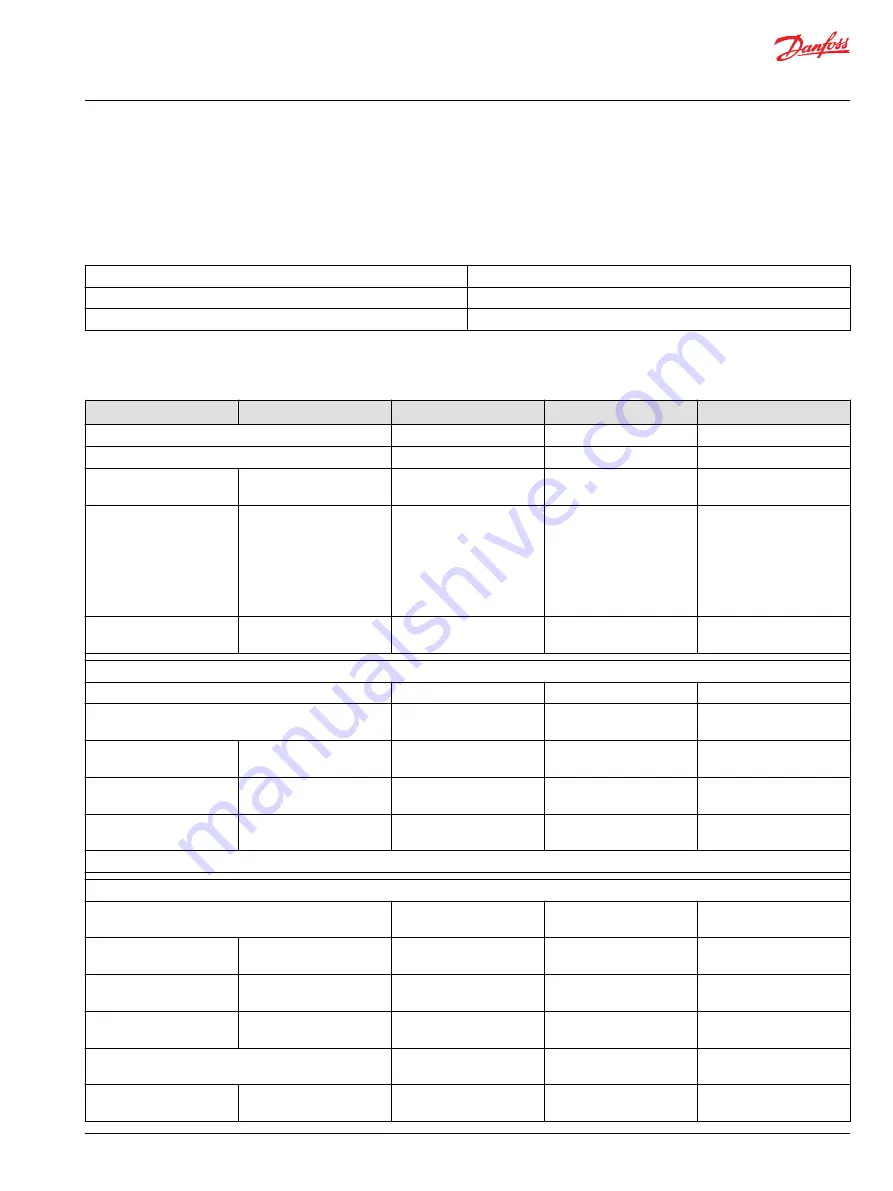
Electric machine installation checklist
Date:
Electric machine and customer information
Customer:
Electric machine type (from the rating plate):
Customer reference:
Electric machine serial number:
Service reference:
Date installed:
N.A = Procedure not applicable PASS = Procedure passed FAIL = Procedure failed
Installation checklist
Approval
N.A
PASS
FAIL
General
Electric machine type is correct
☐
☐
☐
Electric machine is
undamaged
☐
☐
☐
Insulation resistance check
(Reference value of 150 MΩ
should not be exceeded at
reference ambient
temperature 25°C (measured
with 500 V
DC
/ 1 min
Megger))
>150MΩ
☐
☐
☐
Environmental conditions as
specified (see data sheet)
☐
☐
☐
Mechanical installation
Supporting structure as required
☐
☐
☐
Shaft alignment as specified (see chapter Shaft alignment
and load).
☐
☐
☐
D-end attachment bolt
tightening torque
40 Nm
☐
☐
☐
N-end attachment bolt
tightening torque
30 Nm
☐
☐
☐
Cooling circuit connected
and coolant flowing
☐
☐
☐
Used coolant:
Power connections
Cable gland assembly as specified (cable gland to cables)
with correct cable diameter
☐
☐
☐
Cable lug air cap (to metallic
structures)
≥10 mm
☐
☐
☐
Cable gland tightening
torque (to the box)
15 Nm
☐
☐
☐
Cable lug tightening torque
(to the busbar)
13 Nm
☐
☐
☐
The phase connections order is correct (U, V, W -> L1, L2,
L3)
☐
☐
☐
Connection box cover bolts
tightening torque
4 Nm
☐
☐
☐
User Guide
EM-PMI375
Storage, installation and maintenance checklists
©
Danfoss | November 2021
BC265856307805en-000202 | 77