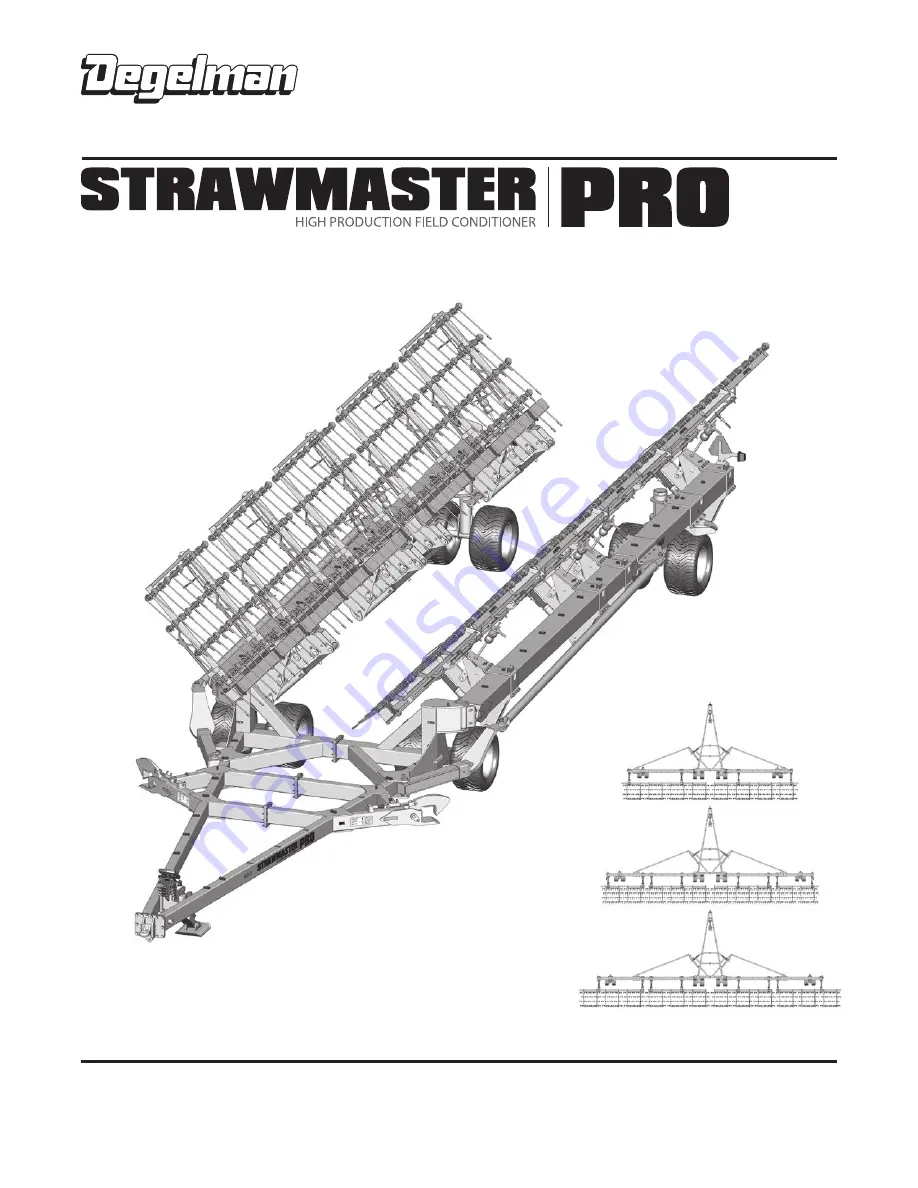
OPERATOR & PARTS
MANUAL
D E G E L M A N I N D U S T R I E S L T D.
B O X 8 3 0 - 2 7 2 I N D U S T R I A L D R I V E ,
R E G I N A , S K , C A N A D A , S 4 P 3 B 1
F A X 306.543.2140 P H 3 0 6 . 5 4 3 . 4 4 4 7
1 . 8 0 0 . 6 6 7 . 3 5 4 5 D E G E L M A N . C O M
STRAWMASTER PRO
80’, 100’ & 120’
Serial Numbers: SM-7557 and up
142646 v2.2