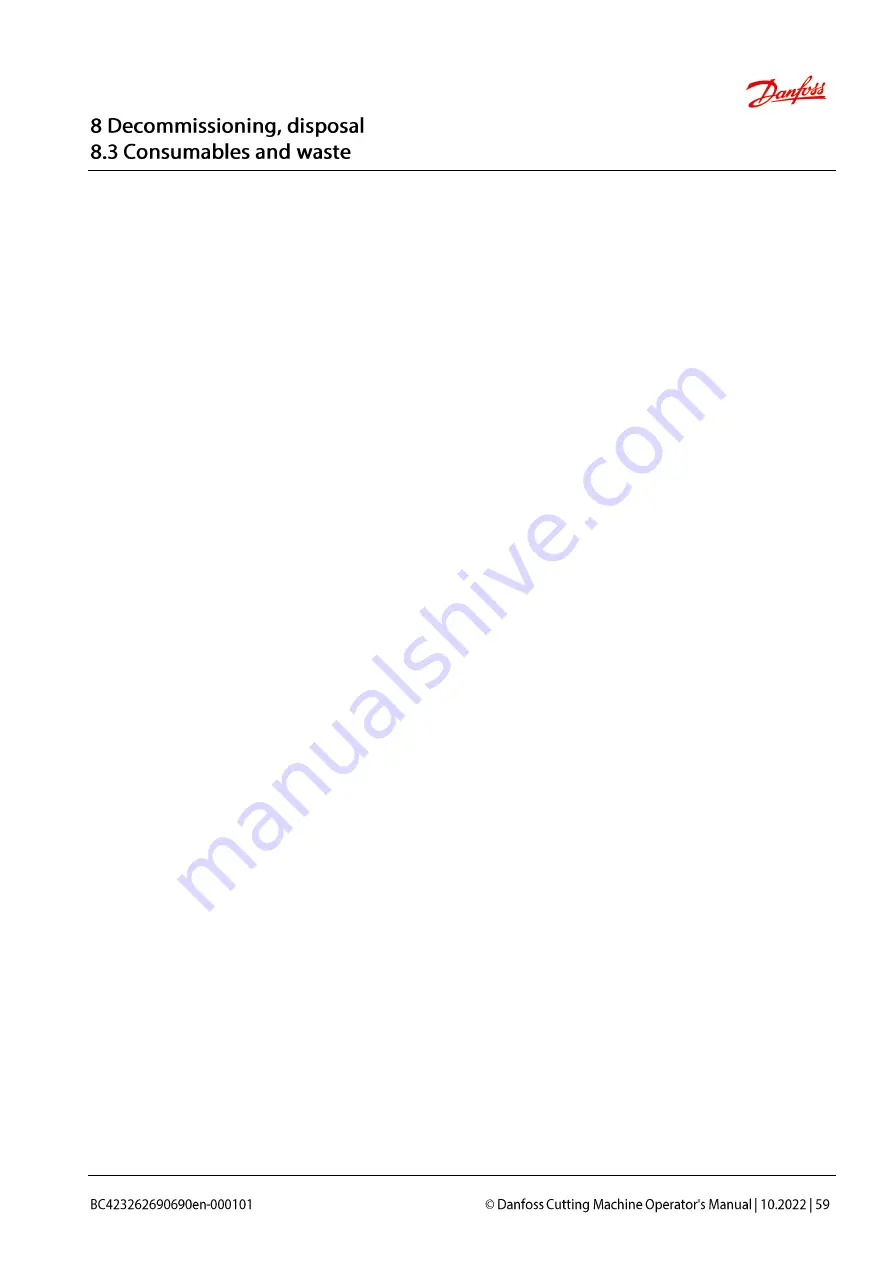
As regards disposal, the applicable national environmental protection
and waste disposal regulations have to be complied with.
8.3 Consumables and waste
Observe applicable national environmental protection and waste dis-
posal regulations.
Return consumables, e.g. oils, greases, test media, to supplier - they
are hazardous waste. Also observe the information given on the
safety data sheet.