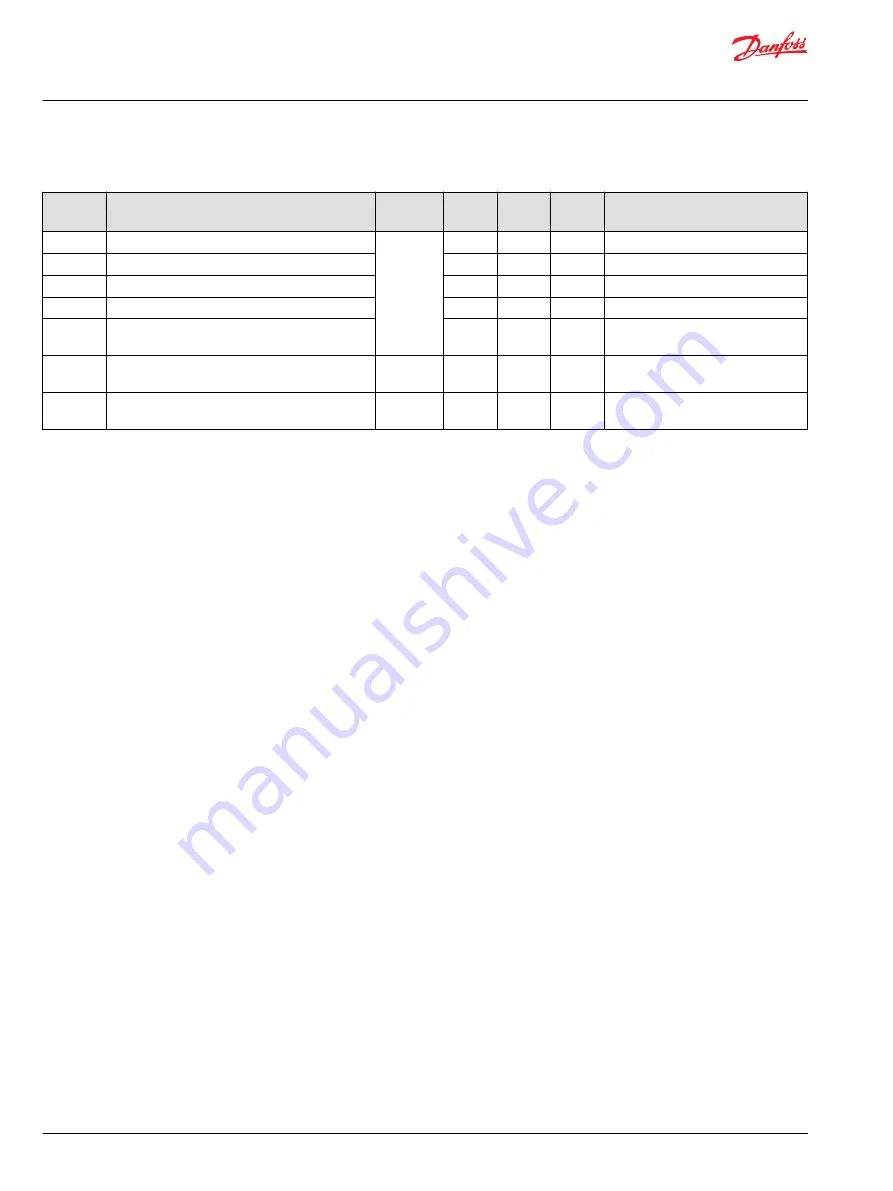
Available J1939 Diagnostic Trouble Codes (continued)
SPN
Description
Lamp
Status
FMI
CM
OC
Corresponding
PVED-CL Error Code
627
Power supply voltage below min. threshold value
Red
4
0
Yes
13030
627
Power supply voltage exceeds max. threshold value
3
0
Yes
13031
1079
Sensor supply voltage below min. threshold value
4
0
Yes
13032
1079
Sensor supply voltage exceeds max. threshold value
3
0
Yes
13033
614
Loss of main spool control or spool position
plausibility check failure
14
0
Yes
13053, 13054
615 (1)
Vehicle speed CAN sensor data plausibility check
failure
Red/Amber 14
0
Yes
13064
615 (2)
Internal PVED-CL error (= any other classified as
critical)
Red
14
0
Yes
any other classified as critical
1. This has been separated from the next row SPN 615 as this is the only case when the DTC with SPN
615 can signal the Lamp status set to Amber.
2. SPN 615 with the Lamp status set to Red indicates that other critical EHPS error has happened. The
user must retrieve an error code from the EHPS error buffer and use the table in section 2 to locate
the source of a problem.
The PVED-CL supports DM1, DM2 and DM3 according to SAE J1939-73 diagnostic protocol (see
PVED-CL
Communication Protocol Technical Information
, 11079551).
A sub-set of all possible PVED-CL fault codes are represented as standardized J1939-73 Suspect
Parameter Numbers (SPN). The sub-set is limited to interface-related faults, which are typically causing
most troubles.
AD1 and/or AD2 Short-circuit
Each of the two analog input ports are monitored for short-circuits to GND, VCC or positive battery
supply. The Failure Mode Identifier (FMI) differentiates between the two type of short-circuits. An internal
pull-down resistor on both analog input ports will pull the input level to GND if an analog input port is
left open. No analog input diagnostic is active if the analog input is not mapped.
Missing CAN Sensor Set-points
SPN 611 indicates a fault due to invalid timing or missing input signals from the sensors, most likely due
to a failing CAN sensor or cable tree fault. In this context, input signals are both CAN messages and
analog samples from sensors. However, missing analog samples or invalid timing of analog samples can
only be caused by an internal PVED-CL fault – nothing can be concluded about the analog sensors from
this SPN.
Invalid timing means that the requirements to the period that data has to be received within, has not
been met. This could again be caused by an incorrectly configured CAN sensor or a heavy CAN bus-load,
restricting the CAN sensor messages to be transmitted at their expected time.
Operation Manual
PVED-CL Controller for Electro-Hydraulic Steering, Version 1.38
Diagnostic & Troubleshooting
104 |
©
Danfoss | May 2016
11025583 | AQ00000216en-US0302