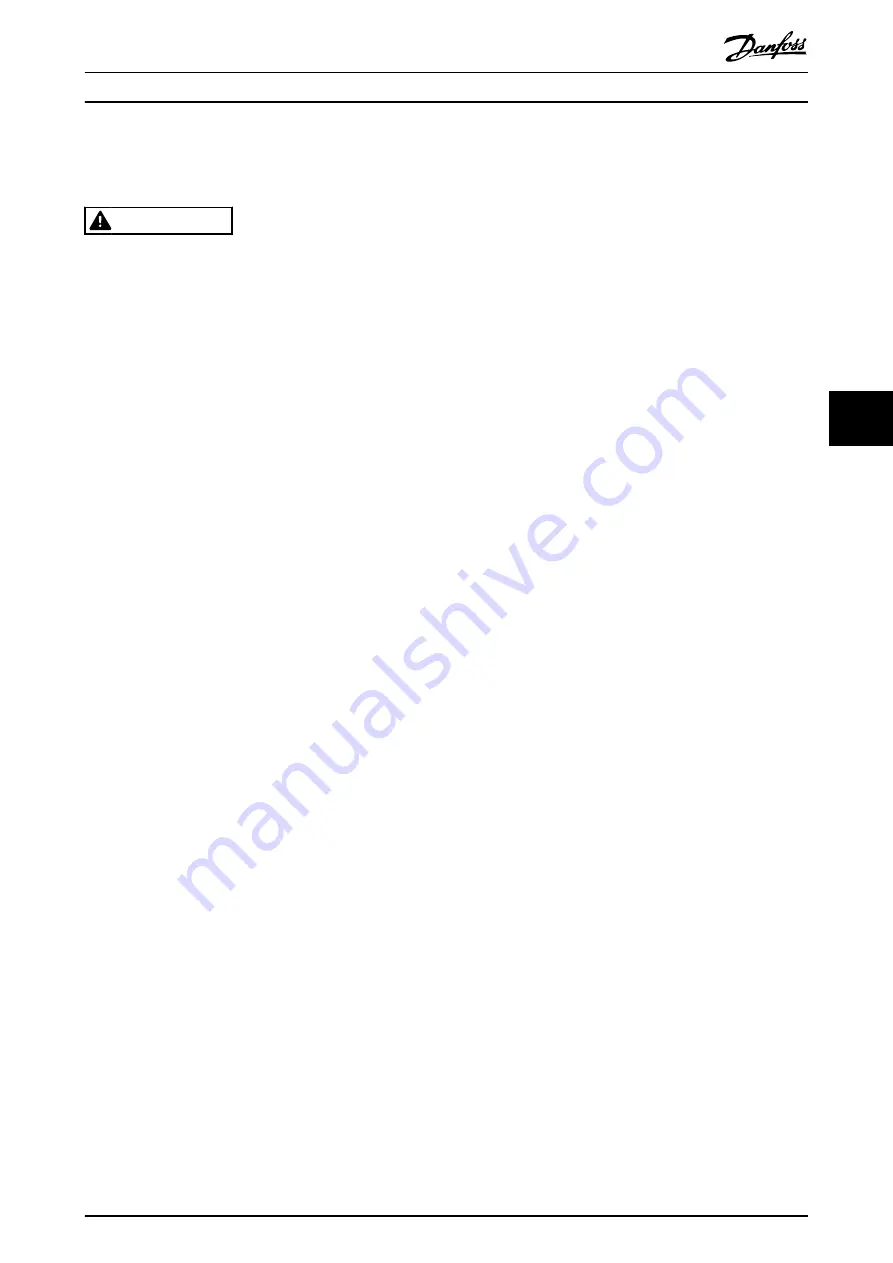
6 Commissioning
WARNING
UNINTENDED START
The ISD 510 servo system contains servo drives that are
connected to the electrical supply network and can start
running at any time. This may be caused by a fieldbus
command, a reference signal, or by clearing a fault
condition. Servo drives and all connected devices must
be in good operating condition. A deficient operating
condition may lead to death, serious injury, damage to
equipment, or other material damage when the servo
drive is connected to the electrical supply network.
•
Take suitable measures to prevent unintended
starts.
6.1 Pre-Commissioning Checklist
Always check the following before initial commissioning
and before commencing operation after extended
downtime or storage:
•
Are all threaded connectors of mechanical and
electrical components firmly tightened?
•
Is the free circulation of cooling air (inlet and
outlet) assured?
•
Are the electrical connections correct?
•
Is contact protection in place for rotating parts
and surfaces that can become hot?
6.2 ID Assignment
6.2.1 EtherCAT
®
EtherCAT
®
needs no special ID assignment (IP address).
Special ID assignment is only required, when using indirect
communication via the ISD Toolbox software (see
chapter 6.5.4 ISD Toolbox Communication
for further
information).
6.2.2 Ethernet POWERLINK
®
Ethernet POWERLINK
®
master communication cannot be
active when using the ISD Toolbox to assign IDs to the
devices. ID assignment via the ISD Toolbox is only possible
when acyclic Ethernet POWERLINK
®
communication is
used. If cyclic communication is already started, send an
NMT reset
command to all devices manually or perform a
power cycle to stop the cyclic Ethernet POWERLINK
®
communication.
6.2.2.1 Single Device ID Assignment
When assigning an ID to a single device, the
Device
Information
window in the ISD Toolbox can be used (see
the
VLT
®
Integrated Servo Drive ISD
®
510 System
Programming Guide
for more information). Setting an ID to
a device can also be done via the LCP.
Setting the node ID directly on a servo drive or on the
SAB
All IP-related parameters are located in parameter group
12-0* IP Settings
. According to the Ethernet POWERLINK
®
standard, the IP address is fixed to 192.168.100.xxx. The
last number is the value in parameter
12-60 Node ID
. For
parameter
12-02 Subnet Mask
, the IP address is fixed to
255.255.255.0 and cannot be changed.
Attach the LCP to the servo drive or SAB for which the
Node ID
should be changed. Change the value in
parameter
12-60 Node ID
to select the desired IP address.
Setting the Node ID for a single servo drive via the SAB
It is also possible to change the
Node ID
of a servo drive
when the LCP is connected to the SAB. This functionality is
contained in parameter group
54-** ID Assignment
on the
SAB in sub-group
54-1* Manual
.
1.
Attach the LCP to the SAB that is connected to
the servo drive for which the
Node ID
should be
changed.
2.
Configure the parameters:
2a
54-10 EPL ID assignment line
2b
54-11 Drive index
(position of the servo
drive in the line)
2c
54-12 EPL ID assignment assign ID
3.
Set parameter
54-13 EPL ID assignment start
to
[1]
start
.
6.2.2.2 Multiple Device ID Assignment
When assigning IDs to several devices (for example, when
setting up a new machine), the ISD Toolbox sub-tool
SAB
ID assignment
can be used (see the
VLT
®
Integrated Servo
Drive ISD
®
510 System Programming Guide
for more
information). Setting the IDs of all the servo drives
connected to an SAB at the same time can also be done
via the LCP when it is connected to the SAB.
Setting the Node IDs of all servo drives on an SAB line
The automatic SAB ID assignment is used for automatically
setting the
Node IDs
on all servo drives for a specified SAB
line. This functionality is contained in parameter group
54-
** ID Assignment
on the SAB in sub-group
54-0* Automatic
.
Commissioning
Operating Instructions
MG75K102
Danfoss A/S © 12/2015 All rights reserved.
43
6
6