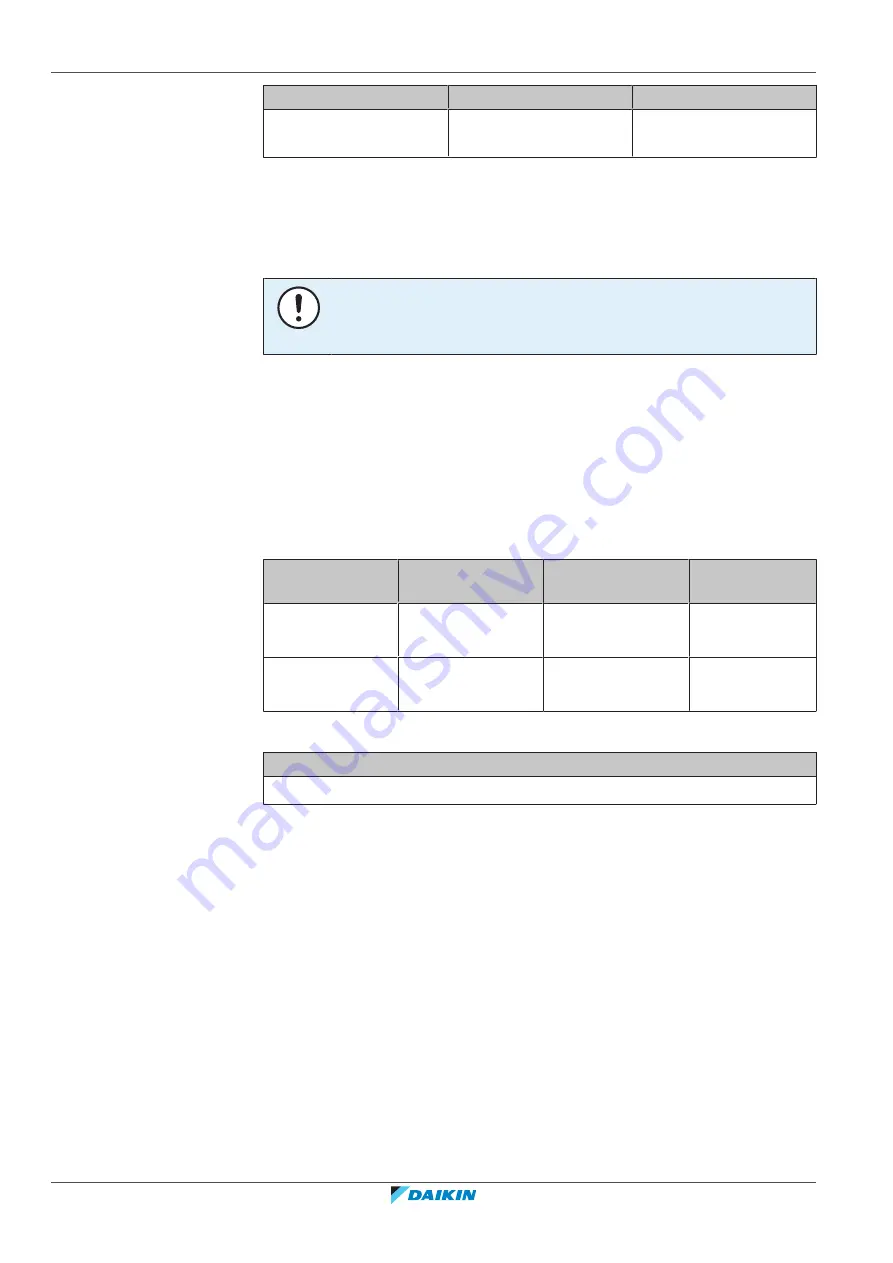
17
|
Electrical installation
Installer and user reference guide
92
LRYELRNUN5A7Y1
CO₂ Conveni-Pack outdoor unit
4P605460-1 – 2020.08
Terminal
Screw size
Tightening torque (N•m)
X1M (A1P): DIII
transmission wiring
M3.5
0.80~0.96
17.5 Specifications of standard wiring components
Power supply
NOTICE
When using residual current operated circuit breakers, be sure to use a high-speed
type 300 mA rated residual operating current.
The power supply must be protected with the required safety devices, i.e. a main
switch, a slow blow fuse on each phase and an earth leakage protector in
accordance with the applicable legislation.
Selection and sizing of the wiring should be done in accordance with the applicable
legislation based on the information mentioned in the table below.
Make sure that a separate power supply circuit is provided for this unit and that all
electrical work is carried out by qualified personnel according to local laws and
regulations and this manual. An insufficient power supply capacity or improper
electrical construction may lead to electric shocks or fire.
Model
Minimum circuit
ampacity
Recommended
fuses
Power supply
LRYEN10A7Y1
33 A
45 A
3N~ 50 Hz
380-415 V
LRNUN5A7Y1
16 A
25 A
3N~ 50 Hz
380-415 V
DIII transmission wiring
Transmission wiring specification and limits
(a)
Vinyl cords with 0.75 to 1.25 mm² sheath or cables (2‑core wires)
(a)
If the total transmission wiring exceeds these limits, communication errors might occur.
Remote switches
See details in:
▪
"17.6.1 Low voltage wiring – Outdoor unit"
▪
"17.7.1 Low voltage wiring – Capacity up unit"
Output signals
See details in:
▪
"17.6.2 High voltage wiring – Outdoor unit"
▪