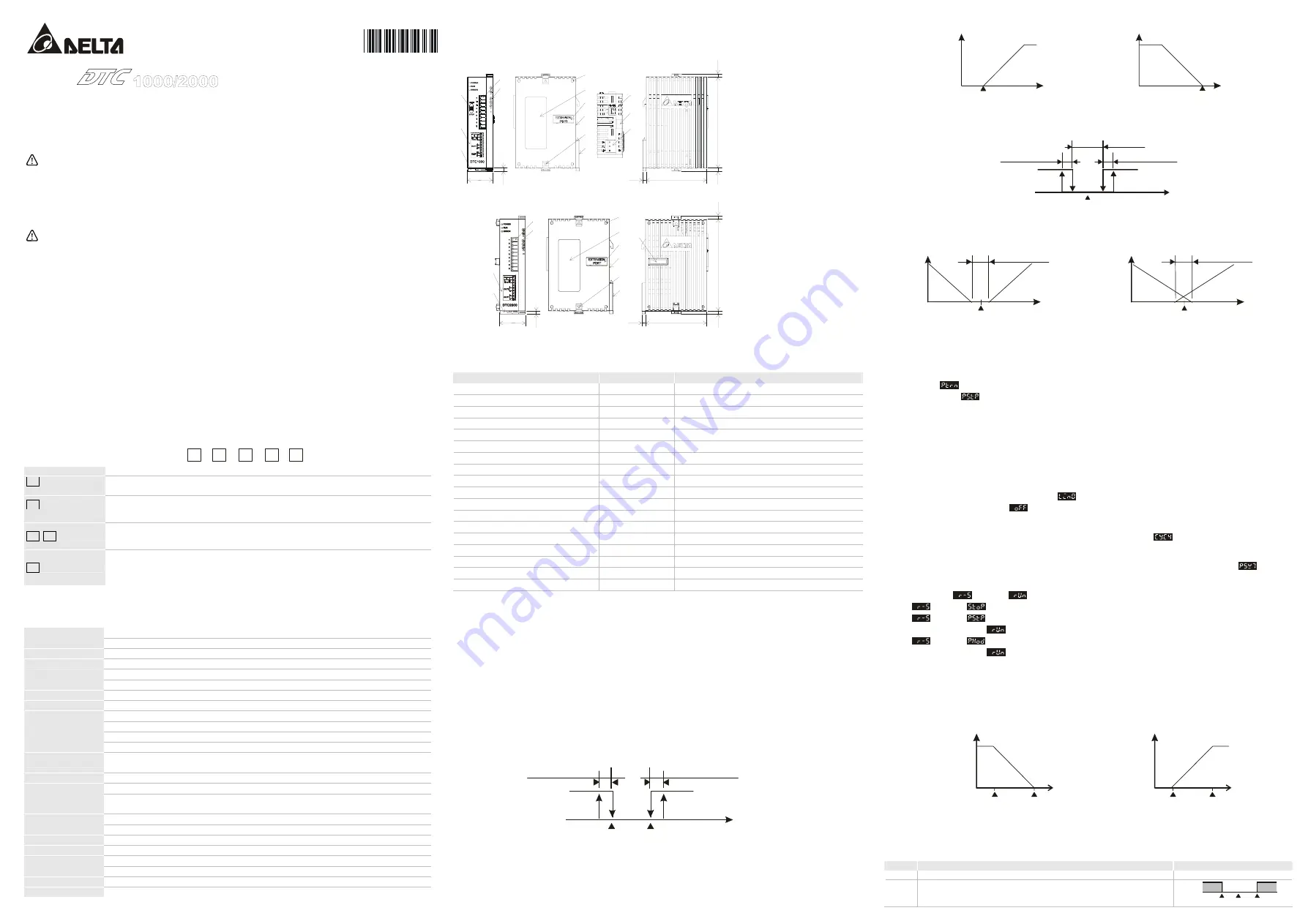
http://www.delta.com.tw/industrialautomation/
5011635003-DCE3
2007-01-25
Temperature Controller
Instruction Sheet
Thank you very much for purchasing DELTA C Series Temperature Controller. Please read this instruction sheet before
using your C series to ensure proper operation and please keep this instruction sheet handy for quick reference.
