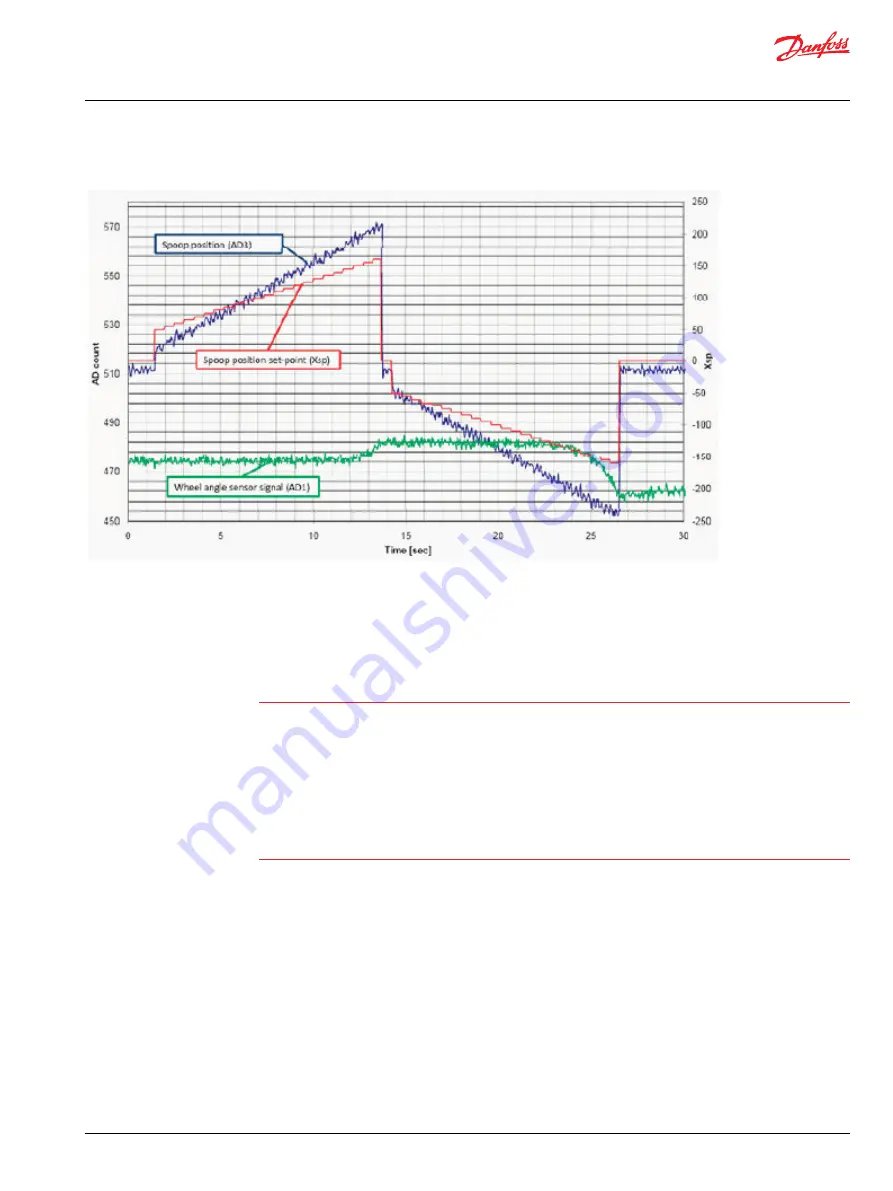
The auto-calibration progress of an EH valve with a static main spool
Explanation:
At 12 second the steering actuator begins to move. Around 14 seconds the actuator speed has exceeded
YactDiffThreshold where after the algorithm proceeds to the left direction. At 26.5 seconds the actuator
speed exceeds YactDiffThreshold and the algorithms stores the dead-band parameters and terminates.
W
Warning
Check for misaligned maximum spool stroke set-point parameter values: Previous auto-calibration
attempts with faulty command values may have shifted the parameters Xspr_1000 and Xspl_1000 to
inappropriate values which may result in asymmetric flow characteristics. Ensure that Xspr_1000 and
Xspl_1000 have values close the default values (±30) for the applied valve. See ‘Xsp maximum spool
displacement’ in table
on page 24.
Check for severe noise levels from the analogue wheel angle sensor: The wheel angle sensor AD noise
shall not exceed ±4 counts when observed via Status set 1 (see Status in PVED-CL Communication
Protocol, 11079551). High noise levels will increase the likelihood of interpreting noise as steered wheel
movement. Furthermore, repeatability may be poor.
Mapping a Steering Device
All the above mentioned functionality must be ‘activated’ by mapping or ‘Setting Present’ the individual
steering devices. This means appropriate parameters must be set to the right values, as shown in the
table below. This is done as mentioned in
Reading and Writing Parameters
on page 18.
The default settings mean a PVED-CL with power on, a CAN Steering Wheel Sensor and an analogue
joystick physically connected, will not interpret any of these inputs until the mapping is done. CAN sensor
messages are ignored and so are the voltage-inputs on the AD pins.
Operation Manual
PVED-CL Controller for Electro-Hydraulic Steering, Version 1.38
Installation
©
Danfoss | May 2016
11025583 | AQ00000216en-US0302 | 31