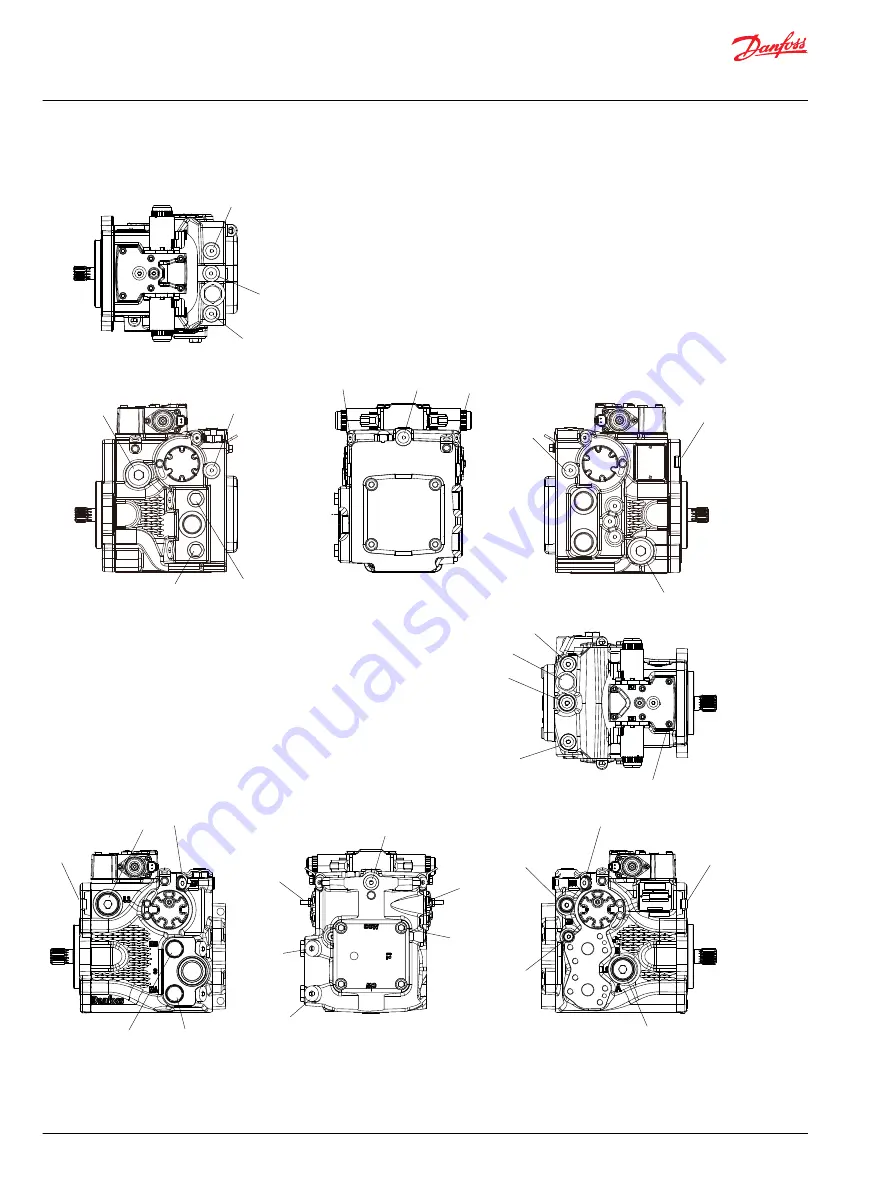
MP1 fastener size and torque
G060
G020
G025
G065
G070
G075
G010
G030
G040
G035
K300
D250
G045
G015
E085
E090
N100
M100
V100
H130
H130
H130
G060
G010
G020
G015
G025
G070
G075
G010
G035
G030
G040
G065
38/45
28/32
Service Manual
MP1
Fastener size and torque chart
64 |
©
Danfoss | April 2019
AX00000244en-000201