Caution
DANGER! Caution! Electric Shock!
DTC1000 is an OPEN-TYPE Process Control Equipment and DTC2000 is an OPEN-TYPE Process Control
Accessory. These devices are microprocessor-based temperature regulating controllers which may be provide with
normally closed and/or open contacts. They are intended for installation completely within an overall panel or Process
control Enclosure and are used in heating or cooling applications. Please Install within a separate UL Listed enclosure
only, keep the enclosure away from airbome dust or high humidity and prevent electric shock or sudden shock. Also, it
is equipped with protective methods such as some special tool or key to open the enclosure, so as to avoid the hazard
to users or any damage to the module.
WARNING!
1.
Prevent dust or metallic debris from falling into the controller that will cause malfunction.
2.
Do NOT modify or disassemble the controller.
3.
Do NOT connect to “No Used” terminal.
4.
Do not install and/or use the controller in places subject to:
(a) Dust or corrosive gases and liquid. (b) High humidity and high radiation. (c) Vibration and shock. (d) High voltage
and high frequency
5.
Power off when wiring and changing an input sensor.
6.
Be sure to use compensating wires that match the thermocouple types when extending or connecting the
thermocouple wires.
7.
Shorten the wire when wiring a platinum resistance thermometer (RTD) to the controller and separate power cable
from load wires to prevent interference and conductive influence.
8.
Make sure power cables and signals device are installed properly before power on; otherwise serious damage may
occur.
9.
Do NOT touch the terminals or repair the controller when power on to prevent electric shock.
10.
Wait at least one minute after power off to allow capacitors to discharge, and do not touch any internal circuit within
this period.
11.
Do NOT touch internal terminals no matter power on or off.
12.
For temperature accuracy, keep the controller away from heating source.
Model Name Explanation
D T C 1
2
3
4
5
DTC
Series
DTC: Delta C series Temperature Controller
1
Controller
Position
1: first controller
2: controller in parallel
2
Auxiliary Output
Groups
0: standard, 2 groups output, no auxiliary output
1: 1 group auxiliary output. Not available now.
2: 2 groups auxiliary output. Not available now.
3 4
Optional
00: standard
01: CT input. Not available now.
02: Event input. Not available now.
5
Main Output Type
R: Relay output SPST, 250VAC, 3A
V: Voltage Pulse output 12V +10% ~ -20%
C: Current output 4 ~ 20mA
L: Linear Voltage output 0 ~ 10V
Standard: DC24V input, Relay output for 2
nd
group, RS-485 communication.
Function & Specification
Power supply
DC24V. Isolated switching power
Voltage range
Rated voltage: 90% ~ 110%
Power consumption
Rated 24 Vdc, Max. 24 W combined, 3 W + 3 W x no. of DTC-2000 (max. 7 connected)
Thermocouple: K, J, T, E, N, R, S, B, L, U, TXK
Platinum RTD: Pt100, JPt100
Sensor type
Linear DC input: 0 ~ 5V, 0 ~ 10V, 0 ~ 20mA, 4 ~ 20mA, 0 ~ 50mV
Sampling rate
Analog input: 0.15 sec. Thermocouple or Platinum RTD: 0.4 sec.
Control method
PID , PID program control, Manual or ON/OFF
Relay output (SPST), Max. load 250VAC, 3A resistive load
Voltage pulse output: DC 12V, Max. output current 40mA
Current output: DC4 ~ 20m A output (Load resistance: Max. 500
Ω
)
Output type
Analog voltage output: 0 ~ 10V (Load resistance shall be higher than 1000
Ω
)
Output function
Control output, Alarm output, or Retransmission output (only for linear voltage and current
output as 1
st
group)
Alarm function
12 Alarm mode selections
Communication
RS-485 digital communication, 2,400bps ~ 38,400bps.
