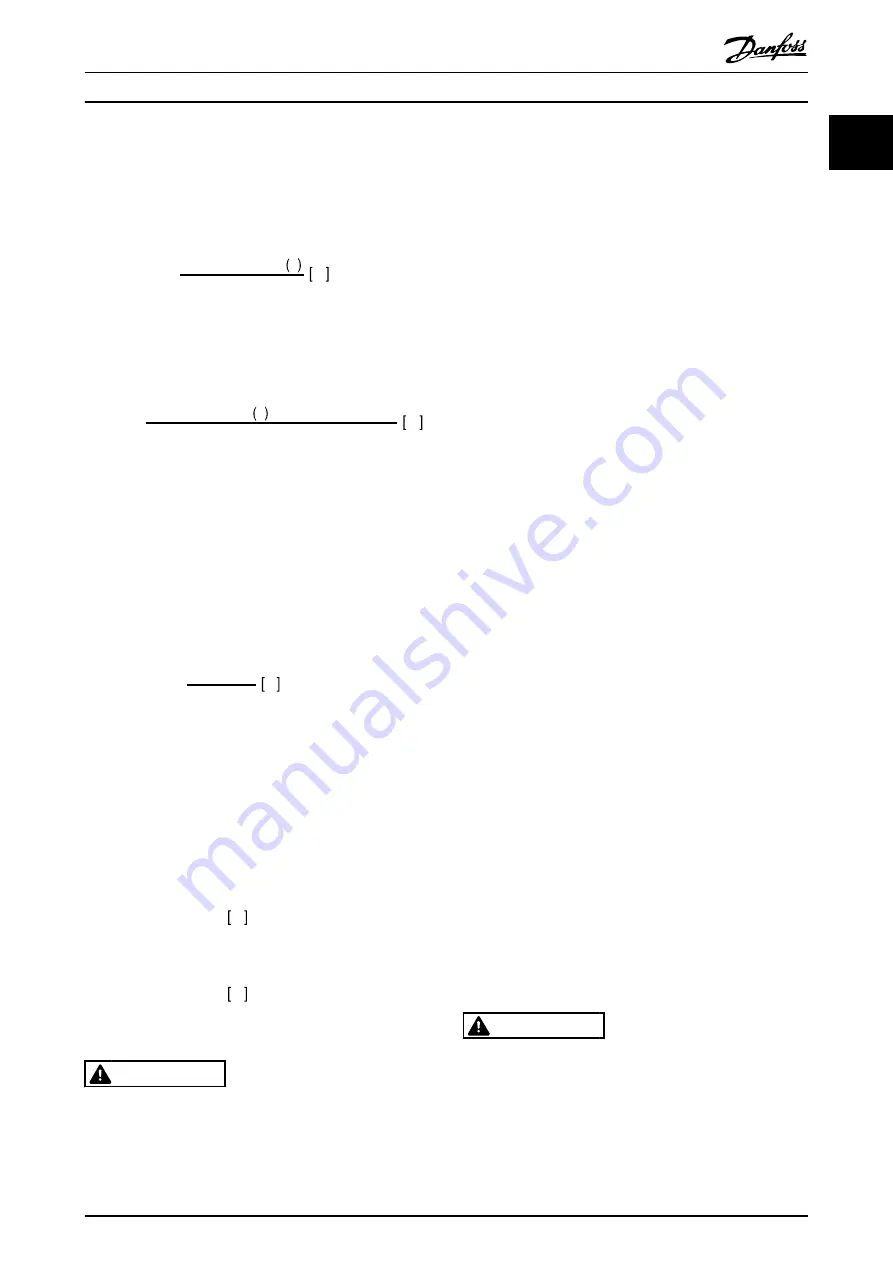
1.11.5 Calculation of Peak Power of Brake
Resistor
P
PEAK, MEC
is the peak power at which the motor brakes on
the motor shaft. It is calculated as follows:
P
PEAK, MEC
=
P
MOTOR
×
M
BR %
100
W
P
peak
is the term describing the braking power that is
applied to the brake resistor when the motor applies the
brakes. P
PEAK
is smaller than P
PEAK, MEC
, as the power is
reduced by the efficiency of the motor and the frequency
converter. The peak effect is calculated as follows:
P
PEAK
=
P
MOTOR
×
M
BR %
× η
INV
× η
MOTOR
100
W
With Danfoss' recommended brake resistor (R
REC
), the
brake resistance can generate a braking torque of 160% on
the motor shaft.
1.11.6 Calculation of Mean Power on Brake
Resistor
The mean power is determined by the period of the
process, i.e. how long the brake is in relation to the period
of the process.
Duty-cycle for braking is calculated as follows:
Duty
−
cycle
=
T
b
× 100
T
p
%
T
p
= The process time in seconds.
T
b
= The braking time in seconds.
Danfoss sells brake resistors with variable duty-cycles up to
40%. For example, with a 10% duty-cycle, brake resistors
can take up P
peak
in 10% of the process period. The
remaining 90% of the period time is spent on redirecting
surplus heat.
The mean power at 10% duty cycle can be calculated as
follows:
P
avg
=
P
peak
× 10%
W
The mean power at 40% duty cycle can be calculated as
follows:
P
avg
=
P
peak
× 40%
W
These calculations apply to intermittent braking with
period times of up to 120 s.
CAUTION
The resistor can become overheat If the period times are
longer than 120 s. This can lead to equipment damage.
Ensure the period times are less than 120 s.
1.11.7 Continuous Braking
For continuous braking, a brake resistor should be selected
in which the constant braking power does not exceed the
mean power P
AVG
of the brake resistor.
Contact the Danfoss supplier for further information.
1.11.8 DC Injection Braking
If the 3-phase winding of the stator is fed with direct
current, a stationary magnetic field is set up in the stator
bore causing a voltage to be induced in the bars of the
cage rotor as long as the rotor is in motion. Since the
electrical resistance of the rotor cage is very low, even
small induced voltages can create a high rotor current.
This current produces a strong braking effect on the bars
and hence on the rotor. As the speed drops, the frequency
of the induced voltage drops and with it the inductive
impedance. The ohmic resistance of the rotor gradually
becomes dominant and so increases the braking effect as
the speed comes down. The braking torque generated
drops steeply just before standstill and finally ceases when
there is no further movement. Direct current injection
braking is therefore not suitable for holding a load at rest.
1.11.9 AC-braking
When the motor acts as a brake, the DC-link voltage
increases because energy is fed back to the DC-link. The
principle in AC-braking is to increase the magnetisation
during the braking and thereby increasing the thermal
losses of the motor. Use
parameter 144 Gain AC brake
in
VLT 2800 to adjust the size of the generator torque that
can be applied to the motor without the intermediate
circuit voltage exceeding the warning level.
The braking torque depends on the speed. With the AC-
brake function enabled and
parameter 144 Gain AC
brake
=1,3 (factory setting), it is possible to brake with
about 50% of rated torque below 2/3 of rated speed and
with about 25% at rated speed. The function is not
working at low speed (below 1/3 of nominal motor speed).
It is only possible to run for about 30 s with
parameter 144
Gain AC brake
greater than 1.2.
The current cannot be read out from the display.
CAUTION
If the value in
parameter 144 Gain AC brake
is increased,
the motor current simultaneously increases significantly
when generator loads are applied. This could damage
the equipments. Change the parameter only it is
guaranteed during measurement that the motor current
in all operating situations never exceeds the maximum
permitted current in the motor.
Introduction to VLT 2800
Design Guide
MG27E402
Danfoss A/S © Rev. May/2014 All rights reserved.
19
1
1