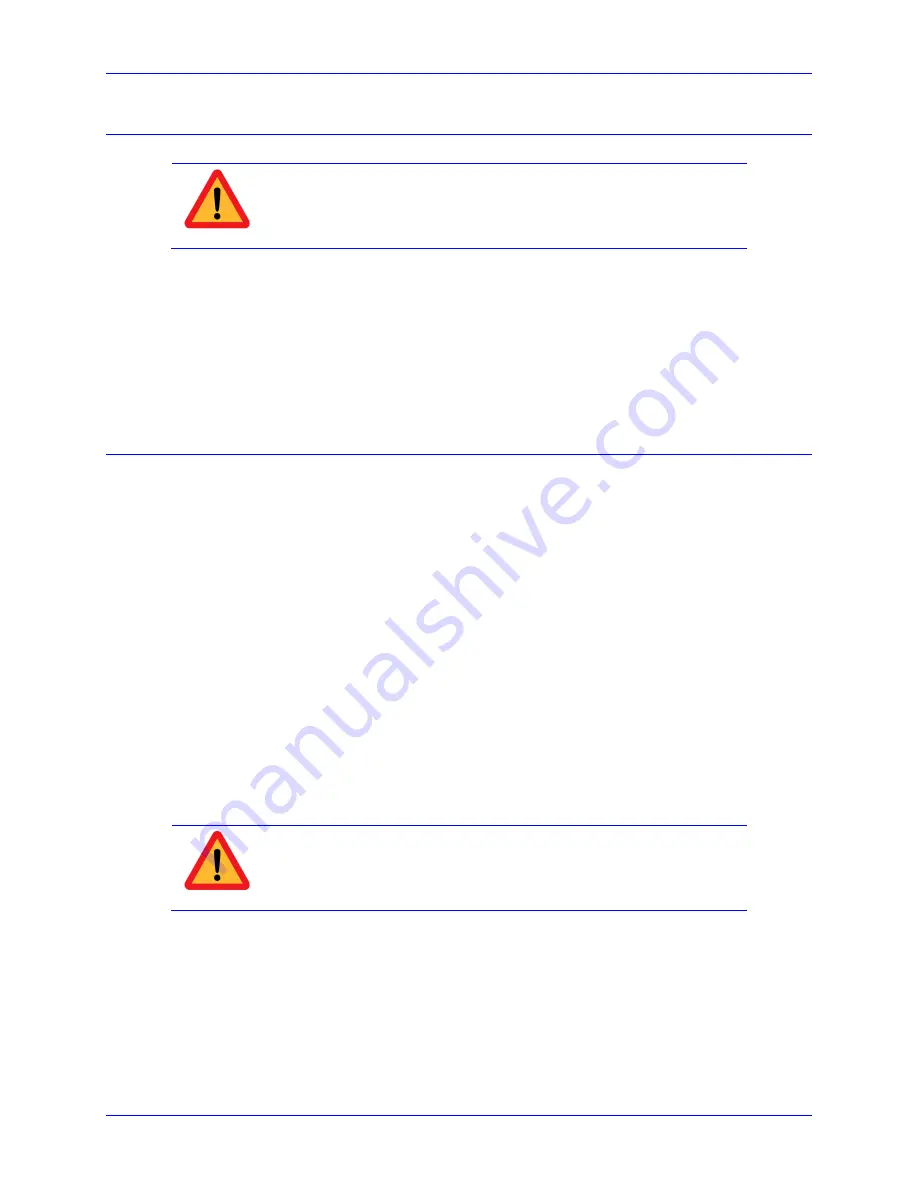
Geo Brick Drive User Manual
Macro Connectivity
260
Absolute Position Reporting over MACRO
Caution
Writing to the motor actual position (Mxx62) should only be done
when the motor is killed.
The Geo Brick Drive supports a wide variety of absolute encoders. When used as a MACRO slave, the
simplest way to report the absolute position to the master (ring controller) is to use the MACRO auxiliary
communication (read/write).
Example:
Retrieving motor #9’s absolute position from motor #1 on a slave Brick yields the online
command (using suggested M-Variables Mxx62):
MXR0,M162,M962
which could be ultimately
inserted in an initialization PLC.
MACRO Configuration Power-Up Sequence
Typically, in a MACRO master-slave configuration, it is desirable to power up the slave first and then the
master. This ensures proper establishment of MACRO communication. If this is not desirable or possible,
the following procedure should ensure that MACRO communication is properly initiated. But either way,
clearing MACRO ring faults is always recommended on power up in the following order:
1.
Power up slave (logic power).
2.
Issue a local clear fault command – in an initialization PLC.
CMD
"CLRF"
3.
Power-up master (logic power).
4.
Insert a 1 second delay in an initialization PLC
This allows the slave to clear its own fault locally first.
5.
Issue a local clear fault command – in the initialization PLC.
CMD
"CLRF"
6.
Insert a 250 millisecond delay
7.
Broadcast a MACRO clear fault command – in the same PLC
CMD
"MSCLRF15"
8.
Insert a 250 millisecond delay
Caution
Make sure that the PLC logic is latched properly (scan initialization
PLCs once), sending CLRF and MSCLRF commands repeatedly locks
up MACRO communication.
Summary of Contents for Geo Brick
Page 5: ...4...
Page 288: ...Geo Brick Drive User Manual Appendix A 288 Limits Flags J4...