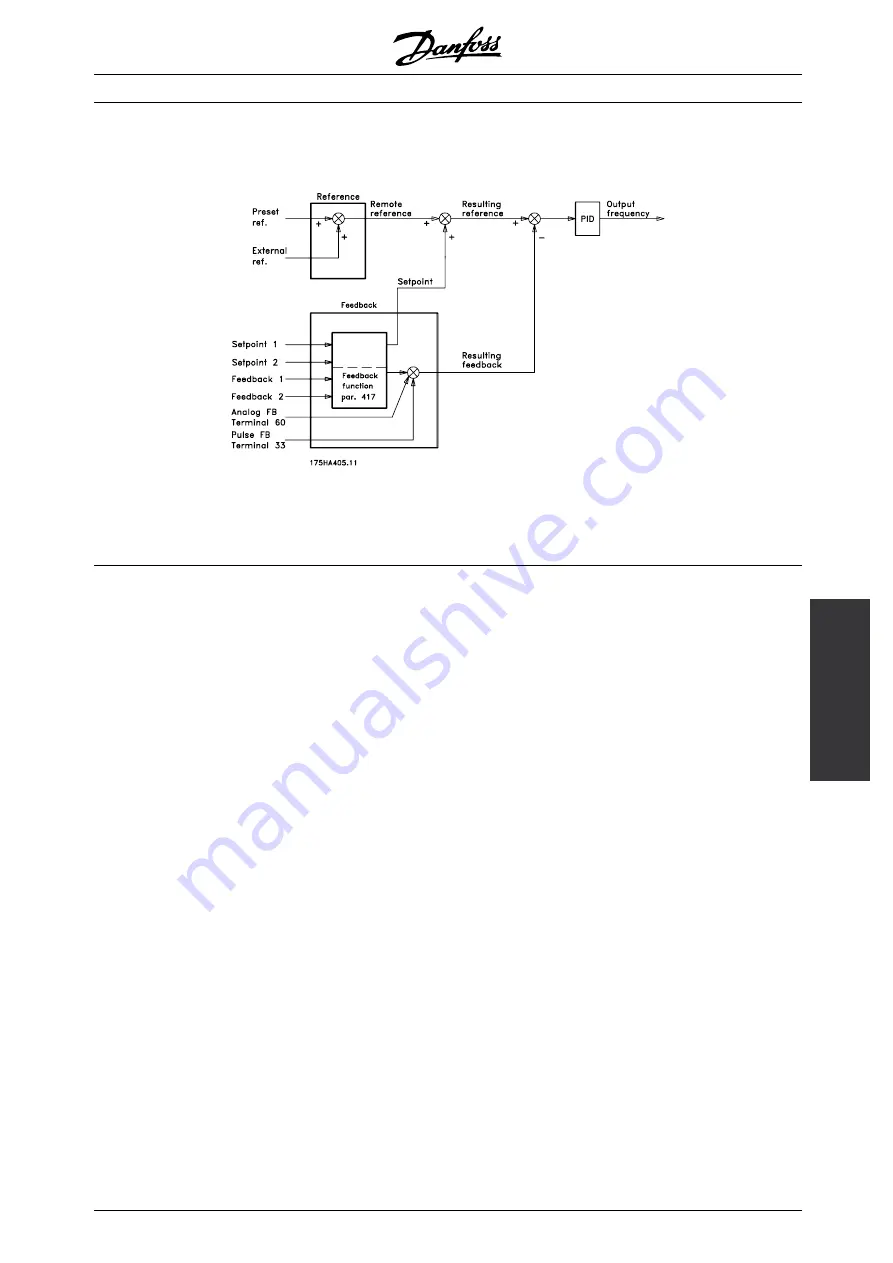
VLT
®
8000 AQUA
Programming
■
PID overview
The block diagram below shows reference and
setpoint in relation to the feedback signal.
As can be seen, the remote reference is totalled
with setpoint 1 or setpoint 2. See also
Reference
handling
. Which setpoint is to be totalled with the
remote reference depends on the selection made
in parameter 417
Feedback function
.
■
Feedback handling
The feedback handling can be seen from the
block diagram on the next page.
The block diagram shows how and by which
parameters the feedback handling can be affected.
Options as feedback signals are: voltage, current,
pulse and bus feedback signals. In zone regulation,
feedback signals must be selected as voltage inputs
(terminals 53 and 54). Please note that
Feedback 1
consists of bus feedback 1 (parameter 535) totalled
with the feedback signal value of terminal 53.
Feedback
2
consists of bus feedback 2 (parameter 536) totalled
with the feedback signal value of terminal 54.
In addition, the frequency converter has an integral
calculator capable of converting a pressure signal
into a "linear flow" feedback signal. This function is
activated in parameter 416
Feedback conversion
.
The parameters for feedback handling are active both
in closed and open loop modes. In
open loop
, the
present temperature can be displayed by connecting
a temperature transmitter to a feedback input.
In a closed loop, there are - roughly speaking -
three possibilities of using the integral PID regulator
and set-point/ feedback handling:
1. 1 setpoint and 1 feedback
2. 1 setpoint and 2 feedbacks
3. 2 Setpoints and 2 feedbacks
✭
= factory setting. () = display text [] = value for use in communication via serial communication port
MG.83.A2.02 - VLT is a registered Danfoss trademark
139