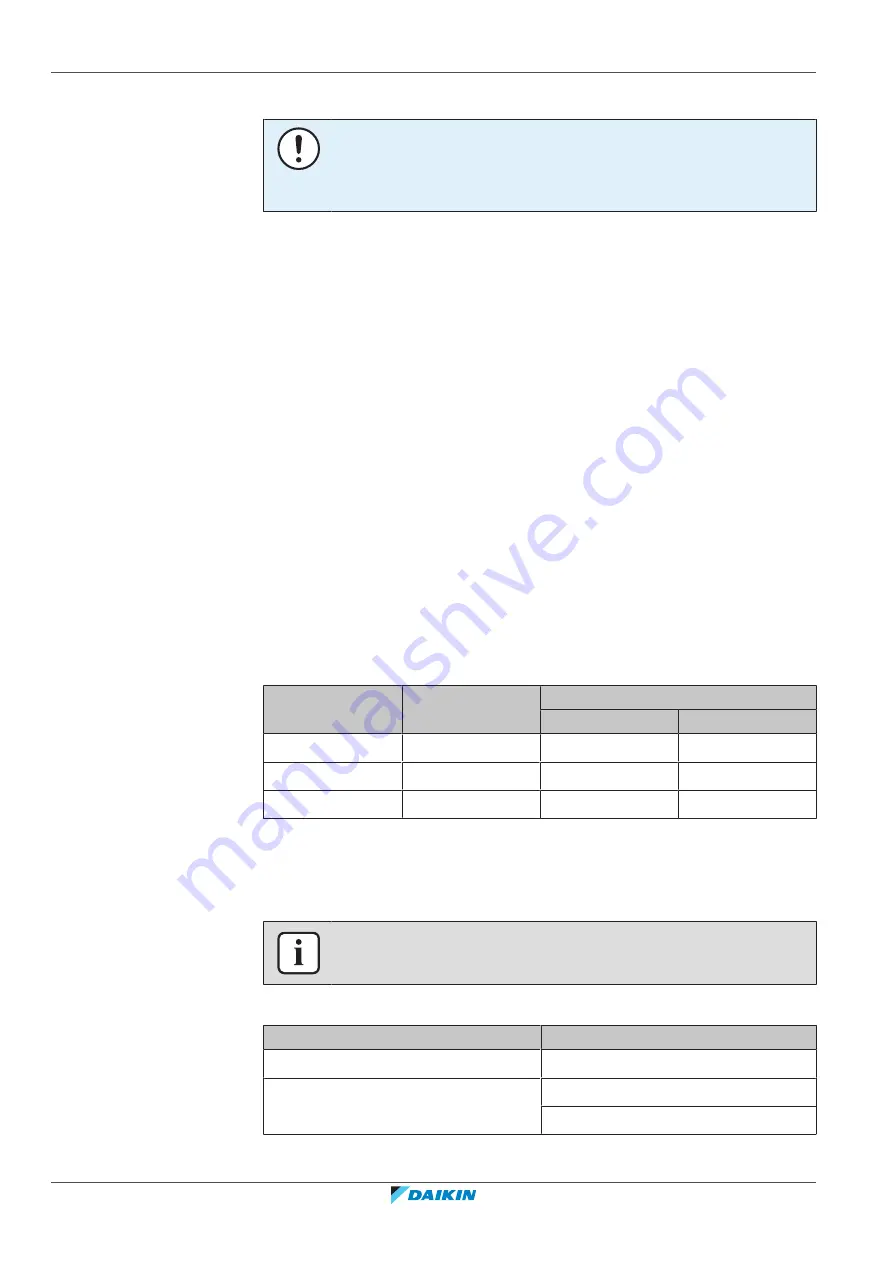
14
|
About the units and options
Installer and user reference guide
56
R R8T7V1B
VRV IV heat pump for indoor installation
4P499898-1B – 2021.12
14.5.1 About combining units and options
NOTICE
To be sure your system setup (compressor unit+heat exchanger unit+indoor unit(s))
will work, you have to consult the latest technical engineering data for the VRV IV
heat pump for indoor installation.
The VRV IV heat pump for indoor installation can be combined with several types
of indoor units and is intended for R410A use only.
For an overview which units are available you can consult the product catalogue
for the VRV IV heat pump for indoor installation.
An overview is given indicating the allowed combinations of indoor units,
compressor units and heat exchanger units. Not all combinations are allowed. They
are subject to rules mentioned in the technical engineering data.
14.5.2 Possible combinations of indoor units
In general following type of indoor units can be connected to a VRV IV heat pump
for indoor installation. The list is non-exhaustive and is depending on the
combination of compressor unit, heat exchanger unit and indoor unit models.
▪
VRV direct expansion (DX) indoor units (air to air applications).
▪
AHU (air-to-air applications): EKEXV-kit+EKEQM-box required, depending on the
application.
▪
Comfort air curtain (air-to-air applications): CYV (Biddle) series.
Connection ratio requirements.
When selecting indoor units, the connection ratio
must comply with the following requirements. For more information, see the
technical engineering data.
Other combinations than those mentioned in the table are not allowed.
Indoor units
Total CR
(a)
CR per type
(b)
VRV DX
AHU
VRV DX
50~130%
50~130%
—
VRV DX + AHU
50~110%
50~110%
0~60%
AHU
90~110%
—
90~110%
(a)
Total CR = Total indoor unit capacity connection ratio
(b)
CR per type = Allowable capacity connection ratio per indoor unit type
14.5.3 Possible options for the compressor unit and heat exchanger unit
INFORMATION
Refer to the technical engineering data for the latest option names.
Refrigerant branching kit
Description
Model name
Refnet header
KHRQ22M29H
Refnet joint
KHRQ22M20TA
KHRQ22M29T9