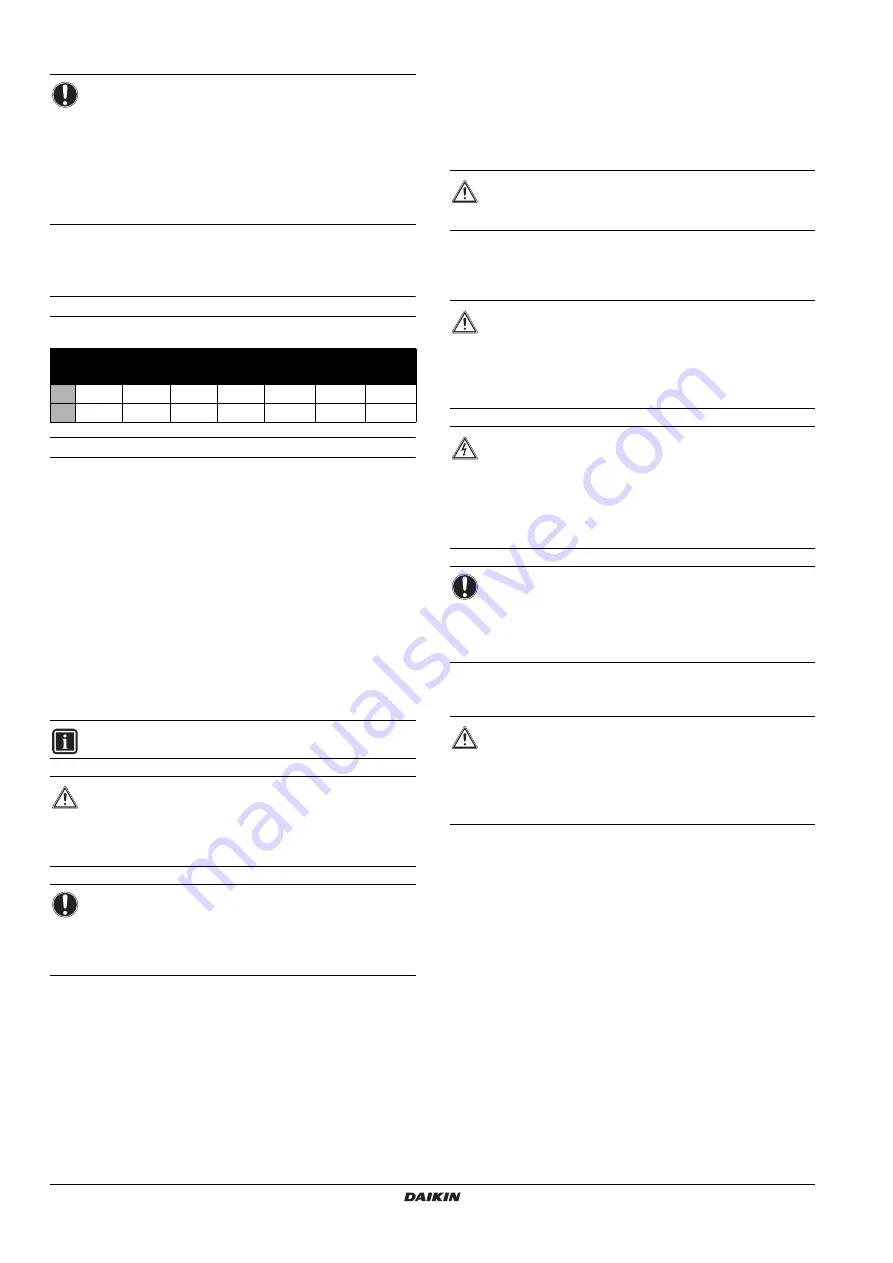
Installation manual
19
ERHQ011~W1 + ERLQ011~W1
Outdoor unit for air to water heat pump
4PW57794-1 – 08.2010
12.5. Complete recharging
In case complete recharging is required (after a leak, etc.), refer to
the information below to determine the necessary amount of
refrigerant.
