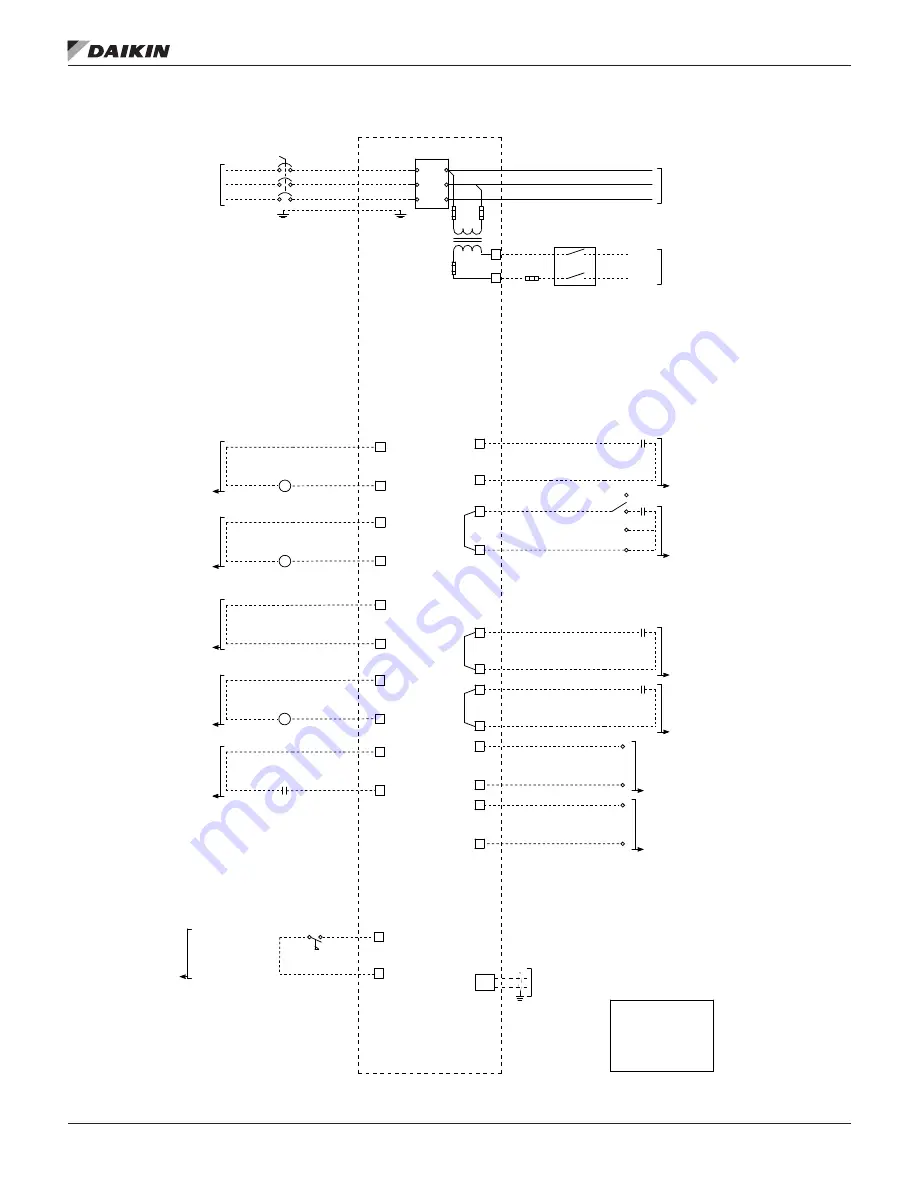
IOM 1242-8 • PATHFINDER
®
MODEL AWV CHILLERS
24 www.DaikinApplied.com
Installation and Application Considerations
Figure 46: Field Wiring Diagram - Single Point Power
910170645_1RC
4-20 mA
DEMAND LIMIT
(BY OTHERS)
4-20 mA
SETPOINT OVERRIDE
(BY OTHERS)
_
_
+
+
EA1
** USE DRY CONTACTS ONLY, SEE NOTE 2
IF EXTERNAL ALARM IS USED, REMOVE
LEAD 402 BETWEEN M5 TERMINALS 5 & 15
TIME
CLOCK
OFF
MANUAL
ON
AUTO
OPTIONAL
FIELD SUPPLIED
CONTROL POWER
OPEN Q12 IF SUPPLY IS SEPARATE 120 VAC SOURCE
DISCONNECT
(BY OTHERS)
N
120 VAC
115
VAC
F120
T1
F120
37
M5
REMOTE
SWITCH
(BY OTHERS)
M5
M5
M5
M5
M5
M5
M5
** USE DRY CONTACTS ONLY, SEE NOTE 2
IF REMOTE SWITCH IS USED,
REMOVE MECHANICAL JUMPER
BETWEEN M5 TERMIONALS 58 & 59.
