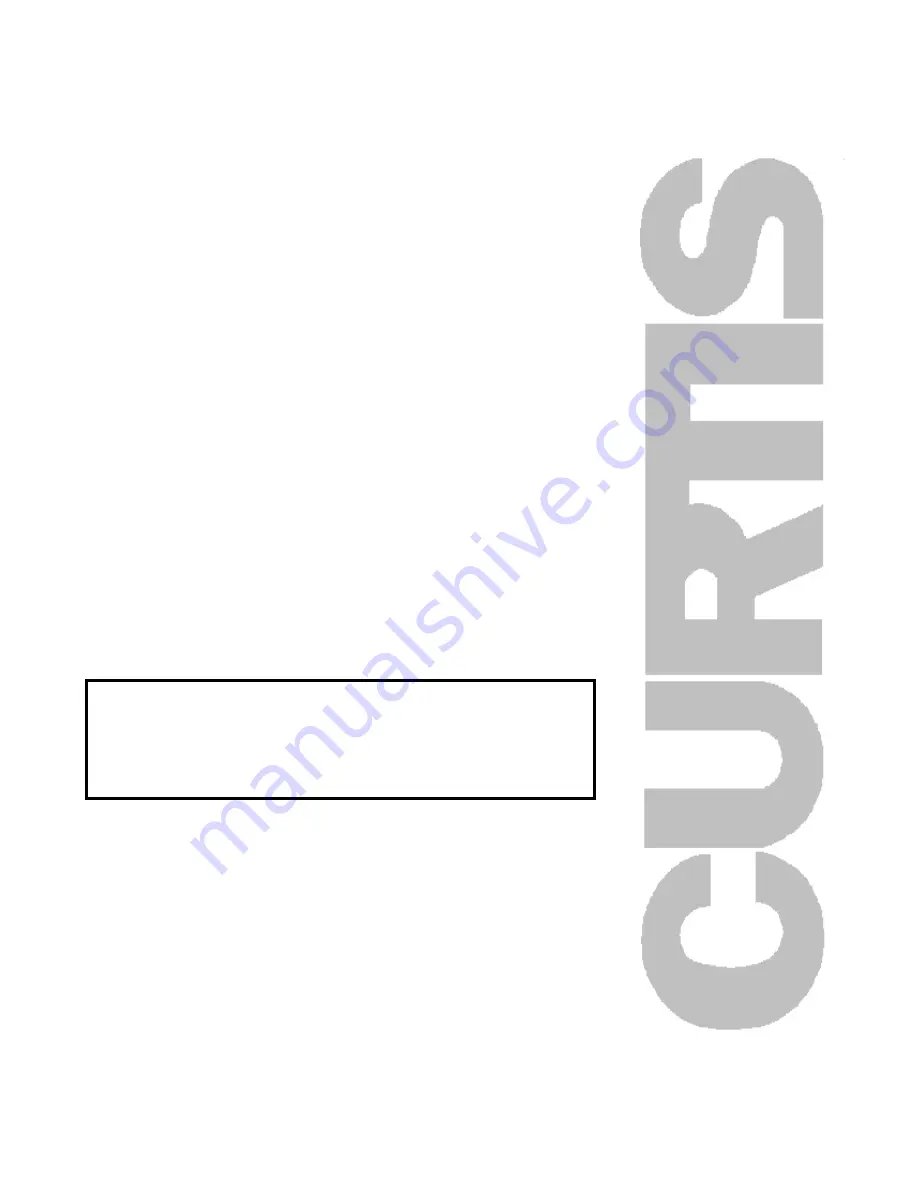
CAP-215
APRIL, 2003
REV. D
OIL-LESS COMPRESSOR
OPERATION AND INSTRUCTION
MANUAL
OIL-LESS
COMPRESSOR MODELS
OL 512 SINGLE STAGE
3 H.P.
OL 512 SINGLE STAGE
5 H.P.
OL 524 TWO STAGE
5 H.P.
OL 812 SINGLE STAGE
7 1/2 H.P.
OL 812 SINGLE STAGE
10 H.P.
CAUTION
Before installing this compressor, read and understand
the safety precautions contained within this manual
CURTIS - TOLEDO, INC.
1905 Kienlen Avenue, St. Louis, Missouri 63133,
PHONE(314)383-1300 ----- FAX (314)381-1439
Summary of Contents for OL 512
Page 34: ...CAP 215 21 Instruction Manual Oil Less Compressors 7 SAFETY REGULATIONS 7 1 GENERAL...
Page 35: ...CAP 215 22 Instruction Manual Oil Less Compressors...
Page 47: ...CAP 215 Fig 19 2 stage compressor dimensions 070308 1015 34...
Page 48: ...CAP 215 35 Fig 20 1 stage compressor dimensions 070307 1015...
Page 49: ...CAP 215 36 Fig 21 1 stage compressor dimensions 077734...