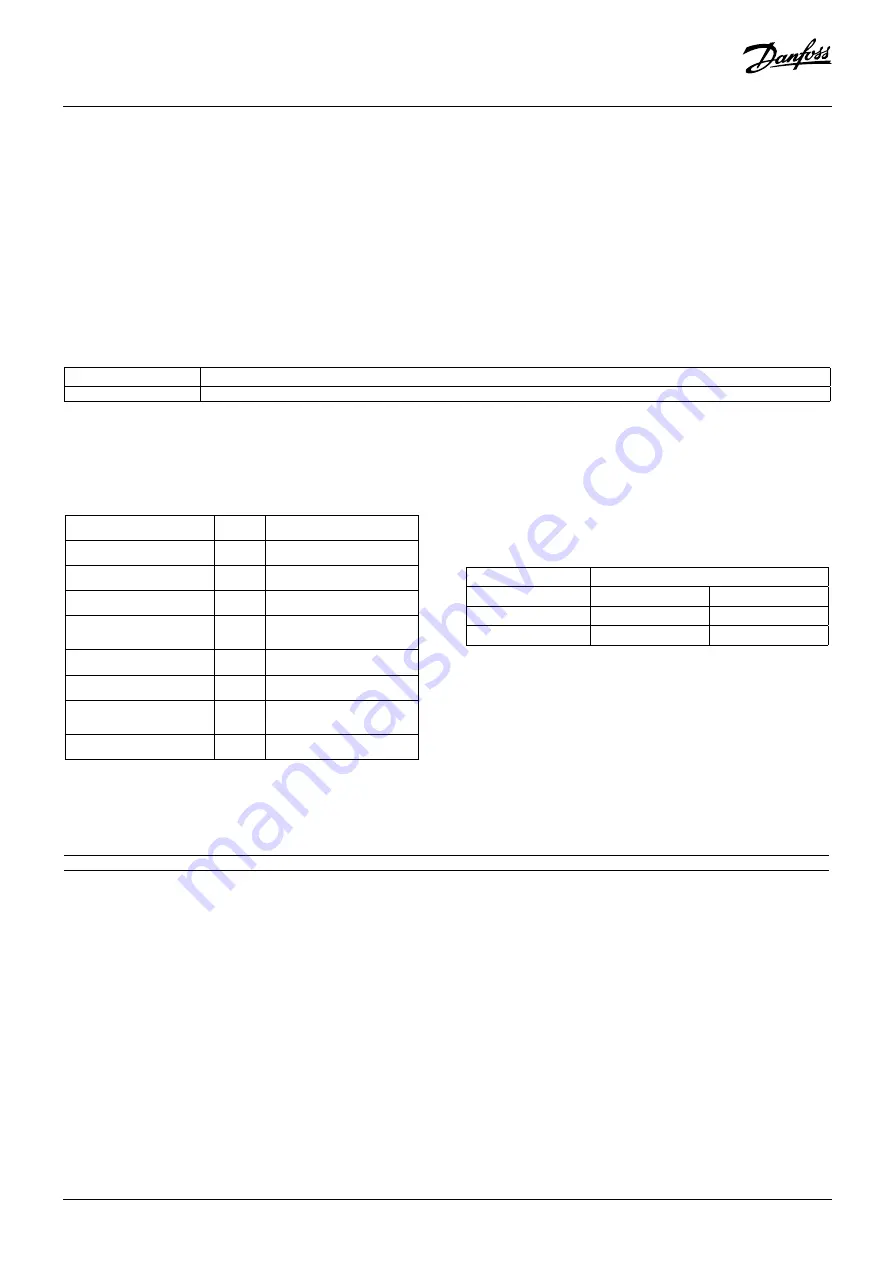
Instructions
38 | AN405821998738en-000102 - 118A5495A
© Danfoss | Climate Solutions | 2023.02 | LCA012A024
10.6. Operation start
1. Turn on the operation switch (CNS2) at the bottom of controller.
2. Turn ON the power supply of condensing unit.
3. Turn ON the operation switch of the module controller.
4. When Low pressure value
≥
Reset pressure or Outdoor air temperature < 5°C and Medium pressure value ≤ Reset pressure, the compressor starts.
