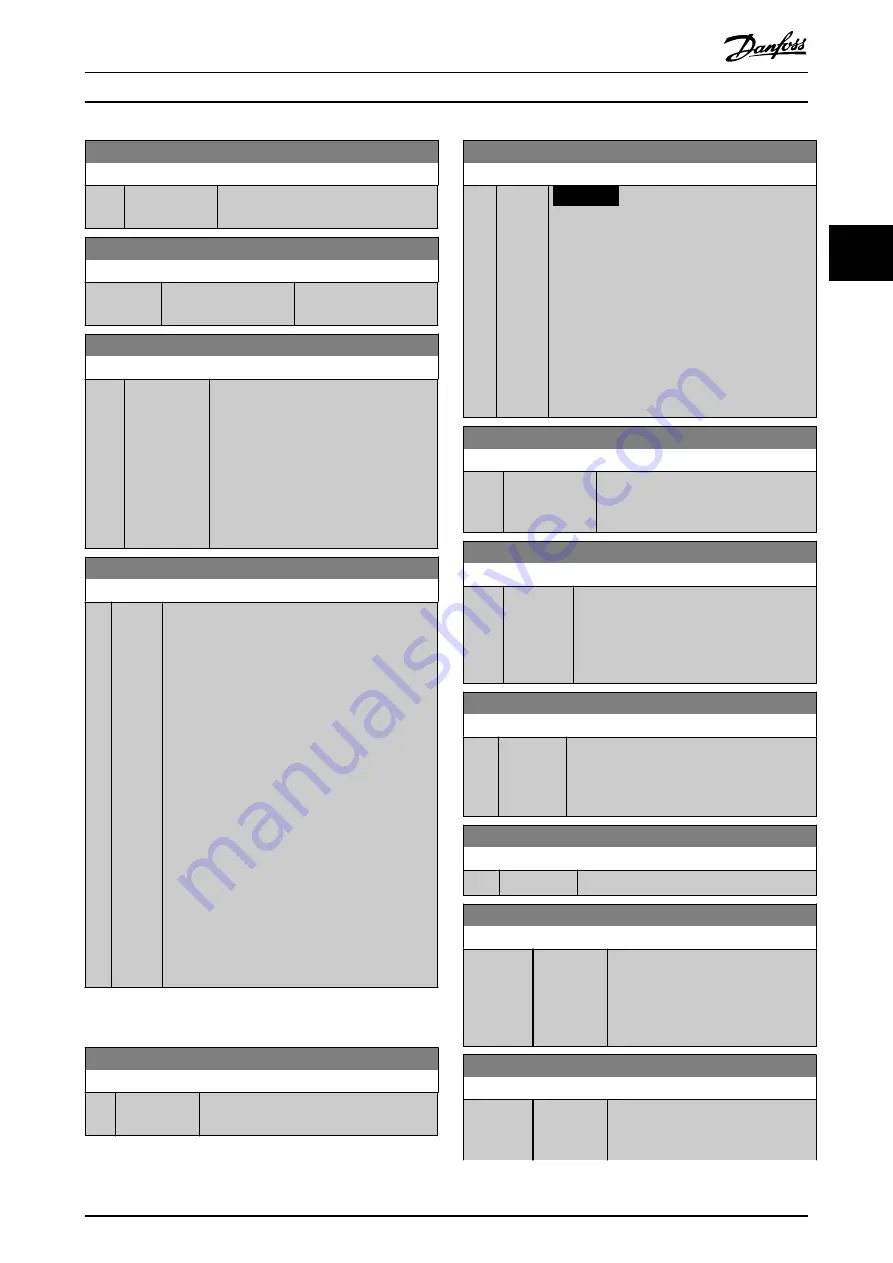
16-23 Motor Shaft Power [kW]
Range:
Function:
0 kW
*
[0 - 10000 kW] Readout of the mechanical power
applied to the motor shaft.
16-24 Calibrated Stator Resistance
Range:
Function:
0.0000 Ohm
*
[0.0000 - 100.0000
Ohm]
Shows the calibrated
stator resistance.
16-25 Torque [Nm] High
Range:
Function:
0
Nm
*
[-200000000
- 200000000
Nm]
View the torque value with sign, applied
to the motor shaft. Some motors supply
more than 160% torque. Therefore, the
minimum value and the maximum value
depend on the maximum motor current
as well as the motor used. This specific
readout has been adapted to be able to
show higher values than the standard
readout in
16-28 Angle Error
Range:
Function:
0 °
*
[-180 -
180 °]
Readout of deviation between sensor less rotor
angle estimation by motor controller and real rotor
angle based on encoder reading. The parameter is
only activated if options in
is set to
[2] Flux Sensorless
and
parameter 1-10 Motor Construction
is set to
[1] PM,
non salient SPM
or
[2] PM, salient IPM
.
The encoder source used for comparison must be
selected in
chapter 3.8.2 7-00 Speed PID Feedback
. To obtain an accurate reading of parameter
16-28, the motor angle offset must be set in
parameter 1-41 Motor Angle Offset
. Rotor detection
is configured in
chapter 3.8.12 7-90 Position PI
which is activated using the
setting in
in
Flux with
motor feedback
.
Parameter 7-90
must be set to
[0]
Motor feedb.P1-02
. The encoder is then only used
for comparison while position control is based on
the estimated sensor less position. This enables to
measure the accuracy of position control in sensor
less mode.
3.16.3 16-3* Drive Status
16-30 DC Link Voltage
Range:
Function:
0 V
*
[0 - 10000 V] View a measured value. The value is filtered
with a 30 ms time constant.
16-31 System Temp.
Range:
Function:
0 °C
*
[-128 -
127 °C]
NOTICE
Valid for FC 302 only.
Shows the highest internal system temperature.
In the smaller enclosure sizes (A–C), the system
temperature matches the control card
temperature measurement in
parameter 16-39 Control Card Temp.
In the larger
enclosure sizes (D–F), the system temperature is
the highest temperature measured on hardware
components with temperature sensors, for
example, the power card(s).
16-32 Brake Energy /s
Range:
Function:
0 kW
*
[0 - 10000 kW] View the brake power transmitted to an
external brake resistor, stated as an
instant value.
16-33 Brake Energy Average
Range:
Function:
0 kW
*
[0 - 10000
kW]
View the brake power transmitted to an
external brake resistor. The mean power is
calculated on an average level based on the
selected time period within
parameter 2-13 Brake Power Monitoring
16-34 Heatsink Temp.
Range:
Function:
0 °C
*
[0 -
255 °C]
View the frequency converter heat sink
temperature. The cutout limit is 90
±
5
°
C (194
±
9
°
F), and the motor cuts back in at 60
±
5
°
C (140
±
9
°
F).
16-35 Inverter Thermal
Range:
Function:
0 %
*
[0 - 100 %] View the percentage load on the inverter.
16-36 Inv. Nom. Current
Range:
Function:
Size
related
*
[0.01 -
10000 A]
View the inverter nominal current,
which must match the nameplate
data on the connected motor. The
data is used for calculation of torque,
motor overload protection, and so on.
16-37 Inv. Max. Current
Range:
Function:
Size
related
*
[0.01 -
10000 A]
View the inverter maximum current,
which must match the nameplate
data on the connected motor. The
Parameter Descriptions
Programming Guide
MG33MP02
Danfoss A/S © 10/2018 All rights reserved.
211
3
3
Summary of Contents for VLT AutomationDrive FC 302
Page 2: ......