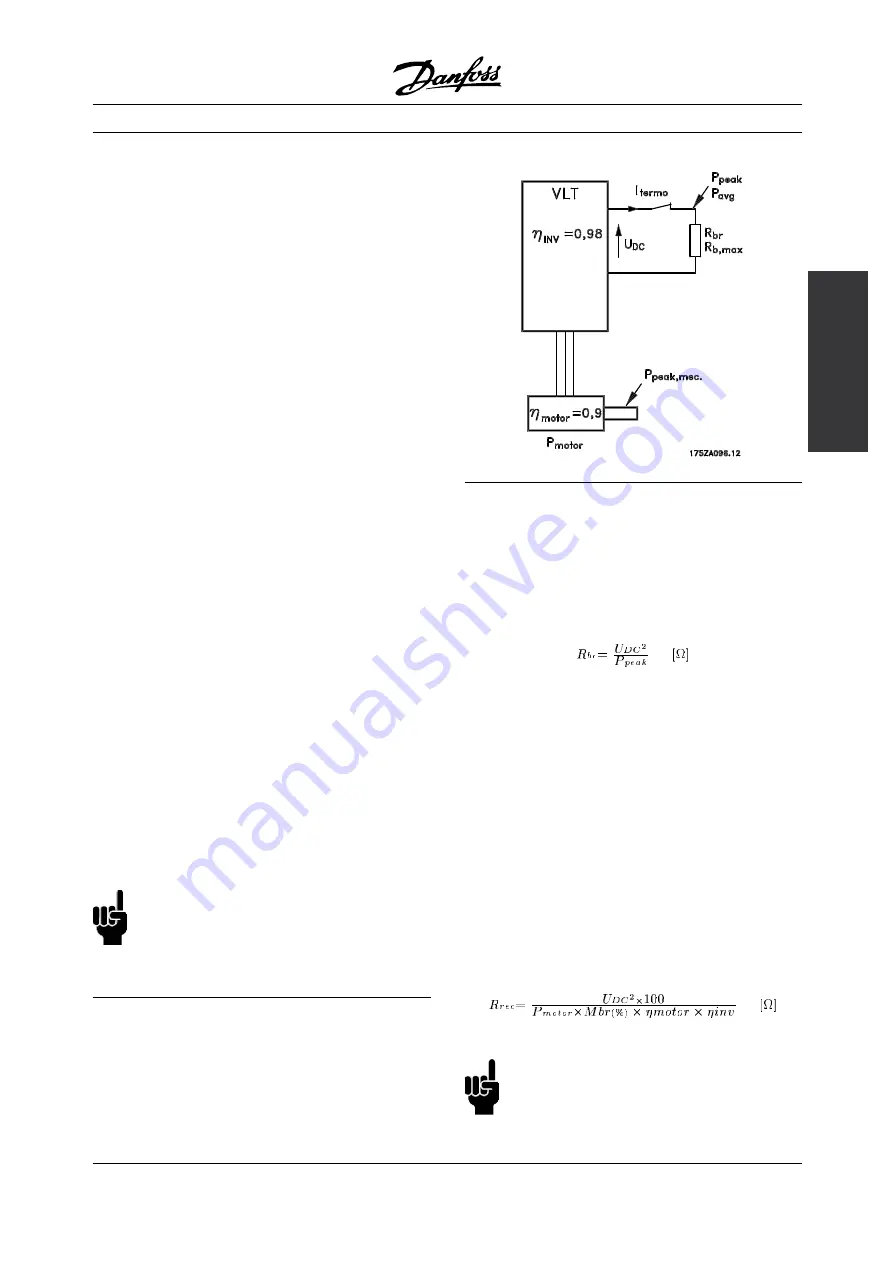
Decentral Solutions
All About FCD
300
■
Dynamic braking
With the FCD 300 the dynamic braking quality in an
application can be improved in two ways, either with
the aid of brake resistors or AC braking.
Danfoss offers a complete range of brake resistors
for all FCD 300 variable frequency drives.
It is the job of the
brake resistor
to apply a
load to the intermediate circuit during braking,
thereby ensuring that the brake power can be
absorbed by the brake resistor.
Without a brake resistor, the intermediate circuit
voltage of the variable frequency drive would go on
rising, until cutting out for protection. The advantage
of using a brake resistor is that you can brake quickly
with large loads, e.g. on a conveyor belt.
Danfoss has chosen a solution in which the brake
resistor is not integrated into the variable frequency
drive. This gives the user the following advantages:
-
The resistor
’
s cycle time can be selected as required.
-
The heat generated during braking can be
diverted outside the panel cabinet, where the
energy can possibly be utilized.
-
No overheating of the electronic components,
even if the brake resistor is overloaded.
An internal brake resistor can be mounted on
the small brake duty cycles.
AC braking
is an integrated function that is used
for applications in which there is a need for limited
dynamic braking. The AC braking function makes
it possible to reduce the brake power in the motor
instead of in a brake resistor. The function is intended
for applications where the required braking torque
is less than 50% of rated torque. AC braking is
selected in par. 400
Brake function
.
NOTE
The AC brake cannot be used if the
required braking torque is more than 50%
of rated braking torque. In such instances
a brake resistor must be used.
■
Brake Setup
The figure shows a brake Setup with a variable
frequency drive.
In the following paragraphs, expressions and
acronyms are used about brake Setups that
can be seen from the figure.
■
Calculation of brake resistance
To ensure that the variable frequency drive does not
cut out for safety reasons when the motor brakes, the
resistance value is selected on the basis of the peak
braking effect and the intermediate circuit voltage:
It can be seen that the brake resistance depends
on the intermediate circuit voltage (UDC).
With variable frequency drives that have a line
voltage of 3 x 380 - 480 Volt, the brake will
be active at 770 Volt (UDC).
You can also choose to use the brake resistance
recommended by Danfoss (R
REC
). This is a
guarantee that the variable frequency drive is able
to brake at the highest braking torque (M
BR
). The
recommended brake resistance can be seen from
the ordering table for brake resistors.
R
REC
calculated as:
NOTE
Remember to check that the brake resistance
can manage a voltage of 850 Volt, if Danfoss
brake resistors are not being used.
MG.90.F2.22 - VLT is a registered Danfoss trademark
173