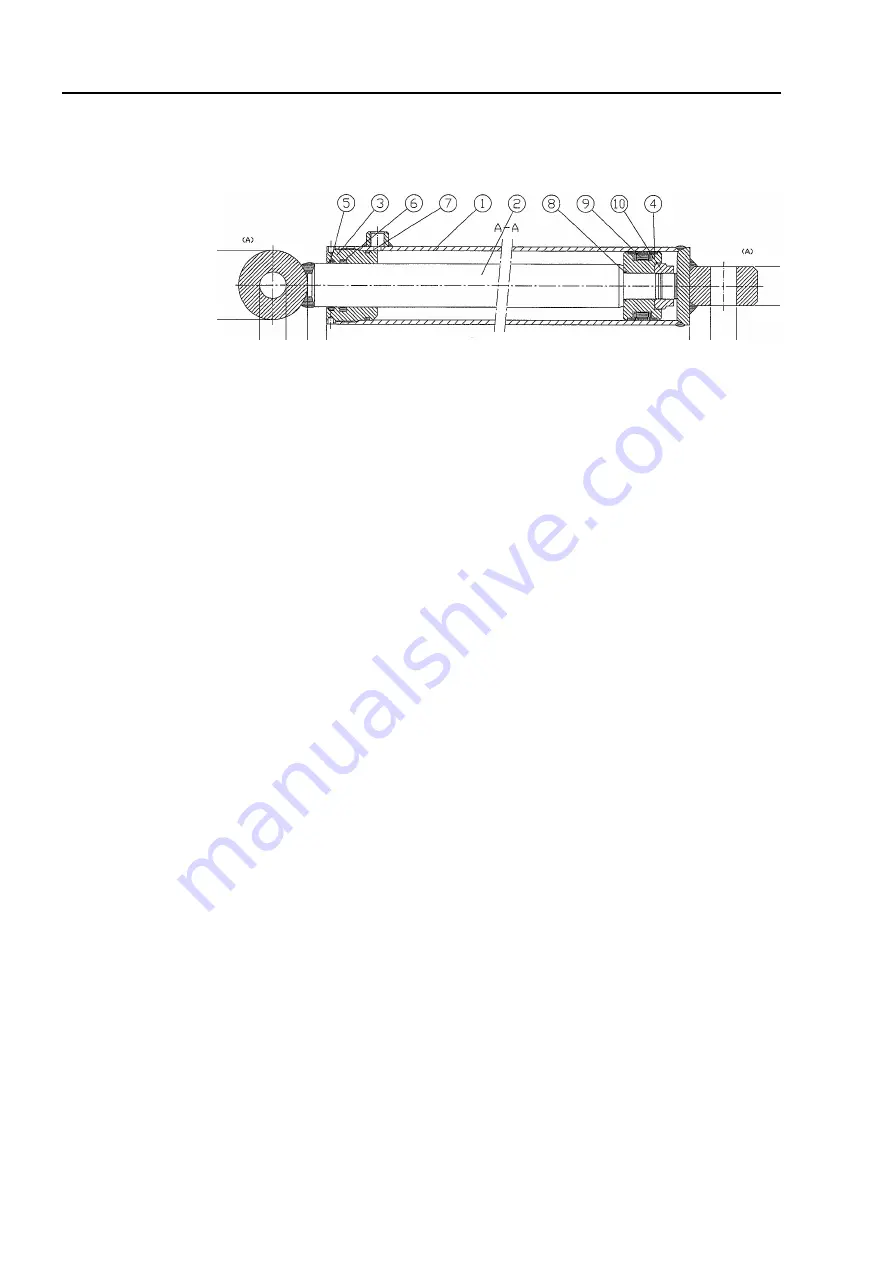
POWERROLL
Side 28
Replacing gaskets on raise/lower cylinder
Fig. 21
1.
Drain oil from cylinder by moving ram carefully backwards and forwards.
2.
Extend ram to centre position. Unscrew upper part (pos. 3) from cylinder tube
(pos. 1). Use special tool to remove upper part. If upper part is stuck, heat front
of upper part. When upper part is detached from cylinder tube, pull ram up to-
wards upper part and remove completely from cylinder tube (pos. 1).
3.
Remove lock nut (pos. 10) retaining collar shoe (pos. 4).
4.
Remove collar shoe (pos. 4) from ram, (pos. 2).
5.
Remove upper part (pos. 3) from ram, (pos. 2).
6.
Remove gaskets in upper part (pos. 5+6+7+8+9) along with collar shoe.
7.
Clean all parts and check for particles etc. Check for rust around scraper ring
(pos. 5) in upper part. If detected, remove thoroughly.
Assembly
1.
Fit new gaskets (pos. 5+6+7+8+9) in upper part, plus collar shoe.
2.
Lubricate thread in upper part (pos. 3) and cylinder tube (pos. 1) with oil.
3.
Remove upper part (pos. 3) on ram shaft.
4.
Remove collar shoe (pos. 4) and screw on lock nut,
secure with Loctite
. Ensure
that thread is absolutely clean and free of oil or other impurities before applying
Loctite.
Do not fill with oil for 12 hours after use of Loctite.
5.
Lubricate outer collar shoe gasket in contact with cylinder tube and inside of
cylinder tube with oil, push ram into centre position.
6.
Fit upper part onto cylinder tube and tighten.
7.
For fitting cyl
inder see ”
Replacing raise/lower cylinder
Summary of Contents for POWERROLL 1430
Page 1: ...POWERROLL ENG 1430 1530 1630 1830 Serial no 100 XXX ...
Page 2: ......
Page 34: ...POWERROLL Side 34 Spare parts ...