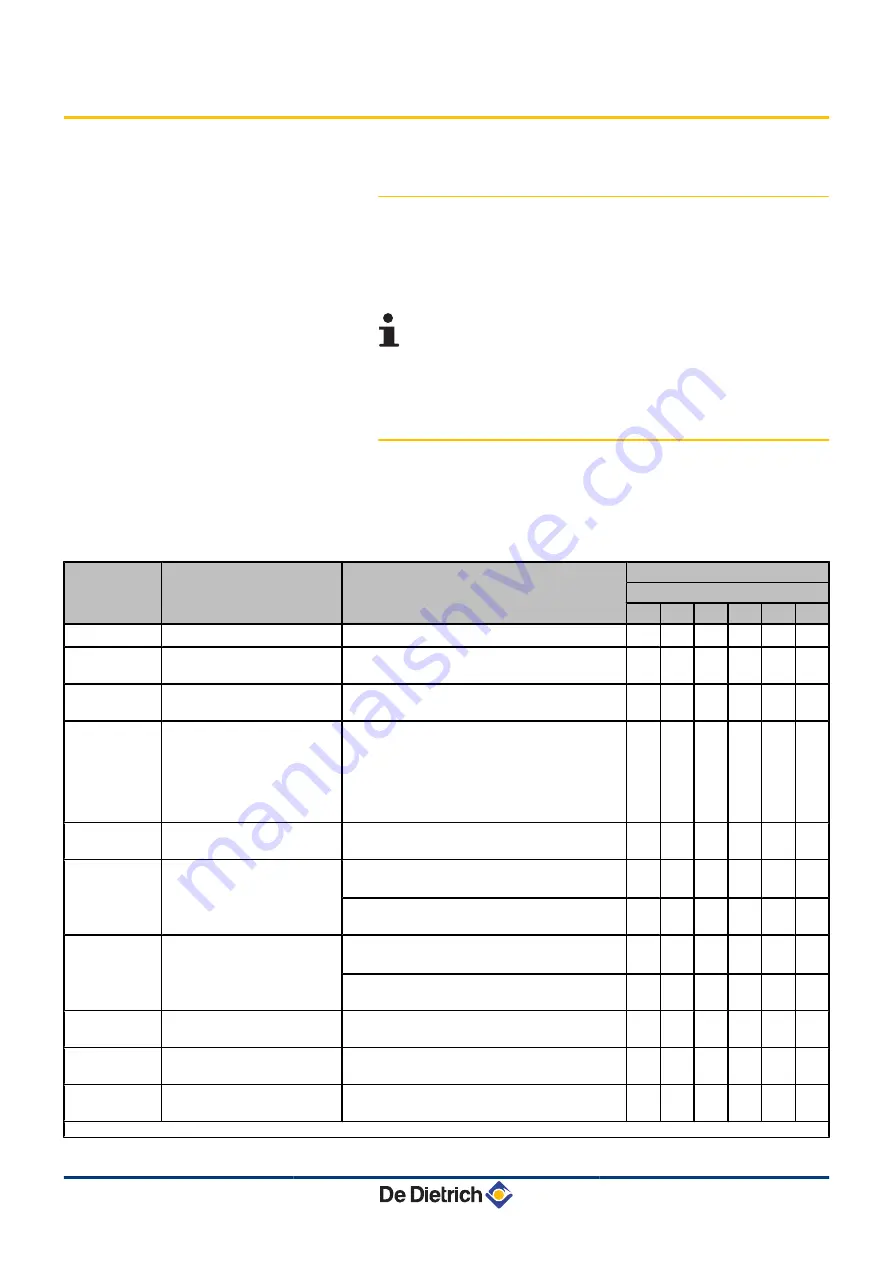
5.4
Changing the settings
5.4.1.
General
The boiler control panel is set for the most common heating
systems. With these settings, practically all heating systems operate
correctly. The user or installer can optimise the parameters according
to own preferences.
For the settings of the
C630 Eco
boiler: The parameters
and settings described are for each boiler module. Each
parameter changing must therefore be done identical on
each module.
5.4.2.
Parameter descriptions
n
Boiler type C 330 ECO
Parameter
Description
Adjustment range
Factory setting
C 330 ECO
280 350 430 500 570 650
p1
Flow temperature: T
SET
20 to 90 °C
80
80
80
80
80
80
p2
Post-circulation of the pump 1 to 98 minutes
99 minutes = continuous
5
5
5
5
5
5
p3
Boiler regulation
0 = Heating deactivated
1 = Heating activated
1
1
1
1
1
1
p4
Display screen
0 = Simple
1 = Comprehensive
2 = Automatic switching to simple after 3
minutes
3 = Automatic switching to simple after 3
minutes; Key blocking is active
2
2
2
2
2
2
p5
Brightness of display lighting 0 = Dimmed
1 = Bright
1
1
1
1
1
1
p17
Maximum fan speed
G25 (Gas L)
(1)
(x100 rpm)
53
56
35
38
43
42
G20 (Gas H)
(x100 rpm)
52
55
35
38
43
41
p18
Minimum fan speed
G25 (Gas L)
(1)
(x100 rpm)
14
15
9
10
11
10
G20 (Gas H)
(x100 rpm)
14
15
9
10
11
10
p19
offset Minimum fan speed
Do not modify
(x1 rpm)
0
50
50
50
0
50
p20
Start speed
Do not modify
(x100 rpm)
25
25
13
14
14
14
p21
Maximum flow temperature
of system
0 to 90 °C
90
90
90
90
90
90
(1) Do not modify these factory settings unless absolutely necessary. E.g. to adapt the boiler to: G20 (Gas H)
5. Commissioning
IniControl For C 330 / C 630 ECO
19
260216 - 7600717-001-06