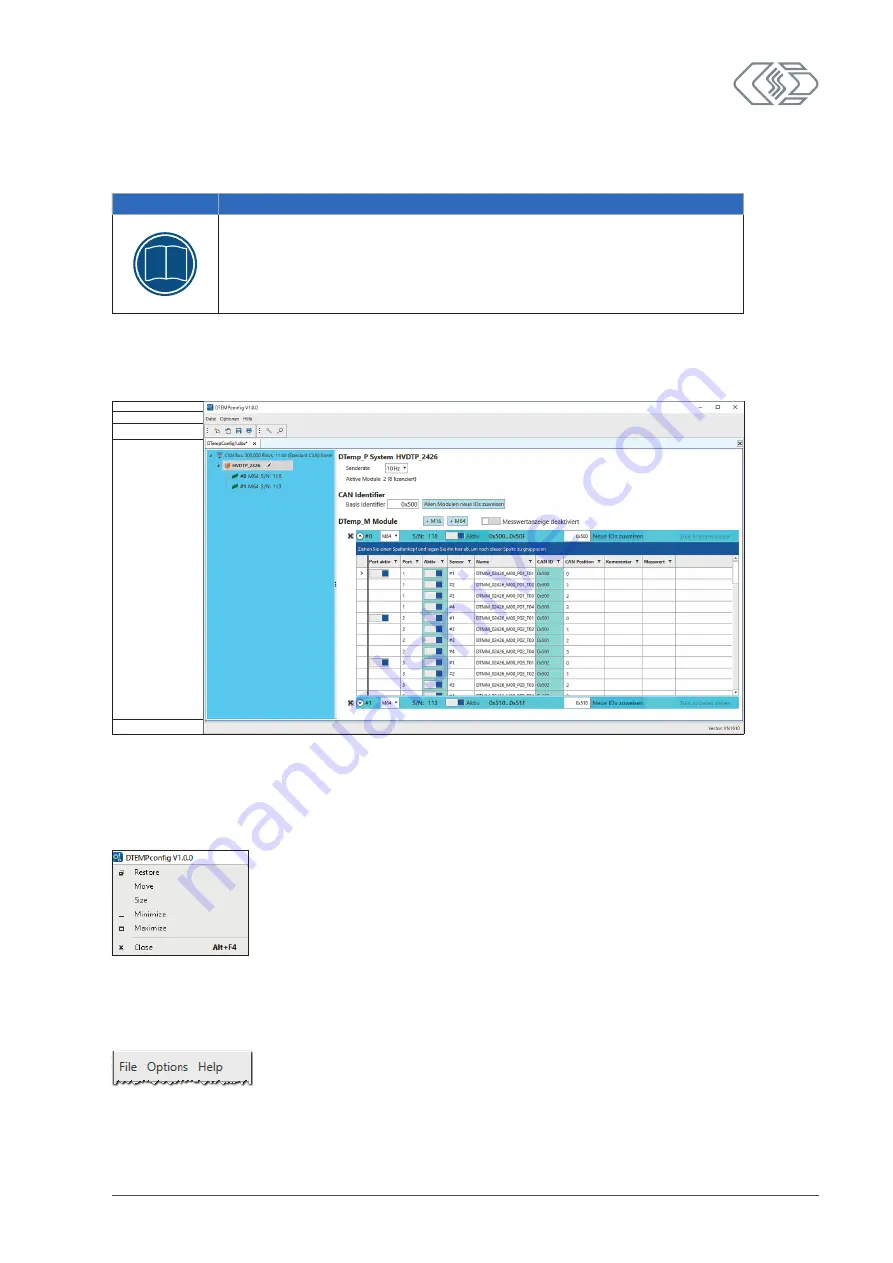
HV DTemp Measurement System – Using a HV DTemp Measurement System
User Guide
29
Version 01.00 // 2021
5.2 Configuration software DTEMPconfig
NOTE!
i
A configuration document (DBC file) is included in the scope of delivery
of a HV DTemp measuring system. If the configuration document has to
be changed, the configuration software DTEMPconfig is required. This
software is available at CSM for a license fee. For further details please
contact the sales department..
5 2 1 DTEMPconfig user interface
The DTEMPconfig software is used for the configuration of HV DTemp measurement systems.
The DTEMPconfig user interface consists of the following sections:
Header
Menu bar
Toolbar
Working space with
layout window
Status bar
Fig. 5-2: DTEMPconfig user interface
Header
Clicking the program icon on the left opens the program menu. The program menu provides
the usual functions for modifying the position and resizing of the program window.
Fig. 5-3: Program menu
Menu bar
The commands are arranged in the following menus:
Fig. 5-4: Menu bar
→ See DTEMPconfig online help for further information on the menu commands.