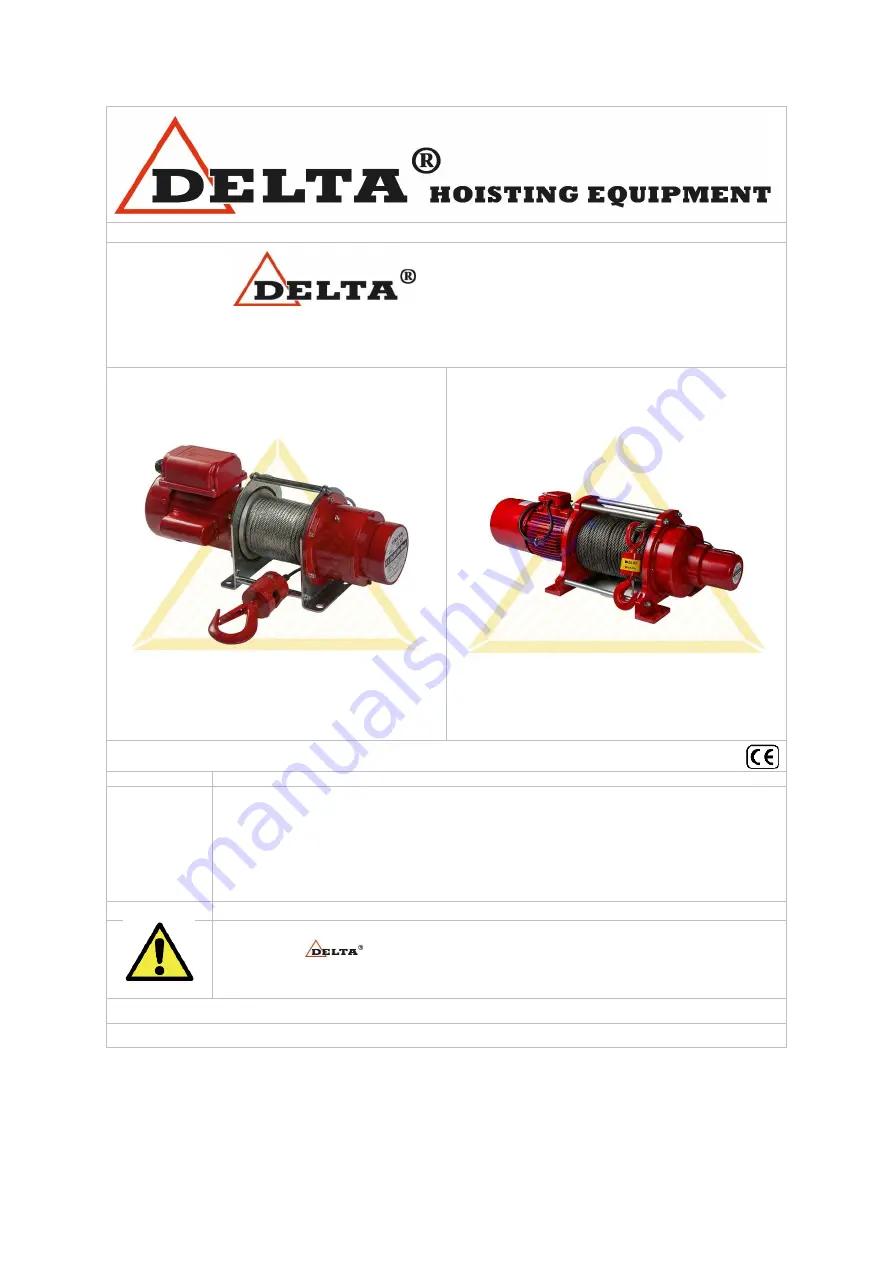
Original instructions
OPERATIONS MANUAL
ELECTRIC WINCHES 230/400 VOLT
[CP.0.DPS / DPT series]
CP.0.DPS SERIES 230 VOLT
CP.0.DPT SERIES 400 VOLT
NOTE:
All of the information reported herein is based on data available at the moment of
printing. We reserve the right to modify our own products at any moment without
notice. Please read the operating instructions carefully before using this product.
Always keep a copy of this instruction manual at hand. Failure to read and comply
with the contents of this manual can result in serious body injury or death, and
property damage.
THIS IS THE SAFETY ALERT SYMBOL. WHEN YOU SEE THIS SYMBOL
ON YOUR
PRODUCTS OR IN THIS MANUAL, BE ALERT FOR
DANGEROUS SITUATIONS. FOLLOW RECOMMENDED AND SAFE
OPERATING INSTRUCTIONS AT ALL TIMES.
If any doubt remains, please contact your supplier.
Summary of Contents for CP.0.DPS Series
Page 8: ...8 3 2 2 electric pulling winch capacity per layer ...
Page 21: ...21 CP 0 DPS 200 Control Circuit ...
Page 23: ...23 CP 0 DPS 250 Control Circuit ...
Page 25: ...25 CP 0 DPS 300 Control Circuit ...
Page 27: ...27 CP 0 DPS 500 Control Circuit ...
Page 29: ...29 CP 0 DPT 30075 Control Circuit ...
Page 31: ...31 CP 0 DPT 30151 Control Circuit ...
Page 33: ...33 CP 0 DPT 30375 Control Circuit ...
Page 35: ...35 CP 0 DPT 30750 Control Circuit ...
Page 37: ...37 CP 0 DPT 31500 Control Circuit ...
Page 39: ...39 CP 0 DPT 34000 Control Circuit ...
Page 40: ...40 9 Derived certificate of test Declaration of CE conformity ...