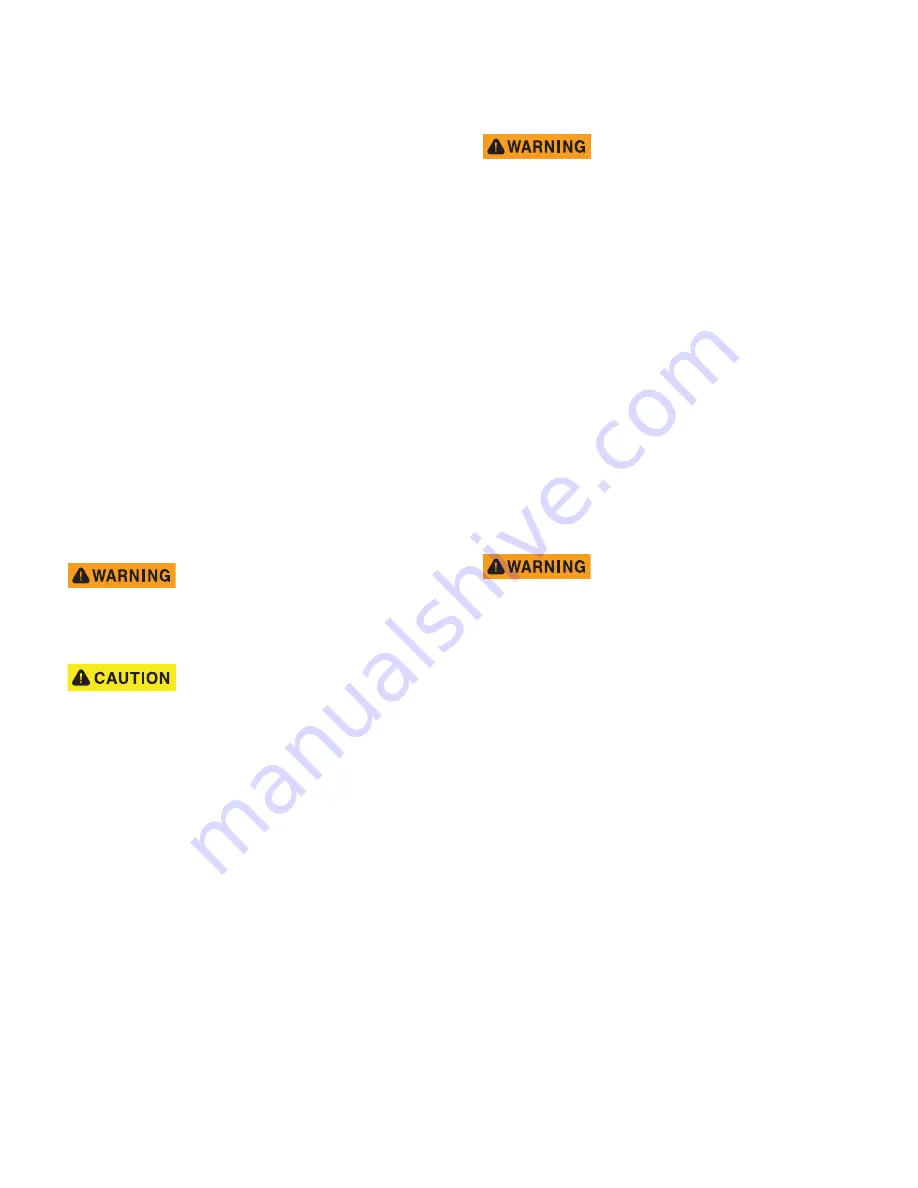
B
REAR HYDRAULIC REAR HYDRAULIC BRAKES
Read all of SAFETY and this section before attempting any procedure. Pay particular attention to Notices, Cautions, Warnings and Dangers.
