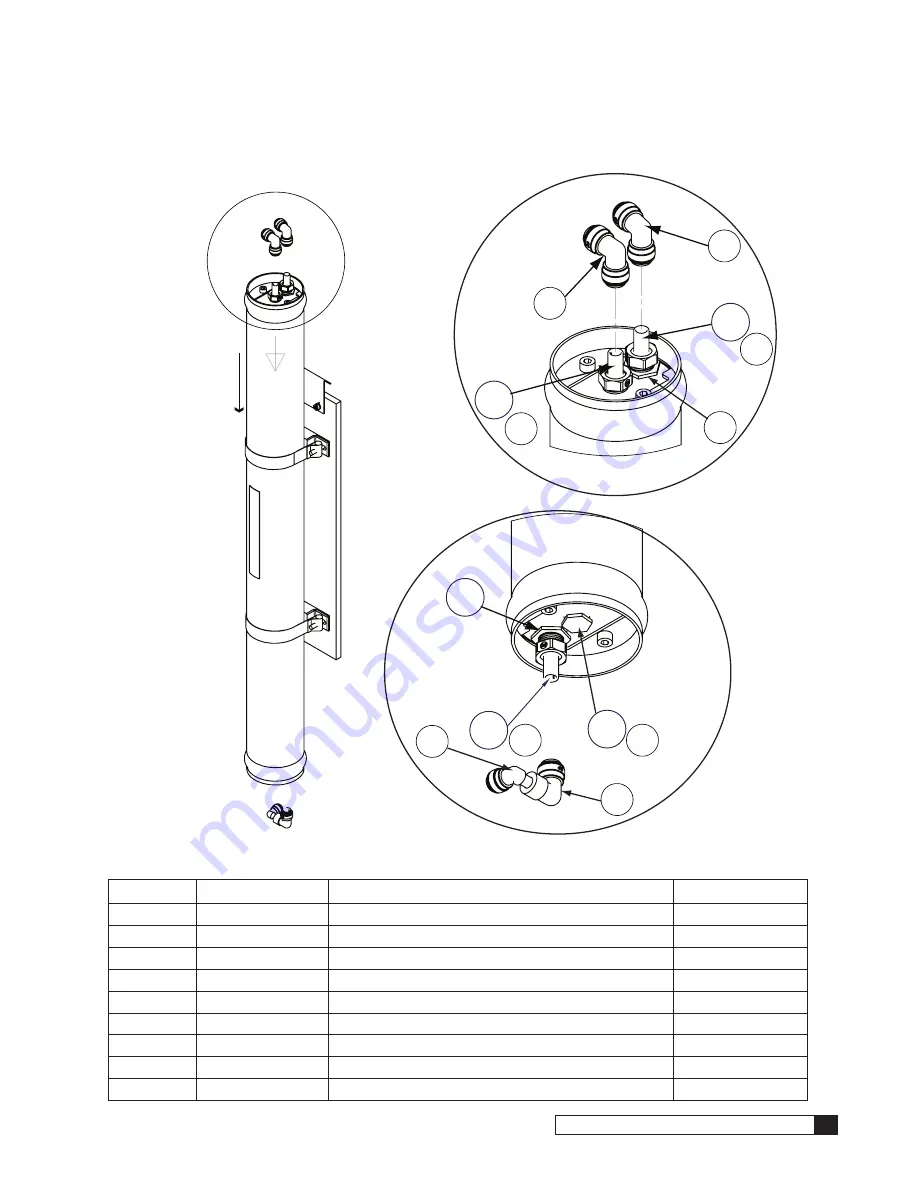
M1 RO Parts Diagrams and Lists
55
Cat. No. 01022940
1F Sub-Assembly
Bottom View
6
Note
Direction
of Flow
2
B
C
5
A = to Feed Port
B = to Recirculating Assy
C = to Center Port (Product)
4
Top View
C
FEED
PRODUCT
A
4
3
3
4
6
1
Figure 37.
M1-1F sub-assembly.
Item
Part No.
Description
Quantity
01022875
Assembly, Membrane Housing, Single, 4.0"x40"
01023922
Kit, Tube and Fittings, 1F (includes items 1–7)
1
—
Elbow, Union, Reducing, 1/2 x 3/8, PI, Polypropylene
1 EA
2
—
Elbow, Plug In, 3/8" stem, 3/8 tube
1 EA
3
—
Elbow, Union, 1/2 Tube, Polypropylene
2 EA
4
—
Stem Adapter, 1/2Tx1/2 Stem, Polypropylene
3 EA
5
—
Plug, 1/2" NPT, PVC Sch 80
1 EA
6
—
BUSHING,3/4x1/2,TxT,PVC SCH.80,
2 EA
7
—
Carton, Tubing and Fittings Kit
1 EA
Summary of Contents for M1 Series
Page 83: ...Notes 79 Cat No 01022940 Notes ...
Page 84: ......