10.7. Check of adequate refrigerant quantity
Calculate the refrigerant quantity according to page 17 "6.4. Refrigerant charge".
Charge the 90% of the calculated amount.
When you confirm that the following operating conditions 1, 2 are met, please add the refrigerant to the 100% of the calculated amount.
1. In the operation at 5 minutes or more after starting the compressor, the subcooling degree (*1) must be 0°C or under.
*1 Subcooling degree = Medium pressure saturation temperature “C46” – “Liquid feed pipe temperature “C15“
Calculated by 7 segment display
C46: Medium pressure saturation temperature C15: Liquid feed pipe temperature
2. The aperture of EEVSC subcooling coil electronic expansion valve must be at the upper limit value.
Type
Upper limit value (pulse) of subcooling coil electronic expansion valve 7 segment display “C23”
OP-UPAC015COP04E
470
11 – Operation
11.1. Oil check verification
Charge condensing unit oil according to “page 13,
6.1. Charge of condensing unit oil
”.
Check if adequate quantity of oil is retained, by the following refrigerating oil check operations.
Operation
1. Change the setting of compressor speed at 90 rps using 7-segment display “P19”. (For the detail of setting, see
Explanation of control on Page 25
)
2. Operate all load units to be connected (show case and unit cooler).
3. Change the dipswitch SW4-6 OFF
→
ON.
4. Operate the unit for 180 minutes in total with the compressor running at 90 rps. Elapsed operating time of compressor (90rps) is indicated at 7-segment
display. (The compressor may stop during operation depending on the condition of load unit.)
5. Should the operation of total 180 minutes be counted up without detecting by the oil level sensor any oil shortage (detection of oil shortage for 30
seconds continuously), “7-segment display” changes to “0”. In this case, it is complete the oil quantity check.
When “7-segment display” has shown “Lo1” in place of “0”, the operation is stopped because an oil shortage has been detected. In this case, turn the
dipswitch SW-6 to OFF and replenish the oil.
(Quantity of oil to be added at one time should be 500 cc as a guide.) After replenishing the oil, repeat from (1), 2 to check operation till “7-segment
display” shows “0”.
11.2. Oil return operation
When the external input harness is inserted into the external input “CN3 ” of the control board while the compressor is in operation and the rotational
speed is less than 70 rps, the oil return control is immediately executed.
Use this condensing unit within the following operation ranges.
* Regarding the capacity of low pressure side device (show case, etc.) to be connected to the condensing unit, connect the device such that its total nominal
capacity will become 50% or more of the rated capacity of the condensing unit.
Item
Unit
Specifications
Refrigerant
-
R744
Evaporation temperature
°C
-45 ~ +5
Low pressure (LP)
bar abs
8.3 ~ 30.5
Suction gas temperature(Ts)
°C
Evaporating
tempe 40°C
Discharge temperature(Td)
°C
125 or under
Ambient temperature
°C
-20 ~ +43
Power supply voltage
-
Within ±10% of rated voltage
(380/400/415 V)
Voltage unbalance rate
-
Within ±2% of rated voltage
(Continuous rating)
Operation range
Note:
1. Provide sufficient insulations on liquid feed piping and suction gas piping. (Refer
to the insulation (*) thickness in the following table.)
Type
OP-UPAC015COP04E
Kind of pipe
Liquid feed
Suction
For cooling
20mm
30mm
For freezing
30mm
40mm
Note: Where the thermal conductivity of insulator is 0.035 W/m-K, if the
liquid feed pipe and the suction gas pipe touch each other, it could cause an
overheat as a result of heat exchange between these pipes. Separate these
pipes effectively.
2. Do not use the unit in corrosive atmosphere.
3. Arrange at site such that the degree of overheat of suction gas will fall within a
range of 5 deg to 40 deg.