Communication
protocol
Mod-bus communication protocol, support RTU/ASCII.
Internal connection
Provide internal connection terminals to transmit 24V power supply and communication signal.
Vibration resistance
10 to 55Hz, 10m/s
2
for 10min, each in X, Y and Z directions
Shock resistance
Max. 300m/s
2
, 3 times in each 3 axes, 6 directions
Ambient temperature 0
o
C to + 50
o
C
Storage temperature -20
o
C to +65
o
C
Altitude
2,000m or less
Relative humidity
35% to 85% RH (non-condensing)
Pollution degree
Degree 2
Product Profile & Outline
DTC1000R/V/C/L
1 RUN/STOP
switch
2
Wiring and Model name
3 DIN
fix
4 I/O
terminals
5 LED
indicators
6
Extension hole of the extension
unit mounting pins
7 Specification
label
8 Extension
port
9 Extension
clip
10 DIN rail
11 RS-485 communication port
12 Extension clip
13 DC power input
9
0
.0
3
.0
60.0
3.4
25.2
4
.0
3
.0
1
2
3
4
5
6
7
8
9
10
3
11
12
13
DTC2000R/V/C/L
1
Wiring and Model name
2
DIN rail clip
3 I/O
terminals
4 LED
indicators
5
Extension hole of the extension
unit mounting pins
6 Specification
label
7 Extension
port
8 Extension
clip
9 DIN
rail
9
0
.0
3
.0
60.0
3.4
25.2
4
.0
3
.0
1
2
3
4
5
6
7
8
9
2
10
10 Extension port
Input Sensor Type
Input Selection for DTC series:
Input Sensor Type
Register Value
Available Range
0 ~ 50mV linear voltage input
17
0 ~ 50mV
4 ~ 20mA linear current input
16
4 ~ 20mA
0 ~ 20mA linear current input
15
0 ~ 20mA
0 ~ 10V linear voltage input
14
0 ~ 10V
0 ~ 5V linear voltage input
13
0 ~ 5V
Platinum RTD (Pt100)
12
-200 ~ 600
o
C (-328 ~ 1,112
o
F)
Platinum RTD (JPt100)
11
-20 ~ 400
o
C (-4 ~ 752
o
F)
Thermocouple TXK type
10
-200 ~ 800
o
C (-328 ~ 1472
o
F)
Thermocouple U type
9
-200 ~ 500
o
C (-328 ~ 932
o
F)
Thermocouple L type
8
-200 ~ 850
o
C (-328 ~ 1562
o
F)
Thermocouple B type
7
100 ~ 1,800
o
C (212 ~ 3,272
o
F)
Thermocouple S type
6
0 ~ 1,700
o
C (32 ~ 3,092
o
F)
Thermocouple R type
5
0 ~ 1,700
o
C (32 ~ 3,092
o
F)
Thermocouple N type
4
-200 ~ 1,300
o
C (-328 ~ 2,372
o
F)
Thermocouple E type
3
0 ~ 600
o
C (32 ~1,112
o
F)
Thermocouple T type
2
-200 ~ 400
o
C (-328 ~ 752
o
F)
Thermocouple J type
1
-100 ~ 1,200
o
C (-148 ~ 2,192
o
F)
Thermocouple K type
0
-200 ~ 1,300
o
C (-328 ~ 2,372
o
F)
Note 1: An internal 249
Ω
precision resistor for the current input is built-in, please refer to the item, How To Set Up Current Input.
Note 2: Factory setting: PT100 input. It is adjustable for linear input and feedback ranges. The default range of input feedback is -999 ~ 9,999. For
example, when a 0 ~ 20mA analog input is selected as the input temperature sensor type, -999 indicates 0mA and 9,999 indicates 20mA. If
change the input range to 0 ~ 2,000, then 0 indicates 0mA and 2,000 indicates 20mA. One display scale is equal to 0.01mA.
Output Function
Output control for DTC is selective: Control output (heating, cooling), Alarm output, or Retransmission output.
