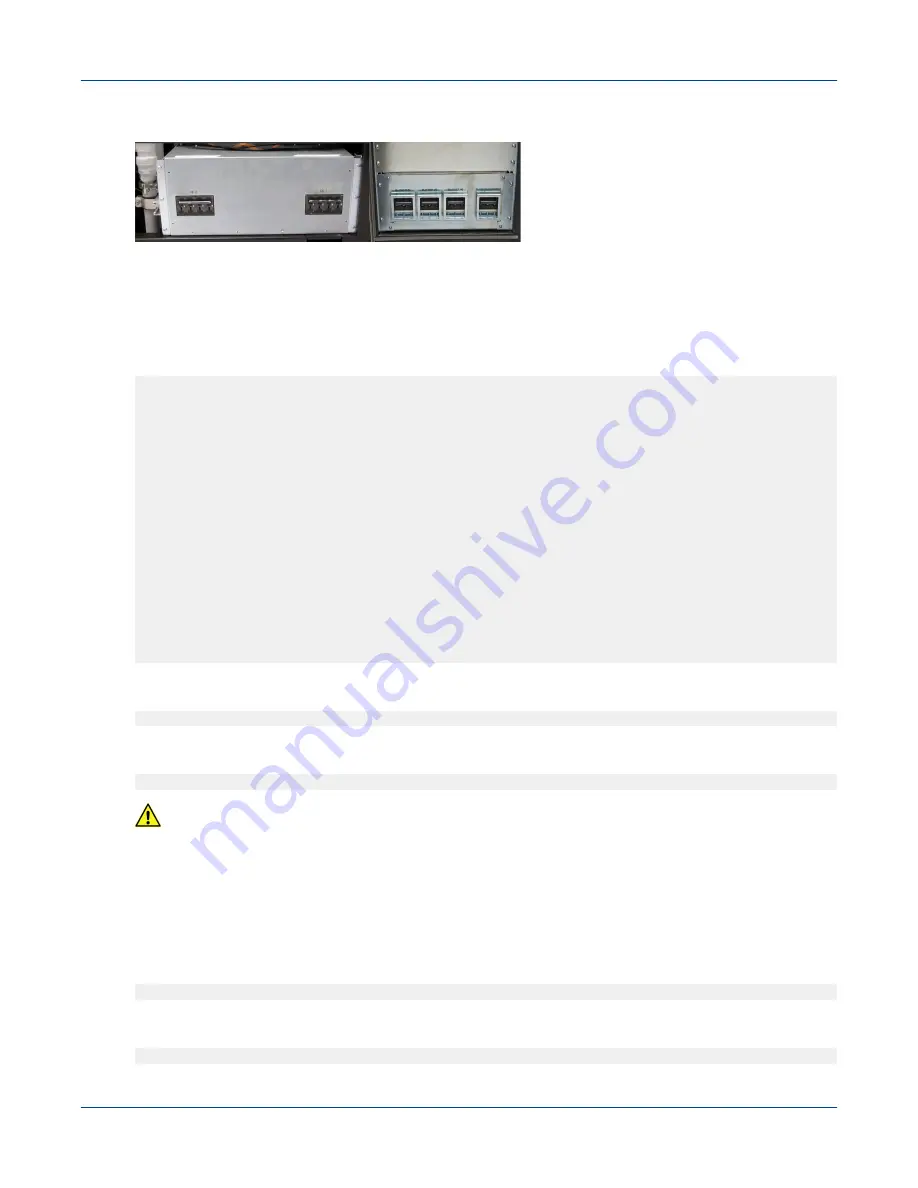
Figure 75. Circuit Breakers for Cabinet (left) and Blower (right)
2. Stop the MODBUS communication to the actuator while the actuator is replaced from the SMW.
a. Determine the manual valve position for the site. Run the
xtrsh
command to determine the systems
current water valve position. Use the largest percentage.
Site water temperatures vary, therefore, the manual valve position must be determined for each site.
smw$
xtrsh -l root -b -m ‘-[0-9]{1,}$’ -s’/opt/cray/bin/ccsysd-Q’ | grep
“Water valve Position”
c3-1 ! ** Message: Compute Cab Water Valve Position: 42.00 pct
c4-0 ! ** Message: Compute Cab Water Valve Position: 40.00 pct
c6-0 ! ** Message: Compute Cab Water Valve Position: 38.00 pct
c6-1 ! ** Message: Compute Cab Water Valve Position: 44.00 pct
c1-0 ! ** Message: Compute Cab Water Valve Position: 46.00 pct
c4-1 ! ** Message: Compute Cab Water Valve Position: 42.00 pct
c7-0 ! ** Message: Compute Cab Water Valve Position: 39.00 pct
c2-0 ! ** Message: Compute Cab Water Valve Position: 38.00 pct
c1-1 ! ** Message: Compute Cab Water Valve Position: 40.00 pct
c0-1 ! ** Message: Compute Cab Water Valve Position: 38.00 pct
c7-1 ! ** Message: Compute Cab Water Valve Position: 42.00 pct
c0-0 ! ** Message: Compute Cab Water Valve Position: 33.00 pct
c2-1 ! ** Message: Compute Cab Water Valve Position: 44.00 pct
c3-0 ! ** Message: Compute Cab Water Valve Position: 36.00 pct
c5-0 ! ** Message: Compute Cab Water Valve Position: 38.00 pct
c5-1 ! ** Message: Compute Cab Water Valve Position: 44.00 pct
b. Log in to each cabinet controller.
smw$
xtlogin cX-Y
c. Change the cabinet directory.
smw$
cd /sys/kernel/micro/commands/compute_cabinet
d.
CAUTION:
●
Equipment damage
●
The actuator must return to automatic mode during the installation. Failure to return the
actuator to automatic mode can result in equipment damage.
From the current directory, enable manual mode.
0 = manual and 1 = automatic
smw$
echo 0 > temp_close_loop
e. Set the valve to the value.
smw$
echo 49 > manual_valve_pos
System Cabinet Procedures
81