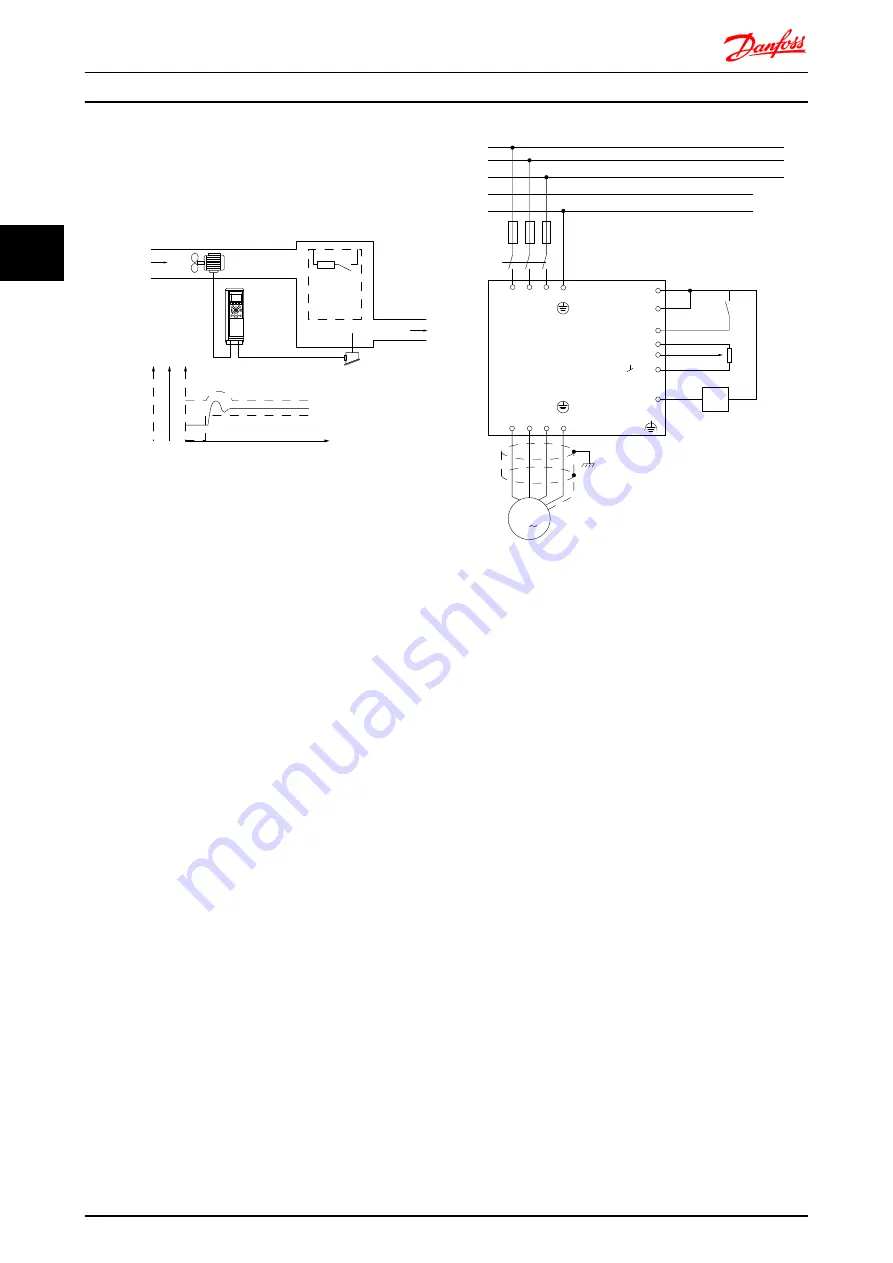
3.4.4 Example of Process PID Control
The following is an example of a Process PID Control used
in a ventilation system:
Temper
atur
e
Fan speed
Temperature
transmitter
Hea
t
Heat
generating
process
Cold air
130BA218.10
100kW
n °C
W
In a ventilation system, the temperature is to be settable
from - 5 - 35°C with a potentiometer of 0-10V. The set
temperature must be kept constant, for which purpose the
Process Control is to be used.
The control is of the inverse type, which means that when
the temperature increases, the ventilation speed is
increased as well, so as to generate more air. When the
temperature drops, the speed is reduced. The transmitter
used is a temperature sensor with a working range of
-10-40
°
C, 4-20 mA. Min. / Max. speed 300 / 1500 RPM.
Transmitter
96 97
99
98
91 92 93 95
50
12
L1 L2
L1
PE
L3
W PE
V
U
F1
L2
L3
N
PE
130BA175.11
18
53
37
55
54
M
3
Illustration 3.7 Two-wire transmitter
1.
Start/Stop via switch connected to terminal 18.
2.
Temperature reference via potentiometer
(-5-35
°
C, 0-10 VDC) connected to terminal 53.
3.
Temperature feedback via transmitter (-10-40
°
C,
4-20 mA) connected to terminal 54. Switch S202
set to ON (current input).
Introduction to FC 300
FC 300 Design Guide
34
MG.33.BD.02 - VLT
®
is a registered Danfoss trademark
3
3