38
35
5
58
36
15
59
EXTERNAL
ALARM
N
N
N
120 VAC
120 VAC
120 VAC
EVAP. WATER
PUMP RELAY No. 2
(BY OTHERS)
M5
MQ
M5
MQ
M5
MQ
CHWR2
(BY OTHERS)
EVAP. WATER PUMP RELAY
120VAC @ 0.25AMP MAX
26
49
CHWR1
(BY OTHERS)
EVAP. WATER PUMP RELAY
120VAC @ 0.25AMP MAX
28
17
17
17
ALARM OUTPUT
EVAP. WATER
PUMP RELAY No. 1
(BY OTHERS)
3 PHASE
POWER
SOURCE
POWER BLOCK
OR
DISCONNECT SWITCH
MODE SWITCH
** USE DRY CONTACTS ONLY, SEE NOTE 2
IF MODE SWITCH IS USED, REMOVE
LEAD 322 BETWEEN M5-21 AND MS-10.
57
21
M5
M5
TO
COMPRESSOR(S)
AND FAN MOTORS
OR CIRCUIT 1
CIRCUIT BREAKER
(BY OTHERS)
12
MQ
MQ
17
EARTH
GROUND
(BY OTHERS)
FUSE
20A for 2KVA
30A for 3KVA
Q12
(BY OTHERS)
120VAC @ 0.25AMP MAX
NOTE:
1) ALL FIELD WIRING TO BE
INSTALLED AS NEC CLASS 1 WIRING
SYSTEM WITH CONDUCTOR RATED
600 VOLTS.
2)**=USE "DRY CONTACTS" ONLY.
DO NOT SUPPLY FIELD POWER TO
THIS CIRCUIT.
3)DO NOT SUPPLY FIELD POWER TO
24VAC OR 120VAC CONTROL CIRCUITS.
23
M5
M5
8
NOTE: For Factory Supplied Thermal
Dispersion Flow Switch wiring, see wiring
instruction in Kit.
FLow Switch Contacts
M
DI2
**USE DRY CONTACS ONLY
SEE NOTE 2
TO/FROM BAS
(CUSTOMER
CONNECTION)
CLA
CLB
CONNECT TO GROUND
AT ONE END ONLY.
BACKUP
CHILLER
62
61
M5
M5
BC1
FOR RAPID
RESTORE OPTION
ONLY
** USE DRY CONTACTS ONLY, SEE NOTE 2
T1
L3
T3
L1
PANEL
T2
L2
LON
GND
(833)
(828)
(737)
(830)
(718)
(721)
(720)
(735)
(735)
(856)
(858)
N
120 VAC
M5
MQ
44
17
WSESR
(BY OTHERS)
N
120 VAC
M5
MQ
45
11
WATER SIDE
ECONOMIZER
STATUS RELAY
WATER SIDE
ECONOMIZER ENABLE
(BY OTHERS)
* SEE NOTE 2
*120VAC CIRCUIT
(933)
(947)
IF WATER SIDE ECONOMIZER IS
USED, REMOVE LEAD 552 AND
INSTALL SWITCH BETWEEN M5-45
AND MQ-11