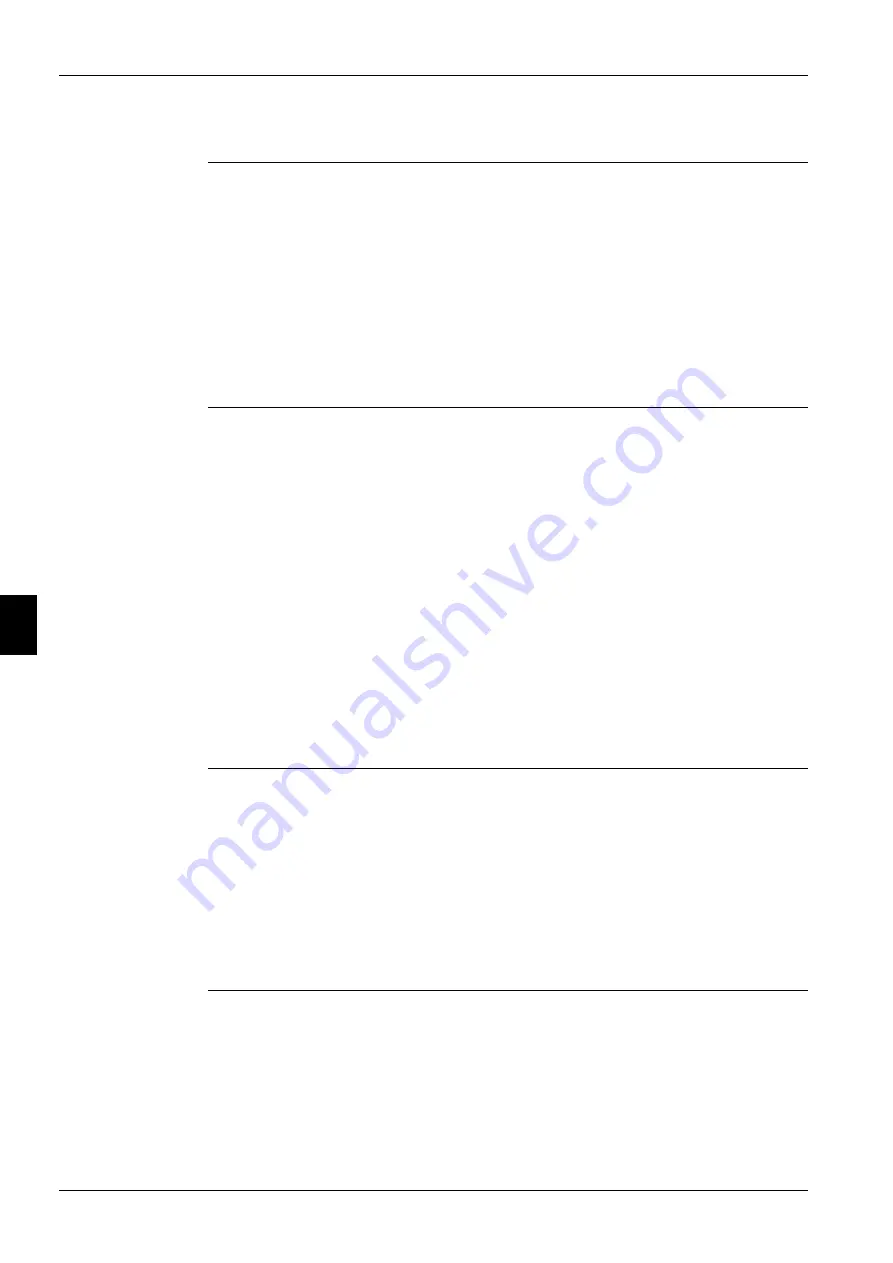
Maintenance
ESIE10-01
5–4
3
1
55
1.2
System Maintenance
Warning:
■
All routine and non-routine maintenance activities on the machine must be carried out solely by
qualified personnel who have been suitably trained and are familiar with the device, its operation
and maintenance, and who are aware of the safety requirements and risks involved.
■
It is absolutely forbidden to remove all the protections of the moving parts of the unit.
Attention:
■
The causes of repeated shut-downs deriving from triggering of safety devices must be investigated
and corrected. Simply re-starting the alarms may seriously damage the equipment.
■
A correct refrigerant and oil change is essential for optimal operation of the machine and for
environmental protection. Any oil and refrigerant recovery must conform to legislation in force.
General
■
Important:
Besides the checks suggested hereto, in order to keep the unit at optimal performance levels and
efficiency and prevent malfunction, it is recommended to schedule periodical inspections of the
unit by qualified personnel. Specifically, the following is recommended:
•
4 inspections per year (every three months) for units running about 365 days per year.
•
2 inspections per year (1 at seasonal start-up and the second mid-season) for units running
about 180 days per year.
•
1 inspection per year (at seasonal start-up) for units running about 90 days per year.
Regular checks and routine controls should be considered extremely important both during initial
start-up and regularly during operation. These checks also include suction and condensation
pressures, the sight glass on the liquid line and that the superheating and subcooling parameters, read
through the microprocessor installed on the machine, fall within the range of operating parameters.