For ERHQ only
Table 3:
Total charging amount <unit: kg>
For ERLQ only
Total charging amount <unit: kg>
Charge of refrigerant (kg) depends on total liquid piping length.
Total refrigerant charge = 3.4 kg + (total length (m) of liquid piping
– 10 m) x 0.054
Remark: Factory refrigerant charge is 3.4 kg
13. P
UMP
DOWN
OPERATION
This unit is equipped with an automatic pump down operation which
will collect all refrigerant from the field piping and indoor unit in the
outdoor unit. To protect the environment, make sure to perform the
following pump down operation when relocating or disposing of the
unit.
1
Turn on the main power supply switch.
2
Make sure the liquid stop valve and the gas stop valve are open
(see
"9.3. Stop valve operation" on page 15
3
Press the pump down button (BS4) on the PCB of the outdoor
unit for at least 8 seconds.
4
The compressor and outdoor unit fan will start operating
automatically.
5
Once operation stops (after 3 to 5 minutes), close the liquid stop
valve and the gas stop valve.
6
The pump down operation is now finished. The remote controller
may display
"
U4
"
and the indoor pump may continue operating.
This is not a malfunction. Even when the ON button on the
remote controller is pressed, the unit will not start to operate. To
restart operation of the unit turn off the main power supply
switch and turn it on again.
7
Turn off the main power supply switch.
14. E
LECTRICAL
WIRING
WORK
14.1. Precautions on electrical wiring work
■
Use only copper wires.
■
A main switch or other means for disconnection, having a
contact separation in all poles, must be incorporated in the fixed
wiring in accordance with applicable legislation.
Do not turn on the main switch until all the wiring is completed.
■
Never squeeze bundled cables into a unit.
■
Fix cables so that cables do not make contact with the pipes
(especially on high pressure side).
■
Secure the electrical wiring with cable ties as shown in the figure
in chapter
"14.2. Connecting power supply and interunit wiring"
so that it does not come in contact with the piping,
particularly on the high-pressure side.
Make sure no external pressure is applied to the terminal
connectors.
■
When installing the earth leakage circuit breaker make sure that
it is compatible with the inverter (resistant to high frequency
electrical noise) to avoid unnecessary opening of the earth
leakage circuit breaker.
NOTICE
Before recharging, make sure to execute vacuum drying of
the internal piping of the unit as well. To do so, use the
internal service port of the unit. Do NOT use the service
ports located on the stop valve (see
), since vacuum drying can not be
performed properly from these ports.
Outdoor units have 1 port on the piping. It is between the
heat exchanger and the 4-way valve.
Refrigerant piping length
3~10 m
10~20 m 20~30 m 30~40 m
40~50 m
50~60 m
60~75 m
V3
2.7
3.2
3.7
4.2
4.7
5.2
5.7
W1
2.95
3.45
3.95
4.45
4.95
5.45
5.95
For more details, refer to the applicable service manual.
WARNING
The outdoor unit is equipped with a low pressure switch or
a low pressure sensor to protect the compressor by
switching it off. Never short-circuit the low pressure switch
during pump down operation!
NOTICE
Before pumpdown is activated be sure that the water
temperature and water volume is sufficiently high.
Pumpdown is done in "cooling mode". See installation
manual of the indoor unit for more details.
WARNING
Make sure to re-open both stop valves before restarting
operation of the unit.
WARNING
■
All wiring must be performed by an authorized
electrician.
■
All components procured on the site and all electric
construction shall comply with the applicable
legislation.
DANGER: HIGH VOLTAGE
To avoid electrical shock, make sure to disconnect the
power supply 1 minute or more before servicing the
electrical parts. Even after 1 minute, always measure the
voltage at the terminals of main circuit capacitors or
electrical parts and, before touching, make sure that those
voltages are 50 V DC or less.
NOTICE
To persons in charge of electrical wiring work:
Do not operate the unit until the refrigerant piping is
complete. (Running it before the piping is ready will break
the compressor.)
DANGER
■
Before obtaining access to terminal devices, all
supply circuits must be interrupted.
■
Be sure to install an earth leakage circuit breaker in
accordance with applicable legislation. Failure to do
so may cause electrical shock.