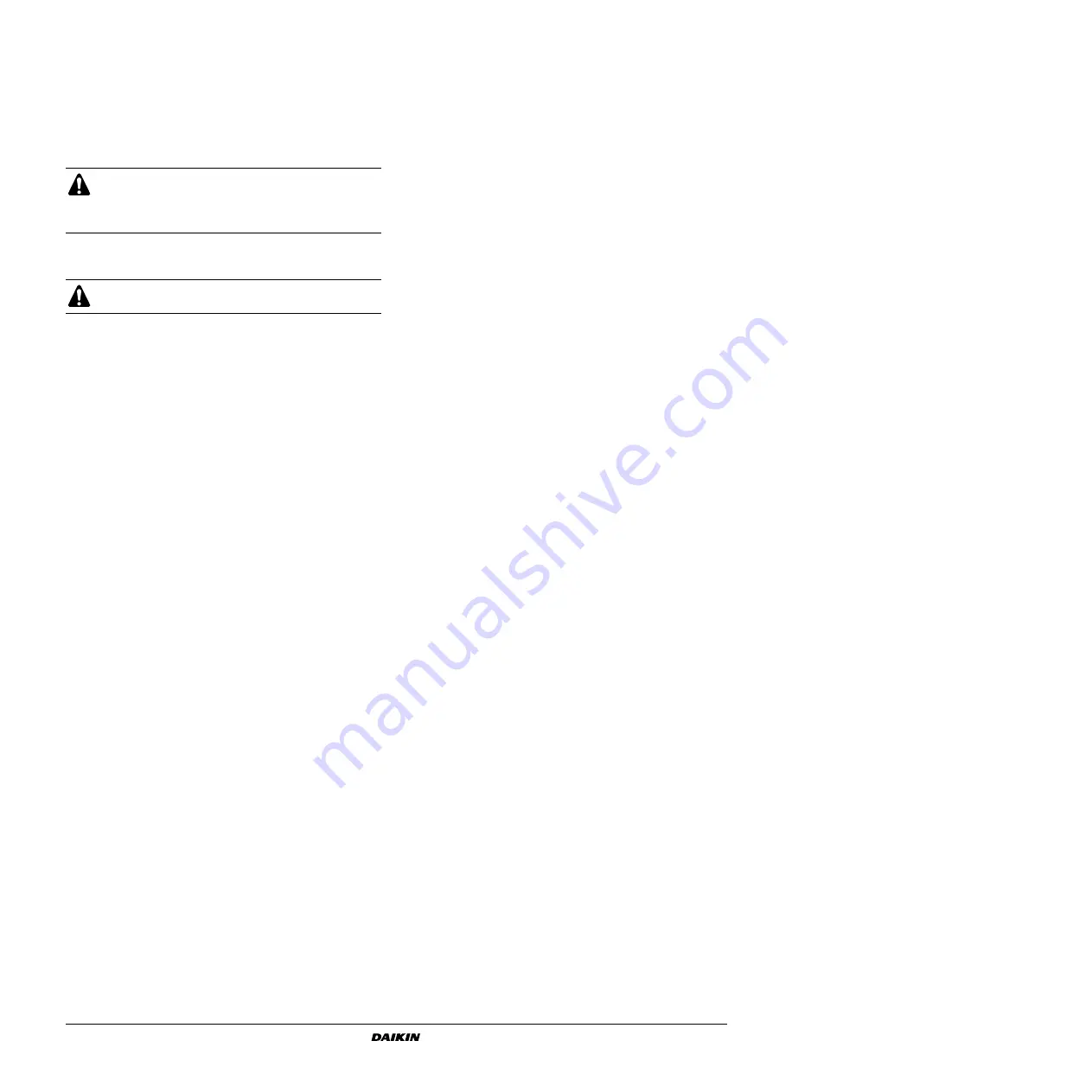
EWWD120~540MBYNN
Packaged water-cooled water chillers
4PW22685-1
Operation manual
20
M
AINTENANCE
In order to ensure optimal availability of the unit, a number of checks
and inspections on the unit and the field wiring have to be carried out
at regular intervals.
If the unit is used for air conditioning application, the described
checks must be executed at least once a year. In case the unit is
used for other applications, the checks should be executed every
4 months.
Maintenance activities
■
Air heat exchanger
Remove dust and any other contaminant from the coil fins using
a brush and a blower. Blow from the inside of the unit. Take care
not to bend or damage the fins.
■
Field wiring and power supply
•
Check the power supply voltage on the local supply panel.
The voltage must correspond to the voltage marked on the
identification label of the unit.
•
Check the connections and make sure they are properly
fixed.
•
Check the proper operation of the circuit breaker and the
earth leak detector provided on the local supply panel.
■
Internal wiring of the unit
Visually check the switch boxes on loose connections (terminals
and components). Make sure that the electrical components are
not damaged or loose.
■
Earth connection
Make sure that the earth wires are still connected properly and
that the earth terminals are tightened.
■
Refrigerant circuit
•
Check for leaks inside the unit. In case a leak is detected, call
your local dealer.
•
Check the working pressure of the unit. Refer to paragraph
"Switching the unit on" on page 8
(2).
■
Compressor
•
Check on oil leaks. If there is an oil leak, call your local dealer.
•
Check for abnormal noises and vibrations. If the compressor
is damaged, call your local dealer.
■
Water supply
•
Check if the water connection is still well fixed.
•
Check the water quality (refer to the installation manual of the
unit for specifications of the water quality).
■
Water filters
•
Make sure to clean the waterfilter in front of the evaporator
water inlet once every 4 months.
•
Check the filter for any possible damage and make sure that
the hole diameter size all over the filter surface is still 1.0 mm
maximum.
■
Water sensors
Check that all the water sensors are correctly fixed into the pipes
in front of the heat exchanger (see also the sticker attached to
the heat exchanger).
Disposal requirements
Dismantling of the unit, treatment of the refrigerant, of oil and of other
parts must be done in accordance with relevant local and national
legislation.
Before carrying out any maintenance or repair activity,
always switch off the circuit breaker on the supply panel,
remove the fuses or open the protection devices of the unit.
Do never clean the unit with water under pressure.
The wiring and power supply must be checked by a
licensed electrician.