A recommended ordinary maintenance programme is given at the end of this chapter, whilst an
operating data collection card is at the end of the manual. We recommend recording all machine
operating parameters on a weekly basis. The collection of this data will also be very useful for
technicians, should technical assistance be required.
Compressor
maintenance
■
Important:
Although the single-screw compressor is of a semi-hermetic type and therefore does not need
scheduled maintenance, for the purposes of keeping the compressor at optimal levels of perform-
ance and efficiency and to prevent malfunction, we recommend a visual check on the sate of sat-
ellite wear every 10000 hours of operation, and a measurement of satellite-screw coupling
tolerance. This inspection must be carried out by qualified, trained personnel.
Vibration analysis is a good method for verifying the mechanical conditions of the compressor.
Verification of vibration readings immediately after start-up and periodically on an annual basis is
recommended. The compressor load must be similar to the previous measurement's load to ensure
measurement reliability.
Lubrication
The units do not require a routine procedure for lubrication of components. The fan bearings are
permanently lubricated and as such no additional lubrication is required.
Compressor oil is synthetic and highly hygroscopic. It is therefore advised to limit its exposure to the
atmosphere during storage and filling. It is recommended that oil is exposed to the atmosphere for a
period of no more than 15 minutes. The compressor oil filter is positioned above the oil separator
(delivery side). Replacement is recommended when its pressure drop exceeds 2.0 bar. The pressure
drop across the oil filter is the difference between the compressor discharge pressure and oil pressure.
Both these pressures can be monitored through the microprocessor for both compressors.
Summary of Contents for EWAD620-C17C-SS
Page 2: ......
Page 8: ...ESIE10 01 1 2 Part 1 System Outline 3 1 1 5...
Page 111: ...ESIE10 01 General Outline Part 1 System Outline 1 105 3 1 4 5 1 36 1 Power Compressor 1 2...
Page 112: ...General Outline ESIE10 01 1 106 Part 1 System Outline 3 1 1 4 5 1 36 2 Power Compressor 3...
Page 113: ...ESIE10 01 General Outline Part 1 System Outline 1 107 3 1 4 5 1 36 3 Kit Pumps...
Page 122: ...General Outline ESIE10 01 1 116 Part 1 System Outline 3 1 1 4 5 1 36 12 Digital Inputs Board...
Page 123: ...ESIE10 01 General Outline Part 1 System Outline 1 117 3 1 4 5 1 36 13 Digital Outputs Board...
Page 124: ...General Outline ESIE10 01 1 118 Part 1 System Outline 3 1 1 4 5 1 36 14 Digital Outputs Board...
Page 127: ...ESIE10 01 General Outline Part 1 System Outline 1 121 3 1 4 5 1 36 17 Extension Control Fans 4...
Page 131: ...ESIE10 01 General Outline Part 1 System Outline 1 125 3 1 4 5 1 36 21 EEXV Compressor 1...
Page 134: ...General Outline ESIE10 01 1 128 Part 1 System Outline 3 1 1 4 5 1 36 24 EEXV Compressor 2...
Page 137: ...ESIE10 01 General Outline Part 1 System Outline 1 131 3 1 4 5 1 36 27 EEXV Compressor 3...
Page 138: ...General Outline ESIE10 01 1 132 Part 1 System Outline 3 1 1 4 5 1 36 28 Pumps Control...
Page 139: ...ESIE10 01 General Outline Part 1 System Outline 1 133 3 1 4 5 1 36 29 Terminals M1 M2...
Page 140: ...General Outline ESIE10 01 1 134 Part 1 System Outline 3 1 1 4 5 1 36 30 Terminals M3...
Page 141: ...ESIE10 01 General Outline Part 1 System Outline 1 135 3 1 4 5 1 36 31 Terminals M5 MQ...
Page 148: ...General Outline ESIE10 01 1 142 Part 1 System Outline 3 1 1 4 5...
Page 150: ...ESIE10 01 2 2 Part 2 Functional Description 3 1 2 5...
Page 170: ...The Digital Controller ESIE10 01 2 22 Part 2 Functional Description 3 1 2 4 5...
Page 200: ...Functional Control ESIE10 01 2 52 Part 2 Functional Description 3 1 2 4 5...
Page 202: ...ESIE10 01 3 2 Part 3 Troubleshooting 3 1 3 5...
Page 254: ...Alarms and Events ESIE10 01 3 54 Part 3 Troubleshooting 3 1 3 4 5...
Page 266: ...Controller Inputs and Outputs ESIE10 01 3 66 Part 3 Troubleshooting 3 1 3 4 5...
Page 280: ...ESIE10 01 4 2 Part 4 Commissioning and Test Run 3 1 4 5...
Page 286: ...Pre Test Run Checks ESIE10 01 4 8 Part 4 Commissioning and Test Run 3 1 4 5...
Page 289: ...ESIE10 01 Running Data Part 4 Commissioning and Test Run 4 11 3 4 5 1...
Page 290: ...Running Data ESIE10 01 4 12 Part 4 Commissioning and Test Run 3 1 4 5...