Control Output:
Temperature can individually be controlled by two groups of outputs: cooling (forward) or heating (reverse). When Dual
Loop output control is used, two output controls shall be designed for cooling (forward) or heating (reverse). If two
control outputs with the same direction are performed, only 1
st
group control period is valid. Control methods: PID
control, ON/OFF control, Manual control, and PID program control.
Single-output Control:
heating hysteresis
ON
OFF
PV
Figure1: ON-OFF control of single output
cooling hysteresis
Heating
Cooling
Set Point
Set Point
PV
100%
0
Heating
Output
PV
100%
0
Output
Set Point
Cooling
Set Point
Figure 2: PID Control, forward (cooling) control
Figure 3: PID Control, reverse (heating) control
Dual Output Control:
OFF
PV
Set point
ON
Heating
dead band
heating hysteresis
Figure 4.
of dual loop output
ON-OFF control
cooling hysteresis
Cooling
dead band: dead
band width: negative
PV
0
PV
0
dead band: dead
band width: positive
Output
Heating
Cooling
Set Point
Output
Heating
Cooling
Set Point
Figure 5: PID control, Dead band is positive
Figure 6: PID control, Dead band is negative
Description of Function and Parameters Setting:
PID program control by 8 patterns (Pattern No. 0~7) is supported in DTB series. Each pattern contains 8 steps (step
No. 0 ~ 7), one Link Pattern parameter, one Cycle parameter and one Actual Step parameter.
Start Pattern:
is in operation mode and it is used to set the Start Pattern of PID program control (This
parameter appear in
mode only).
Steps:
Include set point X and execution time T, these two parameters setting. The set point (SV) should reach
temperature X after the period of execution time T. If the set point is the same as the result of the previous setting,
then it is called Soak program control. If not, then it is called Ramp program control. Therefore, PID program control is
also called Ramp/Soak program control.
The default of step No. 0 in this controller is Soak program control. The controller will control the temperature (PV) to
reach the set point X and then keep the temperature at set point X. The period of execution time is time T which
provided by step No. 0.
Link Pattern Parameter:
For example, when set
to 2, it indicates that pattern No. 2 will execute next after the
execution of pattern No. 0. If set to
, it indicates the program will stop after executing the current pattern and
the temperature will keep at the set point of the last step.
Cycle Parameter:
Additional execution cycle number. For example, when set
to 2, it indicates that pattern No.
4 should execute twice in addition. Including the origin one time execution, the pattern executes totally three times.
Actual Step Parameter:
Execution step number per pattern (can set to 0 ~ 7). For example, when set
to 2, it
indicates that pattern No 7 will not execute other steps than step 0 to step2.
Execution:
When
is set to
, the program will start to execute in order from the step 0 of start pattern.
When
is set to
, the program will stop and the control output is disabled.
When
is set to
, the program will stop and the temperature at that time will be controlled at the set point
before program stop. Select
again, then the program will restart and execute from step 0 of start pattern.
When
is set to
, the program will hold and the temperature at that time will be controlled at the set point
before program hold. Select
again, then the program will follow the step before hold and start to execute
through the rest of the time.
Retransmission Output:
When the 1
st
group output of this controller is linear voltage or current output, it can be Retransmission that is the output
variation corresponding with input. For example, when read value = 0 with input range 0 ~ 1,000, output will be 0mA or
0V. When read value = 1,000, output will be 20mA or 10V.
Figure 7: Retransmission
Output
PV Low
PV High
Output
10V or 20mA
0V or 4mA
PV Low
PV High
Output slope
is negative
PV
PV
Output slope is positive
10V or 20mA
0V or 4mA
Alarm Output:
This controller provides twelve types of alarm input selections. When PV is higher or lower than SV, alarm output will act.
Following table consists of twelve alarm output modes.
SV
Alarm Type
Alarm Output Function
0
No Alarm Function
Output is OFF
1
Deviation upper- and lower-limit:
This alarm output operates when PV value is higher than the setting value
SV+ (AL-H) or lower than the setting value SV- (AL-L).
ON
OFF
AL-L
SV
AL-H