it is installed in an
enclosure with sufficient space (as shown diagram on the right) to its
surroundings for heat dissipation purpose.
DVP MPU
50mm
or more
50mm
or more
50mm
or more
50mm
or more
Installation of the DIN Rail
The DVP-PLC can be secured to a cabinet by using the DIN rail. This DIN rail should be 35mm high with
a depth of 7.5mm, and when mounting the PLC on the DIN rail, be sure to use the end bracket to stop any
side-to-side motion of the PLC, which will reduce the chance of the wires being pulled loose. At the bottom
of the PLC is a small retaining clip. To secure the PLC to the DIN rail, place it onto the rail and gently
push up the clip. To remove it, pull down the retaining clip and gently pull the PLC away from the DIN rail.
Wiring
22-16AWG
< 1.5mm
Use the 22-16AWG (1.5mm) single-core bare wire or the multi-core wire for the
I/O wiring, and the specifications of the terminal are shown diagram on the left.
The twisting power of the screw for the PLC terminal is 1.95 kgf-cm (1.7 lb-in).
Be sure not to place power wires such as the input point signal wire and the
output point wire at the same conduit or to use the same multi-core wire.