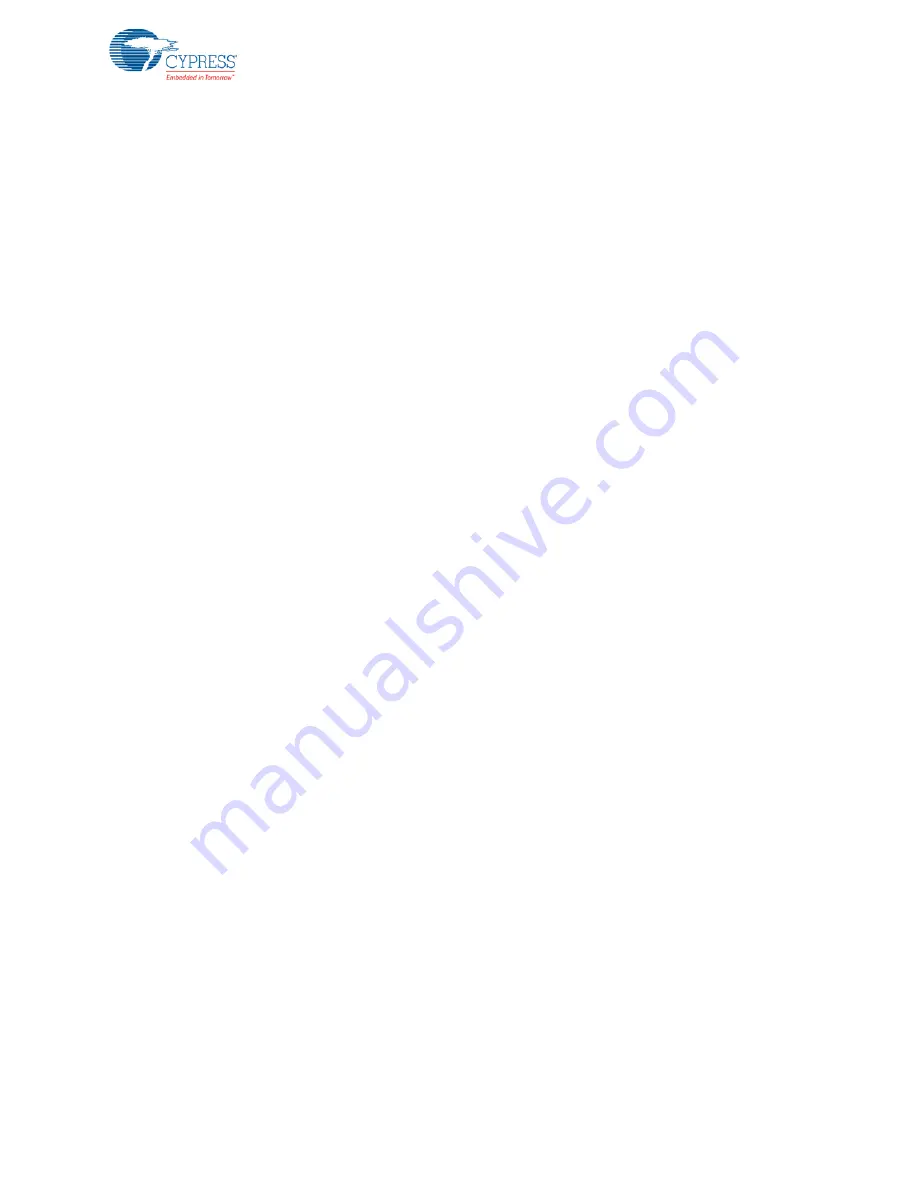
CY8CKIT-025 PSoC® Precision Analog Temperature Sensor Expansion Board Kit Guide, Doc. # 001-65791 Rev. *J
75
Example Projects
4. Open the ThermalManagementSystem_001 project using PSoC Creator and select
Debug >
Program
to program PSoC 3.
5. Detach the MiniProg3 and remove power supply to the PSoC DVK.
6. Connect the CY8CKIT-025 EBK and TME EBK to the PSoC DVK, as shown in
7. Power the PSoC DVK and TME EBK, as shown in
8. Press the
Reset
(SW4) button on the PSoC 3 DVK to run the newly programmed firmware
image.
9. On reset, the LCD displays a welcome message and starts with the Zone 1 temperature reading
and the corresponding temperature calculation algorithm. The desired and actual fan speeds cor-
responding to that zone are also displayed.
10.Use the push button SW1 to view the different zone characteristics.
5.4.2.3
Testing the Project
In this project, the fan temperature is controlled based on the temperature of the corresponding ther-
mal zone. To test the closed loop speed control of Fan 3, vary the potentiometer on the DVK. This
simulates the condition of changing the corresponding zone temperature in the project. The speed of
Fan 3 is adjusted according to the temperature vs speed graph shown in
. To test the
closed loop speed control of Fan 4, touch the RTD sensor on the CY8CKIT-025 EBK. This results in
variations in the measured RTD temperature. The speed of Fan 4 is adjusted according to the tem-
perature vs speed graph shown in
On reset, the LCD displays the characteristics of Zone 1. These characteristics include the zone
temperature, temperature calculation algorithm, desired fan speed, and the actual fan speed. The
fan speeds will match the corresponding zone thermal profiles. Press the push button (SW1 on
CY8CKIT-001 or SW2 on CY8CKIT-030) once to view the characteristics of Zone 2. Press the push
button (SW1 on CY8CKIT-001 or SW2 on CY8CKIT-030) again to view the individual sensor temper-
atures for each zone and the weighted composite zone temperature. Pressing the button again will
repeat this display sequence.
5.4.3
Project Details
This project demonstrates how the temperature sensors in the CY8CKIT-025 EBK combined with
the fans on the TME EBK can create a complete thermal management system. The example shows
how to combine temperature readings from a number of temperature sensors in a variety of ways
and use the composite temperature to set desired fan speeds according to a customizable transfer
function.
The thermal management example uses the concept of a "Thermal Zone", which describes how to :
■
combine multiple temperature sensor readings to form a composite zone temperature
■
map the zone temperature to a fan speed
By this definition, each fan is controlled according to its own independent thermal zone. This exam-
ple has two thermal zones because the TME EBK has only two fans installed. Algorithms currently
implemented to combine multiple temperature sensors into a composite zone temperature include:
straight average, weighted average, and maximum.
In this example, the weighted method is used on both fans. A zone temperature-to-fan speed trans-
fer function is then definable for each zone. Linear and table driven transfer functions are currently
implemented. This example uses the table driven transfer function on both fans; that is, a look-up
table maps the composite zone temperature-to-fan speed.
This example is a simulation of a thermal management system. Zone 1, corresponding to Fan 3 in
combines temperature measurements from two temperature sensors (potentiometer