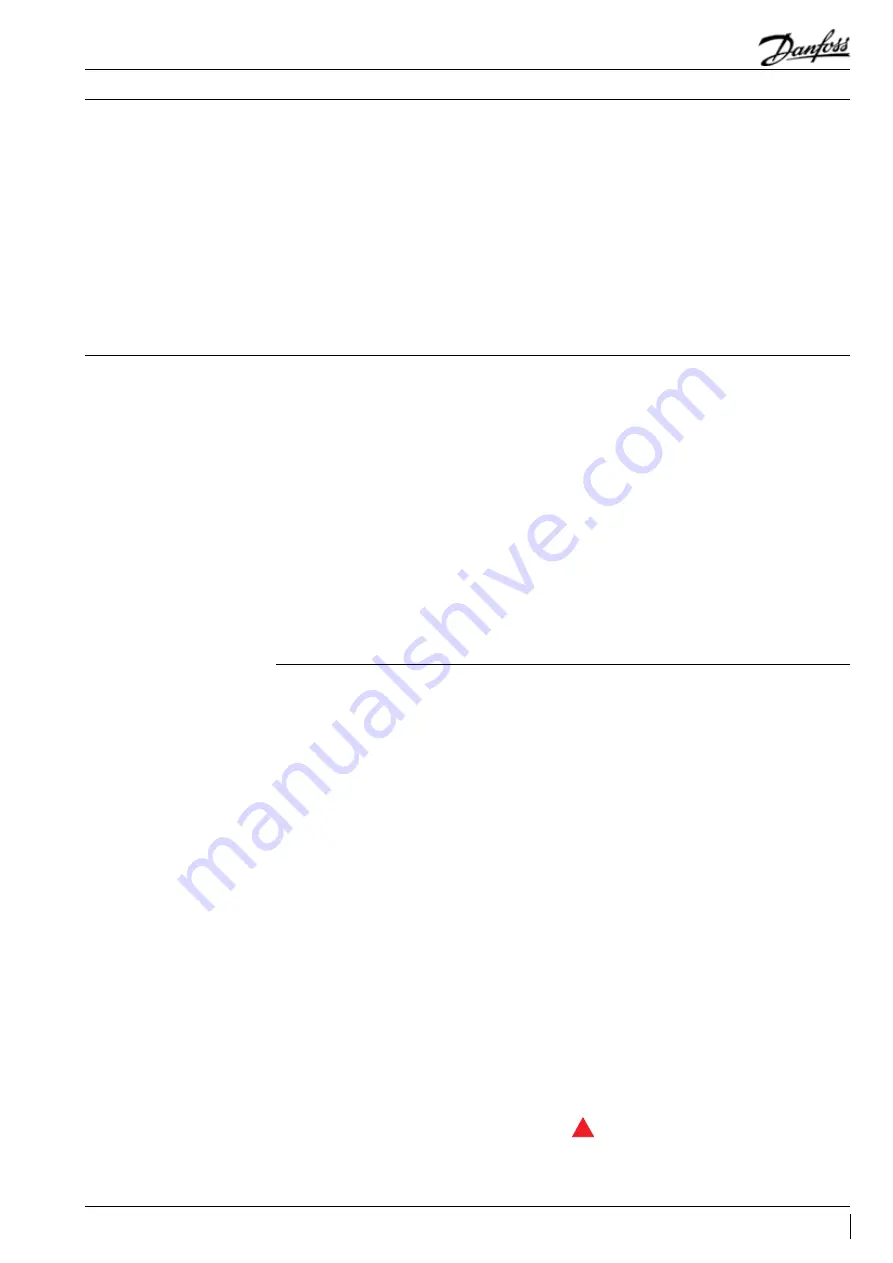
© Danfoss | Climate Solutions | 2022.03
charge as well as the gas velocity in the suction
line. Depending on the operating conditions it
may happen that the recommended connections
of the accumulator are one size smaller than the
suction line.
Selection of a suction line accumulator should
be made on the basis of the following three
capabilities:
1. The accumulator should have an adequate
liquid-holding capacity that can vary with the
system. Normally this should not be less than
50% of the system charge. If possible, this value
should be checked based on actual tests.
2. The accumulator should perform without
adding excessive pressure drop to the system.
3. An accumulator should have the capability of
returning oil at the proper rate and under a range
of load conditions.
Guideline of suction accumulator needs to be
respected in making a selection.
Low ambient application
Low ambient operations
It is recommended that the unit be tested and
monitored at minimum load and low ambient
conditions as well. The following considerations
should be taken into account to ensure proper
system operating characteristics.
The expansion device should be sized to ensure
proper control of the refrigerant flow into the
evaporator. An oversized valve may result in
erratic control. This consideration is especially
important in manifolded units where low load
conditions may require the frequent cycling of
compressors. This can lead to liquid refrigerant
entering the compressor if the expansion valve
does not provide stable refrigerant super-heat
control under varying loads.
The superheat setting of the expansion device
should be sufficient to ensure proper superheat
levels during low loading periods. A minimum of
5 K stable superheat is required.
Head pressure control under low ambient
conditions:
Several possible solutions are
available to prevent the risk of compressor to
vacuum and low pressure differential between
the suction and discharge pressures.
In air-cooled machines, cycling the fans with
a head pressure controller will ensure that the
fans remain off until the condensing pressure
has reached a satisfactory level. Variable speed
fans can also be used to control the condensing
pressure. In water-cooled units, the same can be
performed using a water regulator valve that is
also operated by head pressure, thereby ensuring
that the water valve does not open until the
condensing pressure reaches a satisfactory level.
The minimum condensing pressure must be
set at the minimum saturated condensing
temperature shown in the application envelopes.
Under very low ambient conditions, in which
testing has revealed that the above procedures
might not ensure satisfactory condensing and
suction pressures, the use of a head pressure
control valve is recommended. Note: This
solution requires extra refrigerant charge, which
can introduce other problems. A non-return
valve in the discharge line is recommended and
special care should be taken when designing the
discharge line.
R
For MLM/MLZ090-130-160-200-240, non-
return valve is mandatory.
For further information, please contact Danfoss.
Low ambient start-up
Under cold ambient conditions (<0°C), upon
start-up the pressure in the condenser may be so
low that a sufficient pressure differential across
the expansion device cannot be developed to
properly feed the evaporator.
As a result, the compressor may go into a deep
vacuum, which can lead to compressor failure
due to internal arcing and instability in the
scroll wraps. Under no circumstances should
the compressor be allowed to operate under
vacuum. The low-pressure control must be set in
accordance with the table in the section ”high
and low pressure protection” in order to prevent
this from happening.
Early feeding of the evaporator and management
of the discharge pressure could help to attenuate
these effects.
Low pressure differentials can also cause the
expansion device to “hunt” erratically, which
might cause surging conditions within the
evaporator, with liquid spillover into the
compressor. This effect is most pronounced
during low load conditions, which frequently
occur during low ambient conditions.
Specific application recommendations
31
AB243586442698en-000601
Application Guidelines
Single compressors