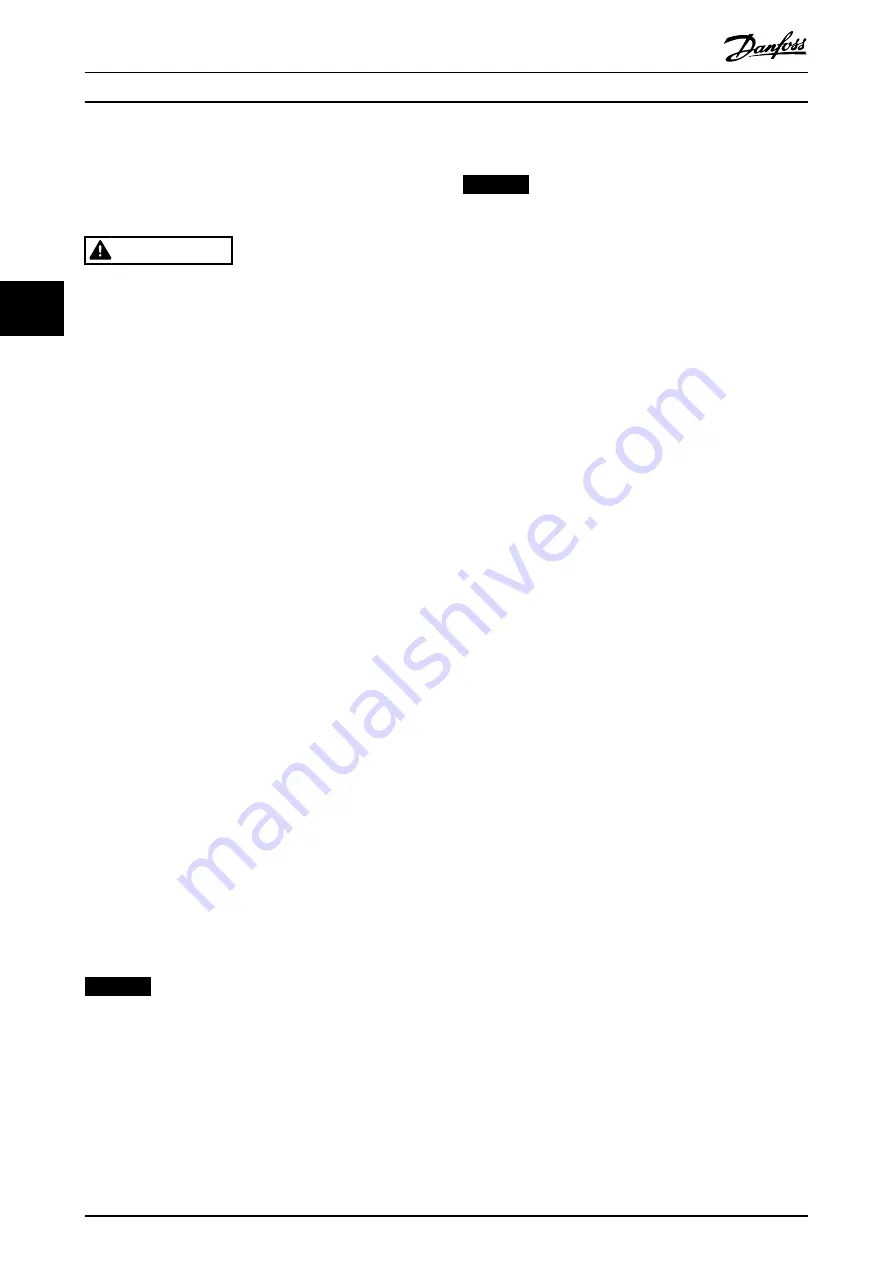
can accumulate on fan blades causing an imbalance which
prevents the fans from properly cooling the unit.
4.4.3 Potentially Explosive Atmospheres
WARNING
EXPLOSIVE ATMOSPHERE
Do not install the drive in a potentially explosive
atmosphere. Install the unit in a cabinet outside of this
area. Failure to follow this guideline increases risk of
death or serious injury.
Systems operated in potentially explosive atmospheres
must fulfill special conditions. EU Directive 94/9/EC
(ATEX 95) classifies the operation of electronic devices in
potentially explosive atmospheres.
•
Class d specifies that if a spark occurs, it is
contained in a protected area.
•
Class e prohibits any occurrence of a spark.
Motors with class d protection
Do not require approval. Special wiring and containment
are required.
Motors with class e protection
When combined with an ATEX–approved PTC monitoring
device like the VLT
®
PTC Thermistor Card MCB 112, the
installation does not need an individual approval from an
approbated organization.
Motors with class d/e protection
The motor itself has an e ignition protection class, while
the motor cabling and connection environment is in
compliance with the d classification. To attenuate the high
peak voltage, use a sine-wave filter at the drive output.
When using a drive in a potentially explosive
atmosphere, use the following:
•
Motors with ignition protection class d or e.
•
PTC temperature sensor to monitor the motor
temperature.
•
Short motor cables.
•
Sine-wave output filters when shielded motor
cables are not used.
NOTICE
MOTOR THERMISTOR SENSOR MONITORING
Drives with the VLT
®
PTC Thermistor Card MCB 112
option are PTB-certified for potentially explosive
atmospheres.
4.5 Installation and Cooling Requirements
NOTICE
MOUNTING PRECAUTIONS
Improper mounting can result in overheating and
reduced performance. Observe all installation and
cooling requirements.
Installation requirements
•
Ensure unit stability by mounting vertically to a
solid flat surface.
•
Ensure that the strength of the mounting location
supports the unit weight. Refer to
chapter 3.2 Power Ratings, Weight, and Dimensions
.
•
Ensure that the mounting location allows access
to open the enclosure door. See
chapter 10.9 Enclosure Dimensions
.
•
Ensure that there is adequate space around the
unit for cooling airflow.
•
Place the unit as near to the motor as possible.
Keep the motor cables as short as possible. See
chapter 10.5 Cable Specifications
•
Ensure that the location allows for cable entry at
the bottom of the unit.
Cooling and airflow requirements
•
Ensure that top and bottom clearance for air
cooling is provided. Clearance requirement:
225 mm (9 in).
•
Consider derating for temperatures starting
between 45
°
C (113
°
F) and 50
°
C (122
°
F) and
elevation 1000 m (3300 ft) above sea level. See
the product-specific
design guide
for detailed
information.
The drive uses back-channel cooling to circulate the heat
sink cooling air. The cooling duct carries approximately
90% of the heat out of the back channel of the drive.
Redirect the back-channel air from the panel or room by
using:
•
Duct cooling. Back-channel cooling kits are
available to direct the air away from the panel
when an IP20/chassis drive is installed in a Rittal
enclosure. Use of a kit reduces the heat in the
panel and smaller door fans can be specified on
the enclosure.
•
Cooling out the back (top and base covers). The
back-channel cooling air can be ventilated out of
the room so that the heat from the back channel
is not dissipated into the control room.
Mechanical Installation
VLT® AutomationDrive FC 302
18
Danfoss A/S © 09/2018 All rights reserved.
MG34U502
4
4
Summary of Contents for VLT AutomationDrive FC 302
Page 2: ......