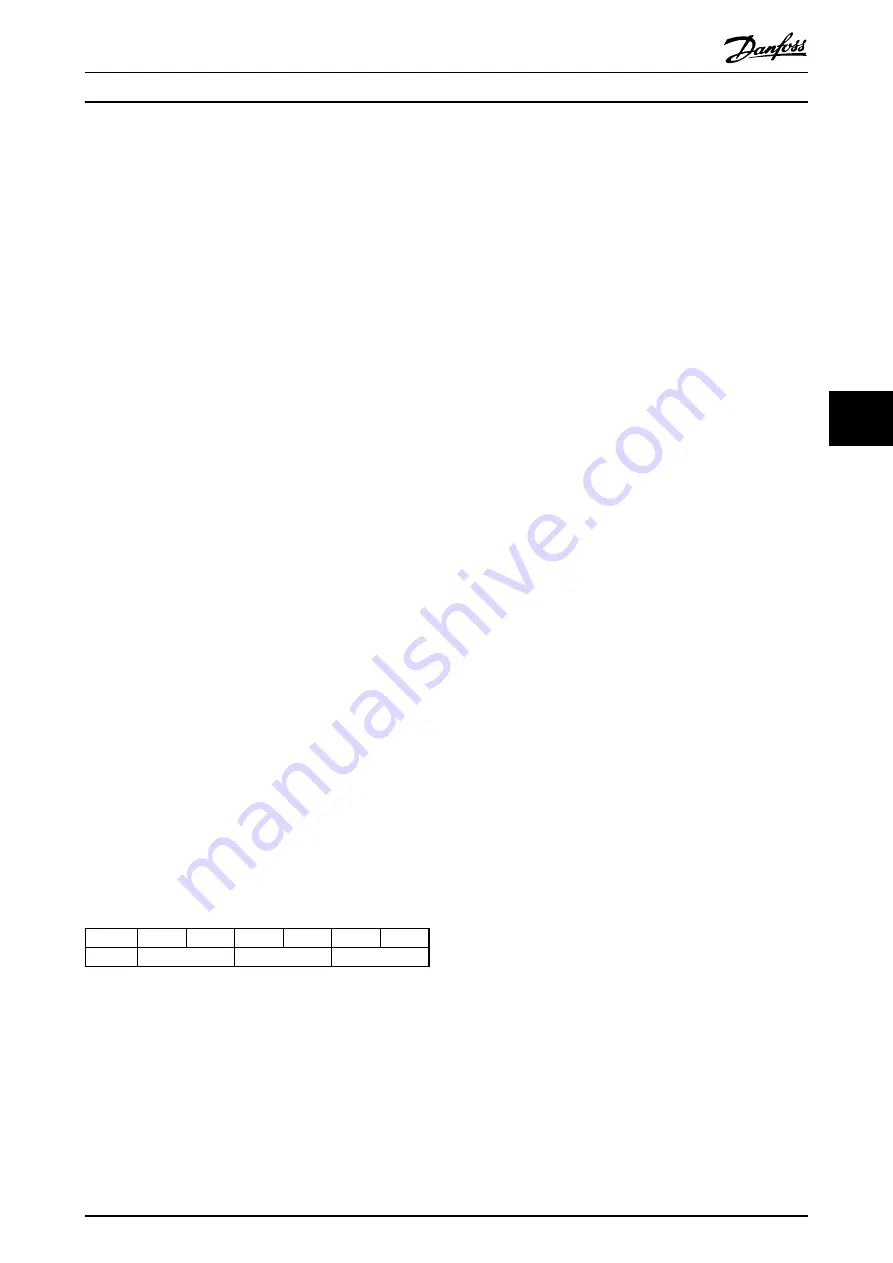
6.2.4 CAN-ID Setting
The
General.BaseCanId
and
General.DefaultCanId
are preset
to 100. All the settings can also be read from the object
dictionary.
There are several ways to set/change the CAN-ID. The
easiest way is setting via the BCD switch.
BCD switch is set to 0
•
The CAN-ID specified as
General.DefaultCanId
on
the SD card will be used.
•
The ISD ID distribution protocol can be used to
give another ID to the box. Note that the ID will
be stored on the SD card as the new
General.DefaultCanId
BCD switch is set to between 1 and 9
•
The CAN-ID is calculated by
General.BaseCanId
+
the value of the BCD switch.
The message for the ID setting over CAN bus is shown in
the table below. Note that the first 4 bytes have to be 0,
otherwise the encoder box ignores the ID setting message.
This is also the case if the BCD switch is not set to 0. After
this message is sent, the new CAN-ID will start flashing on
the encoder box display. Press the <SET> button on the
encoder box to accept the new ID. The encoder box will
only leave this ID setting mode following the acceptance
of the new ID or after an NMT reset.
Note that the other ISD servo system components will also
be in ID setting mode after this message is sent, so an
“NMT reset communication” message has to be sent to
release all devices from this mode.
Note that whilst in ID setting mode, it is not possible to
communicate with the device.
COB-ID
Byte 0
Byte 1
Byte 2
Byte 3
Byte 4
Byte 5
0x7F2
0
0
new CAN-ID
Table 6.1 ISD ID Setting Message
6.3 Switching the Encoder Box on
Ensure that the SD card is inserted and that the encoder
box parameter file (MPARAM.dat) exists before switching
on the encoder box. If not, the encoder box cannot be
started and error code “Err2” is shown on the 7-segment
display.
This error can only be reset by inserting an SD card (with a
valid parameter file) and carrying out a re-start (removing
and replacing the mains supply plug).
Furthermore, the CAN bus and the encoder must be
connected to the encoder box correctly.
For the servo system to function correctly, all components
must be wired correctly. Read the operating instructions of
the other ISD components carefully.
Switching on (booting up)
The encoder box parameter file (MPARAM.dat) contains the
parameter list and is automatically read after the encoder
box is switched on.
The pre-configuration of the defined objects for the
chosen encoder takes place. During this initialisation
phase, the LED "Run / Err." flashes green.
CAUTION
Do not remove or replace the SD card during operation,
otherwise the contents of the SD card could be destroyed.
Switch the encoder box off and wait 10 seconds before
removing the SD card.
Commissioning
VLT
®
ISD Encoder Box Operating Instructions
MG75F102 - VLT
®
is a registered Danfoss trademark
21
6
6