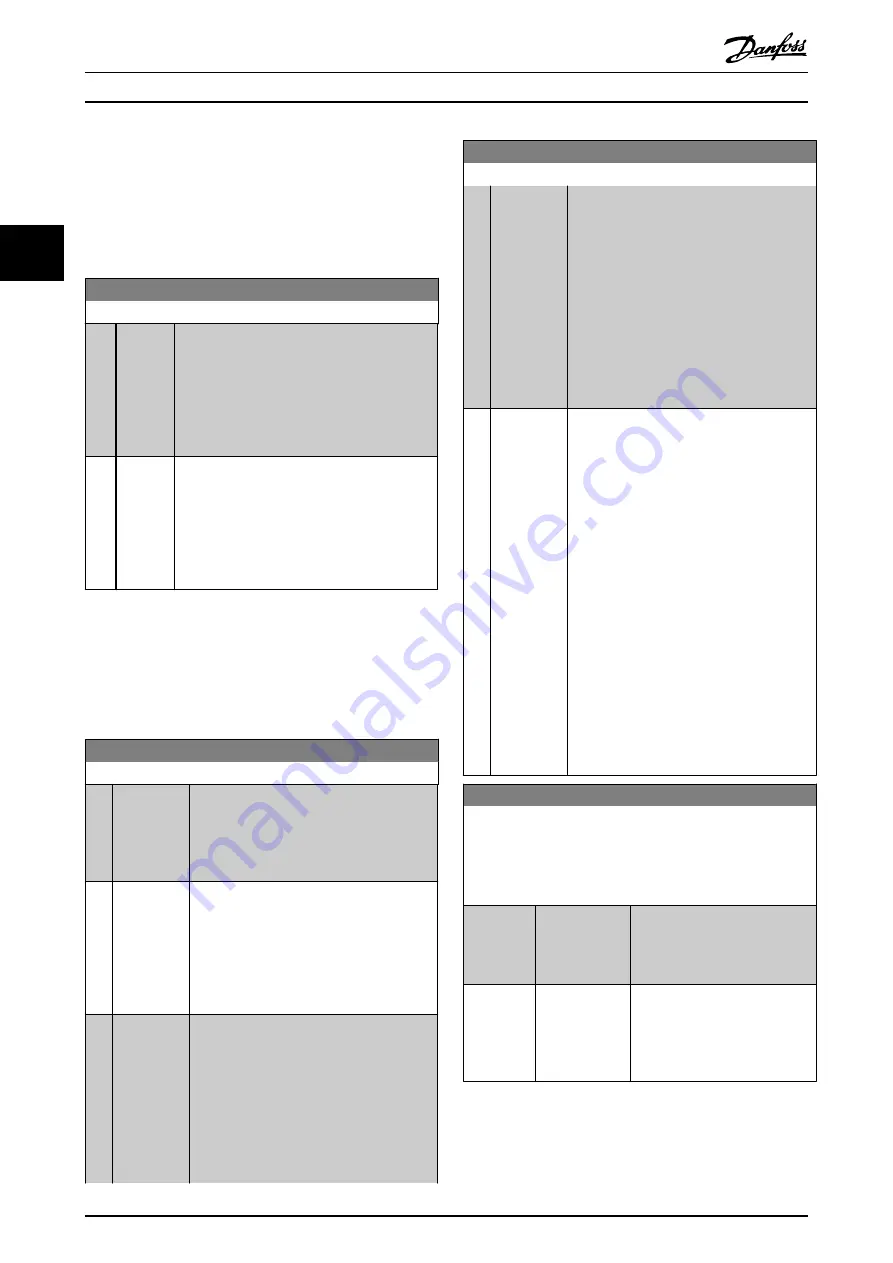
3.3 Main Menu - Load and Motor - Group 1
3.3.1 1-0* General Settings
Define whether the frequency converter operates in open
loop or closed loop.
1-00 Configuration Mode
Option:
Function:
[0]
*
Open
Loop
Motor speed is determined by applying a speed
reference or by setting desired speed when in
Hand Mode.
Open Loop is also used if the frequency converter
is t of a closed loop control system based on an
external PID controller providing a speed
reference signal as output.
[3]
Closed
Loop
Motor Speed will be determined by a reference
from the built-in PID controller varying the motor
speed as t of a closed loop control process (e.g.
constant pressure or flow). The PID controller
must be configured in ameter group20-** or via
the Function Setups accessed by pressing the
[Quick Menus] button.
NOTE
This ameter cannot be changed when motor is running.
NOTE
When set for Closed Loop, the commands Reversing and
Start Reversing will not reverse the direction of the motor.
1-03 Torque Characteristics
Option:
Function:
[0]
*
Compressor
torque
Compressor
[0]: For speed control of screw and
scroll compressors. Provides a voltage which is
optimized for a constant torque load charac-
teristic of the motor in the entire range down
to 10 Hz.
[1] Variable
torque
Variable Torque
[1]: For speed control of
centrifugal pumps and fans. Also to be used
when controlling more than one motor from
the same frequency converter (e.g. multiple
condenser fans or cooling tower fans). Provides
a voltage which is optimized for a squared
torque load characteristic of the motor.
[2] Auto Energy
Optim. CT
Auto Energy Optimization Compressor
[2]: For
optimum energy efficient speed control of
screw and scroll compressors. Provides a
voltage which is optimized for a constant
torque load characteristic of the motor in the
entire range down to 15Hz but in addition the
AEO feature will adapt the voltage exactly to
the current load situation, thereby reducing
energy consumption and audible noise from
1-03 Torque Characteristics
Option:
Function:
the motor. To obtain optimal performance, the
motor power factor cos phi must be set
correctly. This value is set in
. The parameter has a default value
which is automatically adjusted when the
motor data is programmed. These settings will
typically ensure optimum motor voltage but if
the motor power factor cos phi requires tuning,
an AMA function can be carried out using
1-29 Automatic Motor Adaptation (AMA)
. It is
very rarely necessary to adjust the motor
power factor parameter manually.
[3]
*
Auto Energy
Optim. VT
Auto Energy Optimization VT
[3]: For optimum
energy efficient speed control of centrifugal
pumps and fans. Provides a voltage which is
optimized for a squared torque load charac-
teristic of the motor but in addition the AEO
feature will adapt the voltage exactly to the
current load situation, thereby reducing energy
consumption and audible noise from the
motor. To obtain optimal performance, the
motor power factor cos phi must be set
correctly. This value is set in
. The parameter has a default value and
is automatically adjusted when the motor data
is programmed. These settings will typically
ensure optimum motor voltage but if the
motor power factor cos phi requires tuning, an
AMA function can be carried out using
1-29 Automatic Motor Adaptation (AMA)
. It is
very rarely necessary to adjust the motor
power factor parameter manually.
1-06 Clockwise Direction
This parameter defines the term “Clockwise” corresponding to the
LCP direction arrow. Used for easy change of direction of shaft
rotation without swapping motor wires. (Valid from SW version
5.84)
Option:
Function:
[0]
*
Normal
Motor shaft will turn in clockwise
direction when frequency
converter is connected U -> U; V ->
V, and W -> W to motor.
[1]
Inverse
Motor shaft will turn in counter
clockwise direction when
frequency converter is connected
U -> U; V -> V, and W -> W to
motor.
This parameter cannot be changed while the motor is
running.
Parameter Description
VLT
®
HVAC Drive Programming Guide
38
MG.11.CB.02 - VLT
®
is a registered Danfoss trademark
3
3