71
Repair and Service Manual
653045
WHEEL BRAKE SERVICE
Tool List
Quantity
Dust Mask ................................................................... 1
Safety Glasses ............................................................ 1
Socket, 3/4" ................................................................. 1
Ratchet ........................................................................ 1
Wheel Chocks ............................................................. 4
Hydraulic Floor Jack.................................................... 1
Jack Stands................................................................. 2
Brush ........................................................................... 1
Wheel Cylinder Clamp................................................. 1
Pliers ........................................................................... 1
Wrench, 9/16".............................................................. 1
Wrench, 10 mm ........................................................... 1
Shop Towels ............................................................. AR
Socket, 7/16", 3/8"....................................................... 1
Torque Wrench, in. lbs................................................. 1
Wire Brush................................................................... 1
Grease...................................................................... AR
High Temperature Lubricant ..................................... AR
Socket, 10 mm, 3/8" .................................................... 1
Socket, 9/16", 3/8"....................................................... 1
Locking Pliers .............................................................. 1
Thread Locking Compound ...................................... AR
Wear a dust mask and eye protec-
tion whenever working on wheel
brakes. Do not use pressurized air
to blow dust from brake assemblies. Replace both
brake shoes on both wheels if one or more shoes
are worn below .06" (1.5mm) thickness at any point.
Do NOT touch any of the wheel
brake mechanism except as
instructed.
Do NOT use a commercial brake cleaner unless the
entire brake has been disassembled.
Be sure that the parking brake is released.
Loosen rear wheel lug nuts and lift rear of vehicle as per
SAFETY section. Remove wheel, wheel drum and hub
assembly (Figure 1). Refer to ‘Brake Drum Removal and
Installation’ in this section. Remove excess dust and dirt
from the drum with a brush.
Remove any accumulated brake dust from the wheel
brake assembly with a brush.
Install wheel cylinder clamp, then unhook upper and
lower shoe to shoe springs.
Remove parking brake strut and lever.
Remove shoe hold-down springs and remove shoes.
If the wheel cylinder must be removed, begin by loosen-
ing and removing the brake line from the back of the
wheel cylinder. Next remove the wheel cylinder bolts and
remove the wheel cylinder from the backing plate.
Cleaning and Inspection
The drum must not be machined to
remove grooves. Turning will make
the drum too thin causing drum and
brake failure which could cause severe injury or
death.
A backing plate assembly that shows any indication
of galling or gouging is not repairable and must be
replaced with a new wheel brake assembly. Always
replace wheel brake assemblies in pairs.
Inspect the brake drum. Look for a blue coloration or blis-
tered paint that would indicate that it has overheated.
Check for evidence of scoring. Check for excessive wear
indicated by the friction surface being significantly worn
and leaving a ledge of unworn drum. Inspect the splines
for galling, wear and corrosion. If any of these problems
are found, the drum must be replaced.
Visually inspect the axle seal for oil leakage and the con-
dition of the thrust washer. If oil is present, refer to REAR
AXLE section.
Verify the inner brake drum washer is present and check
its condition. Replace if damaged or missing.
Clean the backing plate with an approved cleaner for this
purpose.
A backing plate assembly that
shows any indication of galling or
gouging is not repairable and must
be replaced with a new wheel brake assembly.
Always replace wheel brake assemblies in pairs.
Inspect the backing plate. Inspect for gouges, galling or
other damage, particularly where the backing plate is
contacted by the brake shoes. Be sure shoe ledges are
smooth and free of rough edges. Replace both wheel
brake assemblies if any gouges or galling is found.
Measure the brake shoe thickness. Measure at the most
worn area. Brake shoe thickness must never be less than
.06" (1.5 mm) at any point on the shoe. It is normal for the
shoes to show more wear at the leading and trailing
edges. If the brake shoe thickness is approaching .06"
(1.5 mm), it is recommended that the shoes be replaced.
It is recommended that the brake shoe springs and brake
adjusters be replaced when installing new brake shoes
Check springs for loss of tension and damage. Replace
weak springs and any damaged or badly worn parts.
Check adjuster operation. Ensure that each adjuster will
move with approximately 30 - 50 in. lbs. (3.4 - 5.6 Nm) of
torque. If adjusters are frozen, badly worn or loose,
replace the adjuster assembly.
Replace the wheel cylinder if there is any sign of leakage.
Ensure that the parking lever and strut assembly can be
easily moved by hand. If necessary, this assembly can be
serviced as follows:
Property of American Airlines